New Frontiers in the Safety Assessment of Double-Sided Adhesive Tapes
An innovative approach, based on multiparametric analysis of interfacial crack behavior, opens entirely new perspectives for assessing the adhesive safety of double-sided adhesive tapes.

Credit: Vera Aksionava, iStock / Getty Images Plus
In an ever-evolving industrial landscape, advances in material technology are crucial to meet growing demands. Double-sided adhesive tapes are increasingly coming into focus as indispensable components across various industries. Previously, mechanical joining techniques such as screws, rivets, and welding were dominant. However, with the emergence of lighter materials, more complex designs, and the pursuit of more efficient manufacturing processes, adhesive tapes are gaining importance. Industrial double-sided adhesive tapes, in particular, have proven to be highly versatile solutions for not only permanently bonding materials but also achieving aesthetically pleasing finishes. Companies in sectors such as automotive, electronics, aerospace, and others are increasingly turning to these adhesive solutions to reduce weight, shorten assembly times, and enhance the overall performance of their products.
The reasons for this are manifold: Adhesive tapes enable even distribution of stresses across the entire joint, leading to improved stability. They also offer greater design flexibility, facilitating the bonding of materials with different properties. Moreover, they contribute to noise reduction and vibration damping, which is particularly crucial in the automotive sector. Given these developments, the precise evaluation of adhesive tape performance is becoming increasingly important, underscoring the need for new innovative testing methods in the adhesive industry. These have already been introduced and extensively discussed in previous publications1-13.
Conventional Testing Approaches with Inherent Constraints
In the realm of assessing the suitability of double-sided adhesive tapes, manufacturers consistently prioritize peel resistance tests14,15. It is argued that, in conjunction with adhesive tensile strength16 and shear strength17-20 tests, this method adequately captures minimum adhesive properties. The emphasis is on speed and cost reduction. However, given the prolonged presence of these test methods in the market and the emergence of new innovative approaches, evaluating the efficacy and dependability of established methods becomes imperative. This article introduces an innovative testing and evaluation methodology, initially applied to double-sided adhesive tapes by two major tape manufacturers. Table 1 provides an overview of common test methods, using tapes from Company A as a reference point.
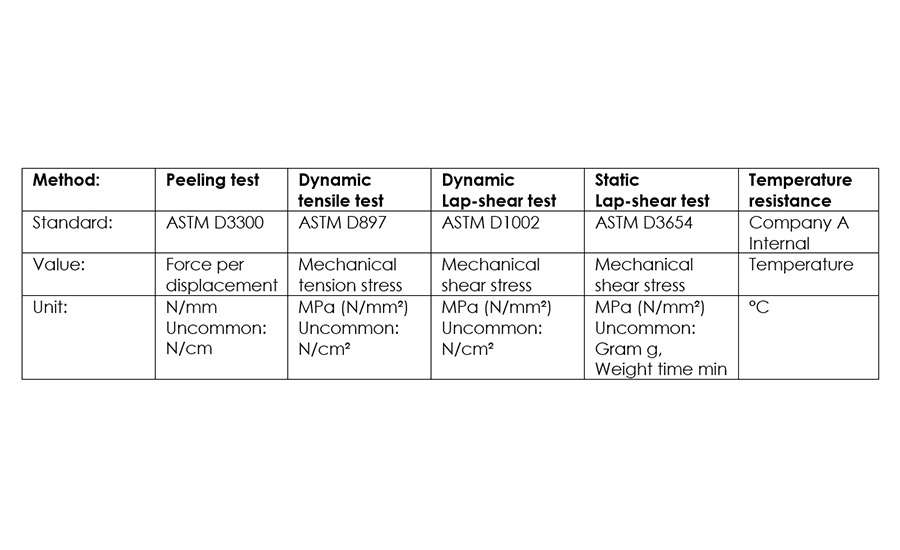
Table 1 outlines the attributes of the methods along with their distinctions:
- Peel tests14,15 evaluate adhesion properties by peeling the adhesive tape from one side at a steady pace. However, limitations include focusing solely on peak values and overlooking other concurrent load types in practical scenarios. Moreover, it fails to describe the intricate failure mechanisms in the boundary layer or characterize the extent of the plastic process zone.
- Tensile adhesion tests16 resemble peel tests but involve bonding the adhesive tape on the facing side and pulling it uniaxially from both sides at a constant rate. The outcome, termed adhesive tensile strength, signifies the mechanical stress in [MPa] leading to bond separation. However, it shares the drawbacks of the peel test.
- Tensile shear tests17-20 determine the maximum shear stress of the adhesive bond by applying a shear force at a constant rate until bond failure. Nonetheless, it shares the limitations of the peel test.
