Manufacturing Pressure-Sensitive Adhesive Products: A Coating and Laminating Process
How are pressure-sensitive adhesives made?
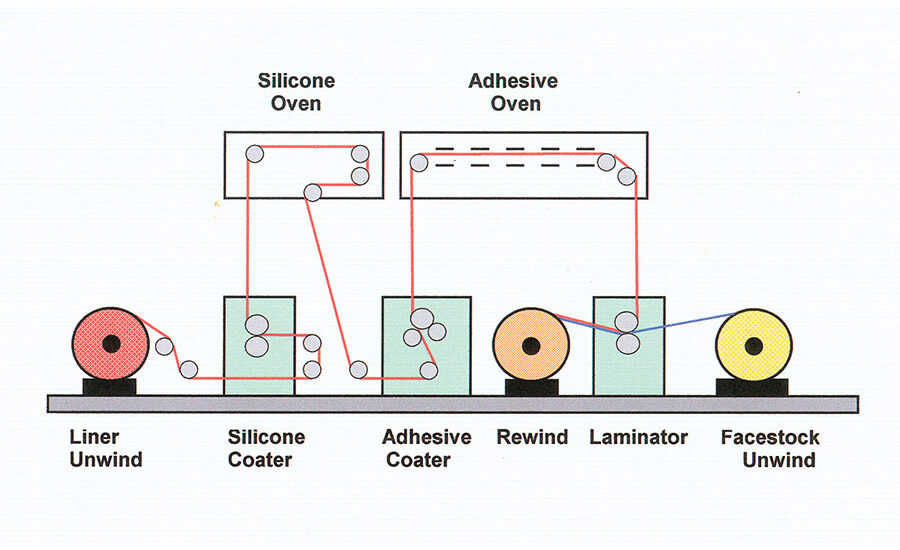
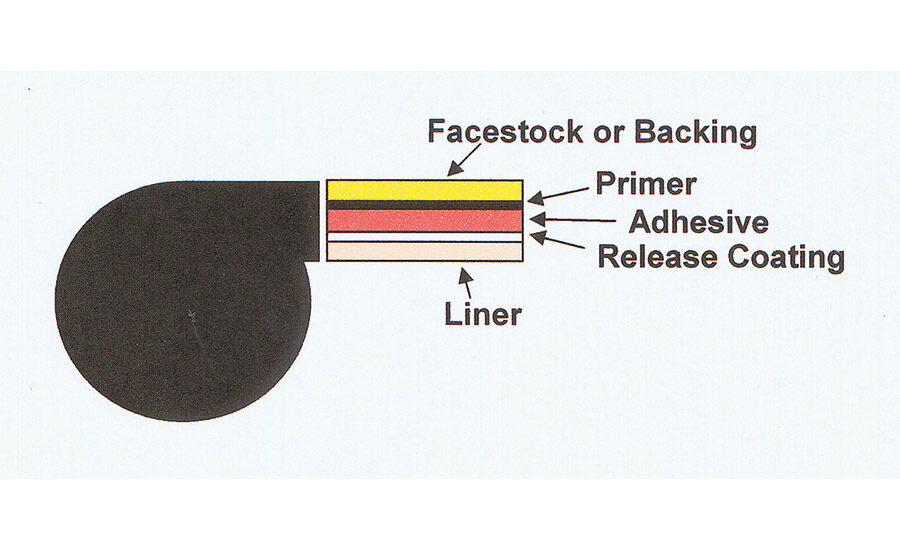
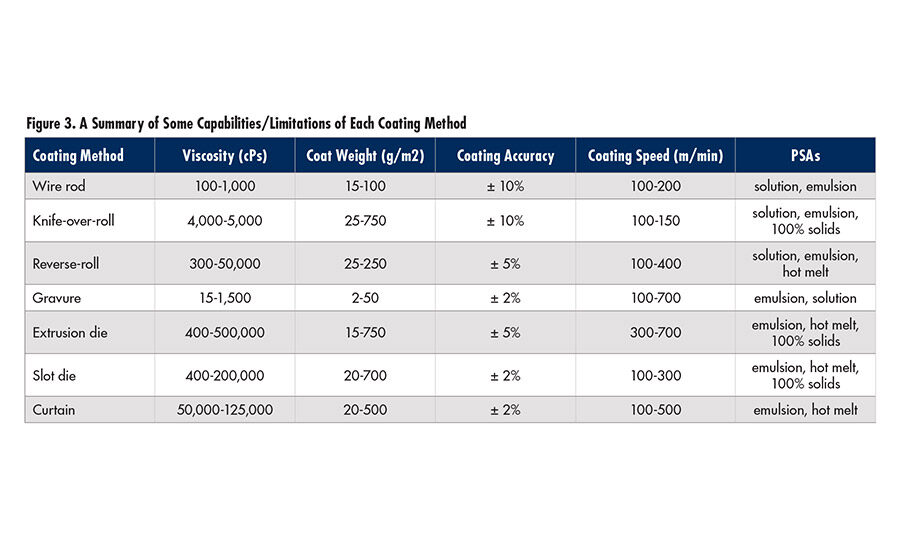



Pressure-sensitive adhesives (PSAs) have become a part of everyday life. We find them on many of the products we purchase as primary labels, price stickers and UPC labels. We use them in the form of plastic bandages, duct tape and clear package sealing tape. We know what we use them for, but how are they made?
