Common Problems with Common Tests
Understanding manufacturer instructions and test standards can help prevent problems when testing to industry standards.
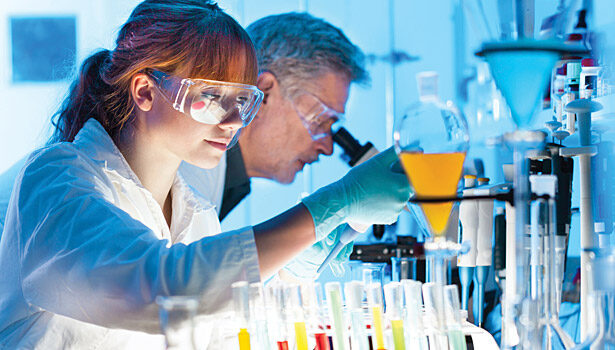
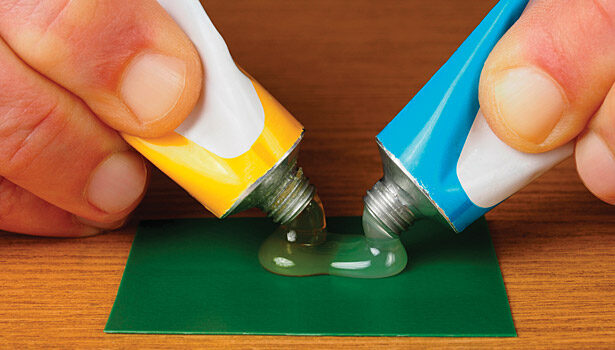


Testing to industry standards provides repeatable methods for comparison and quality assurance purposes. Test methods may have small nuances that can lead to different results if they do not receive proper attention. An understanding of some of the problems that can occur with common industry standards helps minimize and eliminate these factors.
ASTM D 3330
ASTM D 3330 is the Standard Test Method for Peel Adhesion of Pressure Sensitive Tape. This test standard contains methods A-F, which are used for quality assurance purposes. These methods are used to compare the performance of pressure-sensitive tape to a specific requirement in order to determine if the measured bond strengths are acceptable. The values obtained from this method can be used to compare values for a single roll of tape, between rolls or between lots.
Test method A, B, C, E and F can show the relative bond strength of a given tape to one or more surfaces (material and texture) compared to a standard stainless steel panel. Substitution of representative samples of materials in question for the standard steel panel would suffice to do this. Test method D can show the amount of force required to remove a liner that covers the adhesive side of a tape at a specified peel rate.1
One of the common problems with this test standard is choosing the correct test method. The user must consider what type of tape is being tested, as well as the adhesion value they are looking to determine. Since each of the procedures within this standard varies slightly, an important step— such as the number of roller passes or the method the tape is applied to the test panel—could be performed incorrectly if the wrong method is selected.
The test panel to which the tape is applied can cause problems if the proper specifications are not followed. The standard calls for a stainless steel panel with a specified surface roughness. Cleaning the plates is an important step in the test panel preparation. The test panels for these test methods need to be washed three times with one of the specified solvents prior to specimen adhesion. Ensuring that the correct surface finish and cleaning techniques are used will help minimize any effects from a dirty or rough test panel.
Once the test panels are prepared, procedures for the application of the tape to the panel must be followed. During the application of the tape to the test panel, it is important to follow the timing parameters specified in the test standard. Two of these parameters to pay attention to are the elapsed time from unwinding the tape roll to application and the time from application to test. For some tapes, the peel adhesion may increase as the dwell time is increased. The roller used to apply the tape is also important. Since this standard pertains to pressure-sensitive adhesives, the weight and surface of the roller are critical. If the surface of the roller is not perfectly cylindrical, the tape will not be uniformly adhered, leading to inaccurate data.
ASTM D 1002
ASTM D 1002 is the Standard Test Method for Apparent Shear Strength of Single Lap Joint Adhesively Bonded Metal Specimens by Tension Loading (Metal to Metal). This test method is mainly used for comparative purposes. Two metal plates are bonded together with adhesive. These samples are then pulled along the long axis of the sample until failure occurs.
The main challenge when testing to this method is sample preparation. The accuracy of test results is dependent on the preparation of the test samples. The first step to ensure proper sample preparation involves the test panels. ASTM D 1002 recommends using one of six different metals for testing. It is important to choose a panel material with a yield strength that exceeds the expected shear strength of the adhesive under test. If the wrong panel material is chosen, the results may be influenced by the tensile yielding of the panel vs. the shearing of the adhesive.
Prior to adhesive application to the test panels, the panels must be cleaned and dried per the procedure prescribed by the manufacturer. Clean test panels are imperative to achieving accurate test results. Excessive dirt or oils from handling on the bonding surface can cause incomplete bonding of the adhesive to the test panel.
Once the test panels are cleaned, the adhesive can be mixed for application. It is necessary to follow the manufacturer’s instructions for mixing. The adhesive must have complete mixing prior to application to ensure that the results from the test can be repeated and compared from batch to batch.
The adhesive must now be carefully applied to the test panels. One must use caution in order to prevent bubble formation when applying the adhesive to the test panel. Bubbles can lead to incomplete bonding due to air pockets and cause lower apparent shear strength values. It is also important to ensure the adhesive is applied with a consistent thickness in the bonding area. Applying the adhesive with a uniform thickness aids in proper sample alignment.
Once the adhesive has been applied to the test panel, the sample is ready to cure. It is important to follow the curing instructions provided by the manufacturer. Variations in cure time and conditions may cause undesirable effects on the adhesive. Short-term changes in the curing temperature or humidity can lead to chemical changes or internal stresses in the adhesive that can have an effect on the shear strength.
When loading the sample into the universal tester, it must be mounted in such a way that the sample is only loaded in shear. Self-aligning grips can be helpful in achieving this condition. Sample alignment in all axes is critical for this test procedure.
ASTM D 3759
ASTM D 3759 is the Standard Test Method for Breaking Strength and Elongation of Pressure Sensitive Tape. This test method can be used for comparison purposes and can also provide information for material specifications for product design and quality assurance applications. The results derived from this standard provide information regarding the relative strength of the as-received tape and can assist with characterizing backing materials.
Like ASTM D 3330, choosing the correct test procedure is a consideration for this test standard. The test procedures and parameters change depending on the expected elongation, pull direction and whether or not the tape is reinforced with filaments. If proper attention is not paid to the procedure, inconsistent test results will occur.
Like many other adhesive tests, sample preparation is the major area to pay attention to prior to testing. Preparing samples in a given direction (e.g., machine vs. cross) can yield vastly different results, depending on the backing material. Attention must be paid to the directionality of the tape when preparing the samples, or they could be confused.
Sample conditioning also plays a role in testing. Excessive temperature and humidity can affect adhesives and backing materials. For example, if a paper backing is exposed to high humidity, the water absorbed in the paper can cause a decrease in breaking strength. Over-handling of the test specimens can also cause localized heating of the sample.
During testing, it is important to monitor and minimize slippage. If the sample experiences unaccounted slippage, the apparent extension values will exceed the actual extension values.
Understanding the results and units is another area that can cause confusion. When reporting results, strength values are normalized to force per unit width of tape. Other tests for the backing materials may be appropriate for further evaluation.
ASTM D 1876
ASTM D 1876 is the Standard Test Method for Peel Resistance of Adhesives (T Peel Test). This test method is used to determine the relative peel resistance of adhesive bonds between flexible substrates utilizing a T-type specimen. The test specimen is loaded into a tensile tester with the bent, un-bonded ends clamped in the grips. The specimen is then pulled apart, and the peak and average peel forces are measured.
As with ASTM D 1004, the main challenge when testing to this method is sample preparation. Though no specific parameters or procedures for preparation are provided, it is important to follow all manufacturer instructions. Accordingly, it is essential that the adhesive manufacturer provides all relevant specifications for the application of the adhesive. These include surface preparation, mixing directions, application rate, and thickness and curing conditions.
If one or more of these specifications is not provided, it is important to document the parameters used so that the test can be repeated or used for comparison. Altering any of the sample preparation or test specifications can cause changes in the recorded properties. Because this method is generally used to compare the relative peel resistances of multiple adhesives, all specifications must be identical in order for the comparison to be valid.
Another important variable to consider is the backing material of the test panel. The backing material must be strong enough not to yield but also flexible enough to bend through the 90° angle of the test. If the backing material is too weak or too inflexible, undesirable failure modes may be observed. The presence of multiple failure modes adds difficulty when comparing the results of one test to another.
Testing Partners
As in many other industries, new, more cost-effective and environmentally friendly materials are constantly being developed. A good test lab will help its customers anticipate any implications associated with new adhesive formulations and backing materials, including what has been discussed here, so that testing is carried out in a reliable and repeatable manner, ultimately ensuring that the functionality is not sacrificed.
For additional information, email the author at amy.peterson@testedandproven.com or visit www.testedandproven.com.
Reference
Looking for a reprint of this article?
From high-res PDFs to custom plaques, order your copy today!