Although these methods remain prevalent, they suffer from significant limitations as they overlook the intricate interactions at the interface crucial for assessing bond performance and reliability. To address these shortcomings, this article introduces a validated test method from FRACTURE ANALYTICS. Known as the MCT method21, it enables testing of all typical load types (crack opening, longitudinal shear, transverse shear) either individually or in combination. However, the most notable feature is its capability to capture stable test curves, even with brittle materials. This sets it apart from other conventional test methods available. Additionally, it offers broader evaluation possibilities not covered by traditional methods14-20. The MCT method has already been incorporated into the standard testing protocol at FRACTURE ANALYTICS.
In-depth Evaluations Employing Multiparametric Fracture Analysis
Manufacturers' reliance on traditional standard test methods14-20 often stems from historical factors. Cost minimization and the principle of minimum effort typically govern testing policies in this context. Scientific methods with higher requirements are often not prioritized in this cost-driven industry, as sales take precedence and there's often a lack of appreciation for the added value of new innovative test methods. FRACTURE ANALYTICS conducted a correlation analysis to illustrate some of the problems resulting from previous measurement methods. The analysis compared adhesive tape thickness with peel strength and adhesive tensile strength. The results were surprising, indicating that relying solely on peel tests is not advisable. Table 2 presents the results of the correlation analysis from a recent study on various adhesive tapes.

When examining peel resistance and adhesive tape thickness, a positive correlation coefficient of 0.72 is observed. This suggests that there is a relationship between these factors, implying that thicker adhesive tapes lead to higher peel resistances. However, this isn't necessarily the case. Peel resistance remains constant at around 3.4 [N/mm], irrespective of tape thickness, indicating an unclear correlation. Other factors come into play, such as adhesive tensile strength, directly measured by FRACTURE ANALYTICS, averaging at 0.20 [MPa]. Contrary to peel strength, when compared to tape thickness, adhesive tensile strength exhibits a negative correlation coefficient of -0.33, indicating a different trend.
Comparatively, two new parameters from multiparametric fracture analysis, interface debonding strength σc and interface delamination resistance GF, present contrasting insights. These values, previously unused in adhesive tape evaluations due to manufacturers' limitations, are showcased in Figures 1a (top) and 1b (bottom), summarizing the correlations of all test parameters relative to adhesive tape thickness and peel resistance. (Peel resistance data from the manufacturer. Peel-off strength data from own measurements from FRACTURE ANALYTICS.)

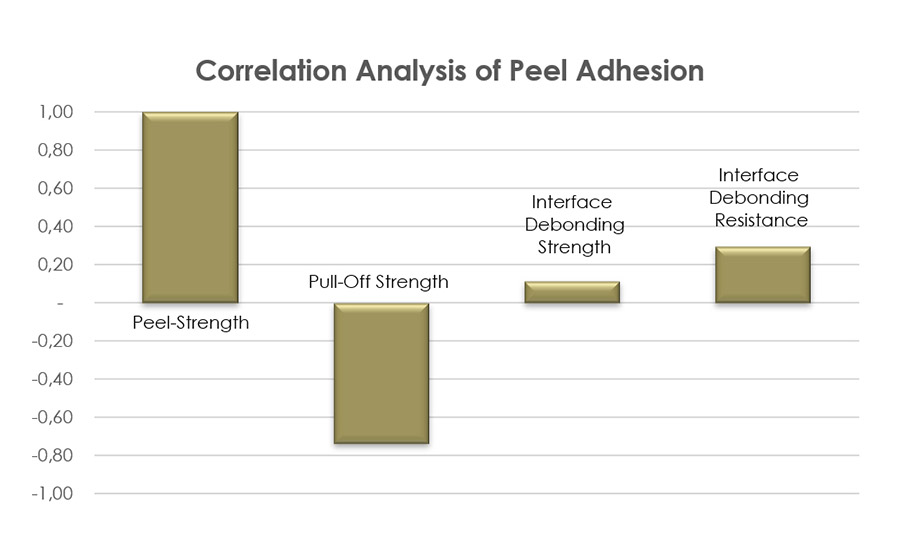
Novel Empirical Metrics for Assessing the Adhesive Security of Adhesive Tapes
FRACTURE ANALYTICS employs a total of eight specially developed empirical key figures based on multiparametric fracture analysis for the assessment of adhesive safety, determined using the MCT method21. This can be likened to a pilot conducting a clear-weather, calm-wind, daylight flight (peel resistance test) versus a night flight in rain and crosswinds with extensive flight assistance systems (MCT test method). While a detailed explanation of all key figures exceeds the scope of this article, two of the eight key figures will be presented here:
1. Interface Debonding Strength σc
The interface debonding strength σc enables the evaluation of the cohesive peel stress in the interface during crack propagation and peeling under different types of loading. Unlike the pure adhesive tensile strength, this parameter measures fracture-analytical detachment processes in the two boundary layers between the adhesive tape and the substrate (interface fracture mechanics). As the failure processes there are much more complex and better reflect real processes, this method is preferable to simple peel tests.
