In the Wake of the Supply Chain Crisis: How Are We Doing?
Companies that took advantage of the opportunity to learn, afforded by the supply chain crisis, have profited greatly and are more prepared than ever to tackle similar difficult times in the future.

credit: PorFang / iStock / Getty Images Plus
The Great Supply Chain Crisis of 2021-2022 acted as a very loud and exceptionally clear wakeup call for all participants within the specialty chemicals value chain, whether in adhesives and sealants; paints and coatings; household, industrial & institutional cleaners (HI&I); lubricants and hydraulic fluids; personal care products; or many others. Its message was loud and clear in all market sectors: “If you don’t wish to have a future repeat of this crisis, in which. . .
- New headaches and new challenges became daily events, albeit rarely challenges of the positive kind
- Employees throughout the company felt a level of stress unthinkable in the past
- Valuable but burned-out employees left you dangling in the wind because they either retired early or sought employment in non-chemical industries
- You were forced to shed other highly knowledgeable employees so that you could keep your business afloat
- Your product liability increased, sometimes dramatically, because of the types and amounts of raw material substitutions that you were required to make
. . . then you only have one way forward: everything must change.” Whether. . .
- Supply chain procedures and policies or product formulation practices
- Production procedures or logistics, both incoming and outgoing
- Policies governing both accounts payable and accounts receivable
- Stocking levels, both raw material and finished goods
. . .Everything that the specialty chemicals industry, and especially those companies within this market space that are engaged in formulation, needs to be re-examined in the light of the Supply Chain Crisis, and — with few exceptions — everything must be changed in ways previously not envisioned, but now necessary for the smoothest possible, and least vulnerable, operation heading into the future.
Multiple industries were given the opportunity by the crisis to learn from the past so that they could create safer, more secure, and more robust protocols and processes in the future to guard against the failures that the entire globe had just experienced. Those that took advantage of this enforced opportunity to learn have profited greatly and are more prepared than ever to tackle similar difficult times in the future. Those that did not take the opportunity to learn the lessons from the Supply Chain Crisis, however, are just now beginning to feel the delayed impact of their lack of change to accommodate the new reality. There are those that are struggling to keep their heads above water. Others have either drowned or are in the process of drowning. It is sad, but predictable. The one weapon that every adhesives and sealants raw material supplier and product formulator has at its disposal is the ability to create a strategy that takes into consideration the lessons learned during the Supply Chain Crisis, and to apply this learning to the careful creation of a winning strategy for the future. Such a strategy will not only keep businesses from repeating the mistakes of the past, but also give them new tools to deal with similar situations in the future. Such strategies not only prepare organizations to avoid serious damage, but also arm them to take advantage of opportunities that inevitably arise during any period of time in which chaos reigns, whether regionally or globally.
A proper strategy must focus on the actions necessary to secure access to supplies of raw materials under all conditions. By developing a “worst case scenario,” proactive adhesives and sealants producers and their raw material suppliers will be able to keep the wolf from the door for as long as possible. This may sound simplistic, but such an approach has many elements that must be anticipated and put into place in advance of the occurrence of a critically disruptive event. As we enter an uncertain future, supply chain managers cannot afford to chase every raw material penny down to the bottom of the barrel — we all saw, in 2021-2022, what happened to formulators with supply chain managers who had treated their raw material suppliers with a lack of respect and collegiality, whereas formulators who valued raw material suppliers and who treated them as partners faced far fewer difficulties obtaining desperately needed materials than did the “C List” customers. (Yes, there is very definitely a rating of customers kept by raw material suppliers that typically ranks them from “A” to “C,” which is why it wasn’t that uncommon during the Supply Chain Crisis for a relatively small customer to be given delivery precedence over a very large, but less considerate, customer.)
Concurrently, raw material suppliers need to be incentivized to develop new products that will generate sufficient sales and margins to justify their investment in R&D. We saw, during 2022-2023, both the positive and the negative results that arose as a result of raw material suppliers that were properly treated and incentivized vs. those that were not. Consequently, far fewer new raw materials were introduced into commerce during that period of time. Midway through 2024, however, it appears that the tide has turned, and raw material producers are once again able to begin supporting the development of strategically important materials for the formulated specialty chemicals industry that are intended to address such global strategic issues as unpredictable PFAS regulatory action and the increasing interest in giving “sustainability” true support, rather than just lip service. NOTE: Certain aspects of “sustainability” fit within the concept of ESG. While ESG is an important concept, it is a concept far too broad to discuss within the context of this article, which is devoted to the concepts of both “sustainability” and “new raw materials.”
The majority of raw material suppliers, distributors, and adhesive/sealants producers do not foresee significant supply chain disruptions during 2024, but everyone adds one or more of the following conditional phrases, “We don’t see any significant supply issues, assuming that:
- We do not have an unexpected and disruptive economic event in, or directly affecting, the United States”
- Interest rates do not begin to rise again.”
- The War in Ukraine, the war between Israel and Hamas, the Houthi rebel activity in the Red Sea, or the Chinese activity in the Pacific cause anything to disrupt the global supply chains to a greater degree than has already been the case.”
- PFAS discussions do not result in sudden, unanticipated, and chaotic regulatory activity.”
There are quite a few qualifiers in play here, but this is probably as realistic as it is possible to be at this point in time. