The Economic, Performance, and Sustainability Value in UV Acrylic Hot Melt PSAs
September 15, 2023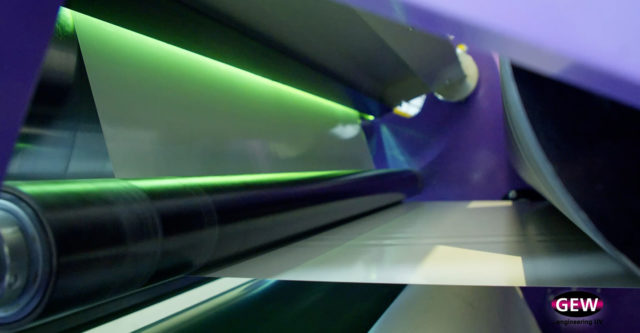
The Economic, Performance, and Sustainability Value in UV Acrylic Hot Melt PSAs
September 15, 2023Converters across the pressure sensitive adhesive (PSA) industry recognize the importance of reducing environmental impact in both manufacturing processes and end-use products. However, making this a reality without increasing costs or sacrificing application performance has been challenging. This is because sustainable materials are often more expensive than incumbent adhesive technologies and lack sufficient performance levels, making it hard to justify incorporating them. Based on acrylic technology, UV hot melt PSAs offer the financial advantages and needed performance levels while also being a sustainable solution.
UV Acrylic Hot Melt PSAs
UV acrylic hot melt PSAs are a 100% solids, PSA technology. They contain zero solvents and work well in a wide range of applications, such as label, graphic, and specialty tape needs in the automotive and building and construction markets. Unlike other existing PSA technologies that feature improved sustainability (e.g., acrylic emulsion PSAs), UV acrylic hot melts are cross-linked using UV lights immediately after the coating process in order to achieve the final performance characteristics. A well-designed UV acrylic PSA improves on the sustainability profile of emulsion acrylic PSAs while maintaining the performance of solvent-based PSAs.
Economic Benefits and Performance Levels
Compared to Solvent-Based Acrylic PSAs
Traditional solvent-based acrylic PSAs are high-performing, durable solutions that can be used in many demanding applications. However, these adhesives are, on average, around 50% solids. This means that converters need to purchase more adhesive to obtain the amount needed for a given application. Essentially, converters are purchasing a product with an inherent and significant yield-loss.
Additionally, with solvent-based acrylic PSAs, converters need to allow time for the solvent to evaporate in the ovens with each production run, which slows down line speeds. If the application requires a thick deposition weight, it may require the lamination of multiple adhesive layers in order to achieve the desired coating weight. This limitation adds to production inefficiencies and increases costs.
Further, because solvent-based acrylic PSAs are flammable, they pose safety along with storage and handling concerns. The combination of solvent vapors and the static electricity-generating environment of high-speed coating operations has resulted in numerous coating-line fires worldwide, in addition to fires that have occurred during adhesive compounding or transfer operations. When transporting these PSAs, converters are likely to be subjected to higher shipping costs than with non-hazardous adhesives.
When coating solvent-based acrylic PSAs, converters need significant capital equipment, including drying ovens, thermal oxidizers, and ventilation systems to account for solvent or VOC evaporation. These elements add operational complexity in addition to increased equipment operating, maintenance, and long-term replacement costs.
Also, because they require drying ovens, which need a significantly larger footprint than alternative coating lines, it can be challenging to fit many solvent PSA coating production lines in a limited plant space. This, in addition to the hazardous material regulations, may limit the number of lines a plant can hold, which ultimately can impact ability to meet strategic growth expectations.
Looking for a reprint of this article?
From high-res PDFs to custom plaques, order your copy today!
However, UV acrylic hot melt PSAs offer several key cost and safety advantages over solvent-based acrylic PSAs, while still possessing high-performance capabilities and being a more sustainable solution.
Increased solids: UV acrylic hot melt PSAs are 100% solids. Unlike solvent-based acrylic PSAs, there is nothing within the product that needs to evaporate. This means converters can purchase less product than solvent-based acrylic PSAs while receiving the same amount of actual adhesive.
Eliminated risk: They also do not contain any solvents, and because UV acrylic hot melt PSAs are solid at room temperature, they are a nonhazardous alternative to solvent-based acrylic PSAs. This reduces storage, transporting, and manufacturing concerns and complexities, as well as costs.
Improved production efficiencies: Compared to solvent-based acrylic PSAs, UV acrylic hot melt PSA production lines can run up to five times faster depending on adhesive deposition and number of UV lights. This is because they don’t require a drying oven, and, unlike with solvents, the UV cure is instantaneous. Additionally, converters are able to achieve a much higher coat weight in a single pass and at a faster rate, which further keeps production lines moving quickly and manufacturing costs to a minimum. This allows converters to more efficiently meet customer needs.
Reduced plant footprint: Further, because manufacturing with UV acrylic hot melt PSAs does not require any drying ovens, production lines take up less space. This enables plant space to be more efficiently used in comparison, aiding in increased revenue potential.
Compared to Rubber-Based Hot Melt PSAs
While rubber-based hot melt PSAs are 100% solids like UV acrylic hot melt PSAs and do not have the same environmental concerns (and associated costs) as solvent-based acrylic PSAs, they do still have limitations. This is because rubber-based hot melt PSAs lack needed performance capabilities for demanding (high-temperature and outdoor) applications. Depending on the specific application, they do not offer sufficient:
- Long-term oxidative stability;
- Shear levels, particularly at elevated temperatures;
- Plasticizer, UV, and chemical resistance;
- Clarity and color-stability; and
- Adhesion performance at temperature extremes.
These limitations result from the inherent chemical instability of the C=C bonds that are present in the rubber polymers as well as rheological limitations in formulated styrene block copolymer adhesives. When exposed to UV light, the rubber becomes brittle, causing rubber-based hot melt PSAs to lose adhesion. Additionally, when subjected to high heat levels, they have ooze issues upon loss of the physical crosslinks in the styrene domains. Due to their lack of chemical crosslinking and high content of oligomeric additives, rubber-based hot melt PSAs also do not have good chemical resistance, limiting where they can be utilized. Further, when in cold temperature conditions, such as lower than 10 °F, they lose their tack. As a result of these limitations, converters are unable to offer their customers expanded options and tap into key, high-value, revenue-generating applications.
PSAs based on acrylic polymers, such as UV acrylic hot melt PSAs, do not exhibit the shortcomings found in rubber PSAs for a variety of reasons, including the lack of C=C bonds and formulas comprised of a very high concentration of polymers. In addition, modern UV acrylic hot melt PSAs offer performance levels on par with most solvent-based acrylic PSAs. For example, UV acrylic hot melt PSAs possess:
- High durability and shear levels;
- Broad adhesion capabilities;
- Excellent UV, plasticizer, oxidation, and chemical resistance;
- High clarity; and
- Good bonding ability at cold temperatures.
Further, UV acrylic hot melt PSAs have a broader service temperature window than rubber-based hot melt PSAs. This means they can be applied in high- and low-temperature conditions without losing their adhesive properties. Product performance of UV acrylic hot melt PSAs can be tuned by the choice of monomer, polymer design, additives, and UV cure. Additionally, their design flexibility, when compared to traditional rubber-based hot melt PSAs, allows UV acrylic hot melt PSAs to meet a broad variety of demanding performance requirements.

A Sustainable Solution
UV acrylic hot melt PSAs are a sustainable solution in the following ways:
- 100% solids: They contain no solvents or other hazardous chemicals that first need to evaporate off before achieving desired adhesion levels. Since they don’t contain solvents, UV acrylic hot melt PSAs are not hazardous, and less product storage and transport are required. Additionally, because they do not contain solvents or other elements that need to evaporate, customers can order on average 50% less adhesive comparatively and still achieve the same bonding results.
- No ovens required: Unlike solvent-based acrylic PSAs, UV acrylic hot melt PSAs do not require ovens to cure or dry. In addition to reducing energy usage, it means they take up a smaller footprint comparatively, which helps decrease environmental impact.
- Ability to achieve high coat weights in single pass: Converters are able to achieve a much higher coat weight in a single pass and at a faster rate, gaining production time and efficiency.
Incorporating into Production Lines
If currently using solvent-based acrylic PSAs: Converters will need to invest in a hot melt PSA coating line with UV lights. Compared to solvent coating equipment, installing a hot melt coater requires a lower capital cost and enables converters to reduce overall costs due to their:
- Decreased energy usage;
- Increased production efficiencies; and
- Reduced plant footprint.
If currently using rubber-based hot melt PSAs: With minimal capital investment, a rubber-based hot melt PSA coater can be converted to run UV acrylic hot melt PSAs, allowing converters to expand their product line and performance scope. Converters only need to make slight adjustments to existing production lines to incorporate UV light(s) with a chilled roll, drum unloader, buffer tank, feed lines, and potentially adding a slot-die coating head. If converters wish to utilize both rubber and acrylic hot melt adhesives on the same coating line, they must take special care to avoid cross-contamination of the molten adhesives in the coating equipment; dedicated transfer lines and buffer tanks are strongly recommended.
When coating UV acrylic hot melt PSAs, UV light is utilized to cure the adhesive. Establishing a program that monitors and maintains the UV lamps is critical to ensuring the consistent quality of the product being produced. Additionally, adhesive performance testing should be used to determine the best operating parameters for production. Therefore, a process that monitors UV light intensity and dose is required to create consistent products and should be correlated with adhesive performance. Lastly, developing a UV lamp maintenance program is critical to maintaining the UV system at optimum conditions for production.
To contact a Bostik expert and learn more about the company's UV offering, visit bostik.com/global/en/customer-support/contact-us.
A special thanks to Bostik’s R&D and technical service experts for their help in writing this article.