PSAs are a combination of several materials that come together to form a "construction." A PSA construction is a combination of layers including a facestock (label) or backing (tape), an optional primer coat, an adhesive, and a silicone release coating on a protective liner. The PSA construction—whether a label, tape or transfer adhesive—is manufactured through several coating and laminating steps, including liner-release coating, adhesive coating/drying/curing, optional facestock or backing primer coating, and lamination of the facestock or backing to the liner.
One of the least-discussed aspects of PSAs is that of adhesive coating and adhesive coating methods. The objective of adhesive coating is simply to uniformly deposit a pressure-sensitive adhesive onto a web substrate. There are two principal PSA coating techniques: 1) Direct coating in which the pressure-sensitive adhesive is coated directly onto the facestock or backing material, and 2) Transfer coating in which the adhesive is first coated onto a release coated liner and transferred to the facestock or backing during the facestock/backing-to-liner lamination process.
The production of PSAs is principally the coating and laminating process. Primary coating and laminating is accomplished on a coating line and produces an adhesive sandwich. PSA coaters are typically tandem coaters on which the two separate substrate webs (facestock/backing) and liner are processed simultaneously prior to laminating them together. Processing of the liner often includes application and drying of the release coating. Processing of the facestock/backing may include application and drying of a primer coat. Actual adhesive coating may be done through direct application to the facestock/backing or by transfer application to the liner. The facestock/backing and liner webs are then laminated together to form the PSA sandwich.
Figure 1 is a simplified depiction of a typical PSA coating and laminating production line. Figure 2 is a depiction of a typical coated and laminated PSA construction in roll form.
A number of adhesive coating methods are used for coating pressure-sensitive adhesives. Many are pre-metered methods in which the thickness of the adhesive is determined prior to the actual application of the PSA to the web substrate, while other methods are post-metered methods in which the thickness of the PSA is determined after the adhesive has been applied to the web substrate.
The actual choice of which adhesive coating technique and coating method is to be used is dependent on a number of factors, including the following:
- What is the desired PSA thickness (usually 0.8-5.0+ mils)?
- What is the viscosity of the PSA (usually 100-100,000 cPs or more)?
- What is the PSA technology (solvent, emulsion, hot melt or 100% solids)?
- What is the solids content of the PSA package (usually 25-100%)?
- What is the required line coating speed (usually 50-700 meters per minute)?
- What is the web width of the substrate to be coated (usually 12-80")?
- What is the web material to be coated and what are its surface characteristics?
- What coating weight accuracy is required (final adhesive thickness +/-)?
- Given the adhesive type, coat weight and substrate surface, should direct or transfer coating be employed?
Once these issues are addressed, we are ready to consider which adhesive coating method is most suitable. Typical adhesive coating methods used to produce PSAs include the following.
