Less is More
Waterborne adhesives can become even more environmentally friendly when the proper practices are applied.

How often have we heard the term “less is more”? It is a line we use often when talking about topics such as the environment, sustainability, and the “greenness” of a particular item or concept. When it comes to adhesives-and the preservation of the environment by using less adhesive (either with a superior product technology or manufacturing technique)-the idea that “less is more” is more important than ever.
From an environmental standpoint, we have already done the bulk of the heavy lifting to make adhesive products green and environmentally friendly. We have reduced volatile organic compounds (VOCs), eliminated ozone-depleting solvents and removed nearly all volatiles. These worthy accomplishments are also environmentally responsible.
Now that we know that going green is best for our world, we need to work on fine-tuning and optimizing the effectiveness of our technologies. For example, waterborne adhesives have long been used as primary bonding products in industries such as packaging, paper converting, bookbinding, woodworking and product assembly. Traditionally, most of these end-use applications have used highly formulated polyvinyl acetate or vinyl acetate-ethylene copolymer-based products to exact a solution to the performance of the product.
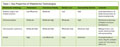
Chemistry
An adhesive’s chemistry is an example of a classic technological battle. The use of superior chemistry formulations results in the need for less adhesive product. Most will agree that acrylic begets copolymers begets homopolymers. While exceptions do exist, the use of highly performing chemistries results in a reduction in the amount of adhesive needed (see Figure 1).
Waterborne technologies offer a range of performance, cost, greenness and sustainability qualities. Table 1 compares various waterborne technologies and their key properties. Although much progress has been made, all of the technologies are, to a large extent, mature. The effort to produce greener and more sustainable technologies must continue.
Production Process
The process by which adhesives are made is a vastly untapped area that is likely constrained by existing steel in the ground. Most adhesives are produced via traditional batch processing that requires energy and hardware to make, transfer, hold, and package. The increased use of automated, less intrusive processing technologies (e.g., in-line preparation) goes a long way toward improving a product’s greenness and sustainability.
Table 2 compares the features of batch vs. in-line processing technologies. In-line mixing has yet to reach its full potential. When it does, it will provide synergistic opportunities for green and sustainable adhesive manufacturing.
Optimizing Use
Another area of particular concern is the amount of adhesive used for a given application. Reducing this amount has a direct benefit on the environmental impact of the product.
Economy and cost are often at the forefront of consideration by nearly every manufacturing sector worldwide. The search for improved methods of adhesive application-and, in turn, the total amount consumed-deserves top priority. Several factors can optimize the use of an adhesive:
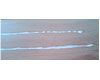
The adhesives industry, for the most part, is ahead of the green curve compared to other industries. For decades, adhesive organizations have led the charge for a cleaner environment by eliminating or reducing products that were deemed harmful. Many of us have worked in careers based solely on the development of products that meet or exceed performance criteria while demonstrating green qualities. In general, the adhesives industry has been self-policing-with the help of a few (albeit major) governmental mandates.
If the goal is to reduce the usage of adhesive by 5% for the sake of the environment, it is best to start by selecting the appropriate technology, manufacturing adhesives in the most efficient manner possible, and finally optimizing the amount of adhesives in end-use applications. Self-policing has always been important for chemists, engineers, and operators who develop, manufacture, and use adhesives; it will undoubtedly take the lead in producing advanced green and sustainable adhesives.
For additional information regarding environmentally friendly waterborne adhesives, contact Wisdom Adhesives at 1575 Executive Dr., Elgin, IL 60123; (847) 841-7002; fax (847) 841-7009; or visit www.wisdomadhesives.com.

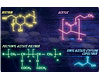
Figure 1. Chemistry Examples
From an environmental standpoint, we have already done the bulk of the heavy lifting to make adhesive products green and environmentally friendly. We have reduced volatile organic compounds (VOCs), eliminated ozone-depleting solvents and removed nearly all volatiles. These worthy accomplishments are also environmentally responsible.
Now that we know that going green is best for our world, we need to work on fine-tuning and optimizing the effectiveness of our technologies. For example, waterborne adhesives have long been used as primary bonding products in industries such as packaging, paper converting, bookbinding, woodworking and product assembly. Traditionally, most of these end-use applications have used highly formulated polyvinyl acetate or vinyl acetate-ethylene copolymer-based products to exact a solution to the performance of the product.
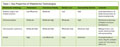
Greenness and Sustainability
Before evaluating the current state of waterborne adhesives’ greenness or sustainability, it is important to define what these concepts mean. A product’s greenness and sustainability can be defined through the following key considerations:- Environmental impact
- Recyclability
- Concentration of VOCs
- Use of renewable resources
- Comprehensive energy efficiency

An adhesive’s chemistry is an example of a classic technological battle. The use of superior chemistry formulations results in the need for less adhesive product. Most will agree that acrylic begets copolymers begets homopolymers. While exceptions do exist, the use of highly performing chemistries results in a reduction in the amount of adhesive needed (see Figure 1).
Waterborne technologies offer a range of performance, cost, greenness and sustainability qualities. Table 1 compares various waterborne technologies and their key properties. Although much progress has been made, all of the technologies are, to a large extent, mature. The effort to produce greener and more sustainable technologies must continue.
Production Process
The process by which adhesives are made is a vastly untapped area that is likely constrained by existing steel in the ground. Most adhesives are produced via traditional batch processing that requires energy and hardware to make, transfer, hold, and package. The increased use of automated, less intrusive processing technologies (e.g., in-line preparation) goes a long way toward improving a product’s greenness and sustainability.
Table 2 compares the features of batch vs. in-line processing technologies. In-line mixing has yet to reach its full potential. When it does, it will provide synergistic opportunities for green and sustainable adhesive manufacturing.
Optimizing Use
Another area of particular concern is the amount of adhesive used for a given application. Reducing this amount has a direct benefit on the environmental impact of the product.
Economy and cost are often at the forefront of consideration by nearly every manufacturing sector worldwide. The search for improved methods of adhesive application-and, in turn, the total amount consumed-deserves top priority. Several factors can optimize the use of an adhesive:
- Reducing the amount of adhesive applied, no matter the technology. For the most part, the amount of adhesive used on a given application can be likened to an ant carrying 100 times its weight. Adhesives have the capacity to far outreach the surfaces to which they are bonding. Therefore, a small 5% cutback in the amount can be easily attained.
- Ensuring that the adhesive is applied in the specific bonding area and matches both the surfaces being bonded and the application equipment.
- Using the latest and best equipment and know-how for applying the adhesive.
- Optimizing the overall gluing process.
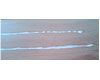
Waterborne adhesives have long been used as primary bonding products in industries such as woodworking.
Recent Advances
Waterborne adhesives date back to ancient Egyptian times. In the 20th century, with the advent of emulsion polymerization, advances were continually made. VAE technologies, the use of in-line mixing, and use optimization can play key roles for the development of future adhesive technologies based on renewable and sustainable materials.The adhesives industry, for the most part, is ahead of the green curve compared to other industries. For decades, adhesive organizations have led the charge for a cleaner environment by eliminating or reducing products that were deemed harmful. Many of us have worked in careers based solely on the development of products that meet or exceed performance criteria while demonstrating green qualities. In general, the adhesives industry has been self-policing-with the help of a few (albeit major) governmental mandates.
If the goal is to reduce the usage of adhesive by 5% for the sake of the environment, it is best to start by selecting the appropriate technology, manufacturing adhesives in the most efficient manner possible, and finally optimizing the amount of adhesives in end-use applications. Self-policing has always been important for chemists, engineers, and operators who develop, manufacture, and use adhesives; it will undoubtedly take the lead in producing advanced green and sustainable adhesives.
For additional information regarding environmentally friendly waterborne adhesives, contact Wisdom Adhesives at 1575 Executive Dr., Elgin, IL 60123; (847) 841-7002; fax (847) 841-7009; or visit www.wisdomadhesives.com.
Links
Looking for a reprint of this article?
From high-res PDFs to custom plaques, order your copy today!