2. Interface Debonding Resistance GF
The interface debonding resistance GF is an energetic evaluation parameter from non-linear plastic fracture mechanics. It measures the crack resistance of a material under load for the crack formation, crack initiation and crack propagation phases. Mathematically, it is the area under a stable test curve from the load-displacement diagram in relation to the ligament area of the fracture surface of a test specimen. In the case of the current study, load mode I (crack opening) was selected, which corresponds to the international test standard. In comparison to the pure peel resistance — which only provides a maximum value — the delamination resistance determines an empirical material law in the form of an individual test curve. Furthermore, this key figure is an independent material property and therefore provides a higher quality of information. It is therefore clearly preferable to peel resistance tests21.
Novel Insights into Evaluating the Adhesive Safety of Adhesive Tapes
Figure 2 depicts the trajectory of measurement outcomes for various adhesive tapes from Company A, including Tape A2, Tape A1, and Tape A3, alongside those from company B with tapes B1, B2, B3, and B4.
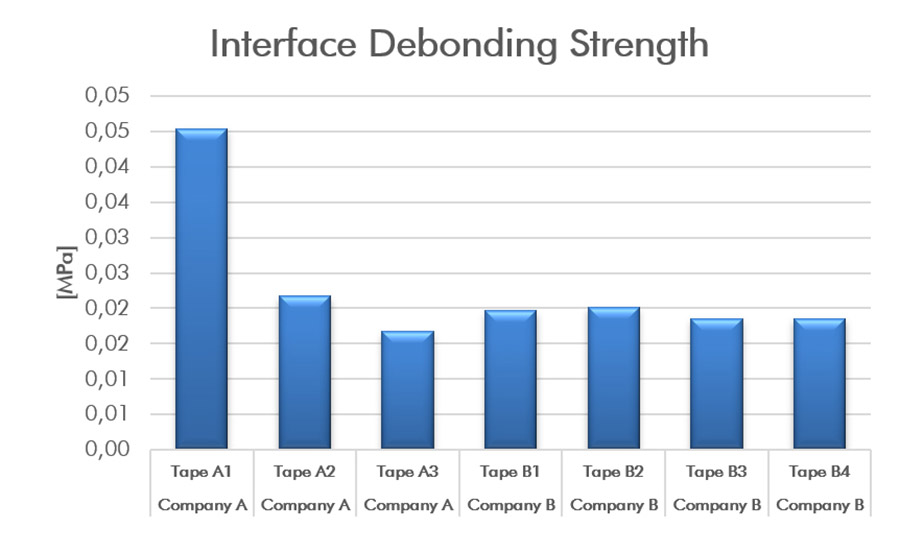

The findings can be summarized as follows:
1) In Figure 2a (top), the interface debonding strength σc is depicted. Notably, Tape A1 exhibits double the values compared to the rest of the group, which range around 0.02 MPa. These values are approximately 10 times lower than the adhesive tensile strengths. This discrepancy arises from the fact that samples for the fracture analysis test are pre-cracked before testing begins, facilitating controlled crack propagation until complete fracture.
2) Figure 2a (bottom) illustrates the trajectory of delamination resistance GF. Tape A1 presents the lowest performance in this aspect. With a value of approximately 0.4 J/mm², it demonstrates the weakest resistance to delamination among all tested tapes. Consequently, in scenarios involving tears in the boundary layer due to defects and external stresses, this tape exhibits the lowest tear resistance and the highest likelihood of debonding. In such instances, candidate Tape B2 emerges as a preferable option, boasting 2.5 times higher debonding resistance compared to Tape A1.
Summary and Outlook
The findings from the current assessment of adhesive safety in double-sided tapes from two different brands reveal that relying solely on peel resistance and tensile strength does not provide a comprehensive performance overview. The varying correlations between the test parameters commonly used by manufacturers14-20 and those of FRACTURE ANALYTICS21 highlight the need for further detailed investigations. It became evident that peel resistance alone does not suffice for an adequate evaluation or reliable selection of double-sided adhesive tapes. Consequently, the MCT method was employed in Mode I across seven different products from two tape manufacturers. This investigation revealed that the assessment of the adhesive tape boundary layer produces different outcomes depending on the test parameter utilized. Thus, there is a pressing need to develop a carefully considered evaluation framework for double-sided adhesive tapes that addresses these discrepancies. More insights will be provided in the forthcoming study by FRACTURE ANALYTICS, scheduled for fall 2024.
Learn more about FRACTURE ANALYTICS at www.fractureanalytics.com.
References:
1. Brandtner-Hafner, M. H. "Unkontrolliertes Versagen verhindern: Neues Analysekonzept für die Klebstoffselektion." In: Dicht! (1) 2018, S. 34–35, ISGATEC, Mannheim.
2. Brandtner-Hafner, M. H. "Mit SF und SP die Sicherheit von Strukturverklebungen verbessern." In: Dicht! (3) 2020, S. 20–21, ISGATEC, Mannheim.
3. Brandtner-Hafner, M. H., "Ressourcen bei der Klebstoffselektion sparen." In: JAHRBUCH Dichten. Kleben. Polymer, 2019, S. 66–76, ISGATEC, Mannheim.
4. Brandtner-Hafner, M. H., "Die optimale Kleb-Performance ermitteln." In: JAHRBUCH Dichten. Kleben. Polymer, 2020, S. 56–63, ISGATEC, Mannheim.
5. Brandtner-Hafner, M. H., "Die Sicherheit von Strukturklebungen bewerten." In: JAHRBUCH Dichten. Kleben. Polymer, 2021, S. 278–287, ISGATEC, Mannheim.
6. Brandtner-Hafner, M. H., "Auswirkung von Fügeteilvariationen auf die Klebsicherheit." In: JAHRBUCH Dichten. Kleben. Polymer, 2022, S. 231-239, ISGATEC, Mannheim.
7. Brandtner-Hafner, M. H., "Innovatives Bewertungskonzept für die qualitative Klebstoffselektion." In: Adhäsion: Kleben & Dichten 62 (5), 2018, S. 28–33, DOI: 10.1007/s35145-018-0034-1.
8. Brandtner-Hafner, M. H., "Ganzheitliche Bewertung von Industrieklebstoffen für den optimalen Selektionsprozess." In: Adhäsion: Kleben & Dichten 63 (5), 2019, S. 22–25, DOI: 10.1007/s35145-019-0030-0.
9. Brandtner-Hafner, M. H., "Technisch-ökonomische Sicherheitsbewertung von Strukturverklebungen." In: Adhäsion: Kleben & Dichten 64 (5-6), 2020, S. 24–29, DOI: 10.1007/s35145-020-0119-5.
10. Brandtner-Hafner, M. H., "Einfluss von Substratvariationen auf die Klebsicherheit." In: Adhäsion: Kleben & Dichten 65 (4), 2021, S.26–30, DOI: 10.1007/s35145-021-0487-5.
11. Brandtner-Hafner, M. H., "Klebsicherheitsbewertung mittels ganzheitlicher Bruchanalytik." In: Adhäsion: Kleben & Dichten 66 (3), 2022, S.30–35, DOI: 10.1007/s35145-022-0564-4.
12. Brandtner-Hafner, M. H., "Effizienzbewertung von geklebten Betonverbunden." In: Adhäsion: Kleben & Dichten 66 (12), 2022, S.34–37, DOI: 10.1007/s35145-022-1145-2.
13. Brandtner-Hafner, M. H., "Spaltbrückeneffizienz elastischer Verklebungen." In: Adhäsion: Kleben & Dichten 67 (7-8), 2023, S. 40–44, DOI: 10.1007/s35145-023-1209-y.
14. ASTM D1876, "Test Method for Peel Resistance of Adhesives." 2015, DOI: 10.1520/D1876-08R15E01.
15. ISO 8510, "Klebstoffe - Schälprüfung für flexibel/starr geklebte Proben." Beuth, Berlin, 2010, DOI: 10.31030/1720845.
16. ASTM D7234, Standard test method for pull-off adhesion strength of coatings on concrete using portable pull-off adhesion testers, 2021, DOI: 10.1520/D7234-21.
17. DIN EN 1465, "Klebstoffe - Bestimmung der Zugscherfestigkeit von Überlappungsklebungen." Beuth, Berlin, 2009, DOI: 10.31030/1507601.
18. ISO 4587, "Klebstoffe - Bestimmung der Zugscherfestigkeit hochfester Überlappungsklebungen." Beuth, Berlin, 2003, DOI: 10.3403/02844256.
19. ASTM D3163, "Standard Test Method for Determining Strength of Adhesively Bonded Rigid Plastic Lap-Shear Joints in Shear by Tension Loading." 2014, DOI: 10.1520/D3163-01R14.
20. ASTM D1002, "Test Method for Apparent Shear Strength of Single-Lap-Joint Adhesively Bonded Metal Specimens by Tension Loading (Metal-to-Metal), Test method for apparent shear strength of single-lap-joint adhesively bonded metal specimens by tension loading (metal-to-metal)." 2010, DOI: 10.1520/D1002-10.
21. Brandtner-Hafner M. H., "Interface fracture behavior of industrial adhesives: A novel evaluation approach for adhesive selection." in Proceedings of the IN-ADHESIVES Symposium on Innovations in Adhesives and their Applications, Munich, February 14-15, pp. 221-229, 2017.
Looking for a reprint of this article?
From high-res PDFs to custom plaques, order your copy today!