Wire Wound Rod (Mayer Rod) Coating
This is a relatively inexpensive post-metered coating method normally used to coat solution or emulsion pressure-sensitive adhesives. Wire rod coating is usually limited to low-viscosity PSAs with good flow properties due to the possibility of "adhesive ridging," which results from the wire. Because of the ridging concern, wire wound rod coating is used primarily to adhesive-coat opaque label facestock or tape-backing materials.
Knife-Over-Roll (KOR) Coating
One of the earliest known coating methods, KOR is a simple, relatively inexpensive adhesive coating method that is most often used to coat both solution and emulsion PSAs, but is also suitable for coating hot-melt PSAs. As with wire rod coating, KOR adhesive coating may exhibit adhesive streaking and adhesive void problems, especially when coating lower viscosity pressure-sensitive adhesives at higher coating speeds. This method is, therefore, usually limited in its use to opaque facestock/backing materials and lower-performance applications.
Reverse-Roll Coating
A pre-metered adhesive coating method using several rolls to pick up pressure-sensitive adhesive, meter the adhesive amount and apply the adhesive to a facestock or backing web. The actual adhesive supply may be from a pan for lower viscosity PSAs or from a nip formed by two rolls for higher viscosity adhesives. This coating method is usually used to coat solution and emulsion PSAs, but it may also be used to coat hot-melt PSAs from a heated pan. Reverse roll coating is quite common in the United States, though it is less popular in Europe.
Gravure Coating
(includes reverse gravure, direct gravure and offset gravure)
Gravure is also a pre-metered coating method that offers very accurate adhesive coat weights at high coating speeds, but is one of the most costly adhesive coating methods available. Gravure is usually limited to low-viscosity pressure-sensitive adhesives and the application of low adhesive coating weights. It is commonly associated with emulsion PSAs, but is also useful for applying solution PSAs and release coatings. Gravure coating produces an extremely smooth coating profile and, as such, is very suitable for coating PSAs on clear film facestocks. Pattern, or zone, coating of PSAs is often accomplished using specially engraved cylinders.
Extrusion Slot Die Coating
This pre-metered adhesive coating method is an offshoot of the screw extrusion process used in the production of plastic sheets or films. It is most often associated with the coating of hot-melt PSAs because of its ability to handle high-viscosity adhesives. This coating method offers two benefits, including the ability to pattern coat the PSA and the lack of an excess adhesive feed and recirculation issue as with most other adhesive coating methods (actual adhesive feed = adhesive coat weight).
Slot Die Coating
This coating method differs from extrusion slot die principally in the use of pump pressure rather than screw extrusion to feed the PSA. It is more commonly used for coating lower-viscosity PSAs as hot-melts, high-solids emulsions or 100%-solids curable adhesives. As with the extrusion method, it is very well suited to pattern coating of a PSA.
Curtain Coating
This pre-metered method is based on the creation of a "waterfall" or "curtain" of PSA using a slot die. The curtain is positioned above, and separated from, the substrate web. In curtain coating, the PSA viscosity is extremely important in forming a consistent curtain to maintain the desired coat weight and eliminate adhesive voids. Curtain coating is associated with high coating line speeds, but because of an "overcoating" phenomenon, pattern coating of PSAs using this method is problematic. This method is quite popular in European pressure-sensitive production, but is only beginning to gain popularity in the United States.
Figure 3 shows a summary of some of the capabilities/limitations of each of these coating methods that are of interest when coating pressure-sensitive adhesives.
Conclusion
While the manufacture of PSA products is a relatively simple process of coating and laminating, it entails a number of variables. It should now be a little clearer that not all PSAs can be coated using any, or every, adhesive-coating method. PSAs are available in a variety of adhesive technologies, each having both viscosity and solids ranges associated with them. They require various thicknesses of adhesive coating weights for specific applications, and are composed of a number of different constituent materials, each of which can affect adhesive-coating requirements.
Be mindful that PSAs are expected to perform a variety of identifying, decorating and bonding jobs, and meet a host of end-use requirements that, in most cases, strongly affect the adhesive coating and laminating process.
For more information on coating and lamination equipment, contact Chemsultants Inc., 9349 Hamilton Drive, Mentor, OH 44060; phone (440) 352-0218; fax (440) 352-8572; or visit http://www.chemsultants.com.
Looking for a reprint of this article?
From high-res PDFs to custom plaques, order your copy today!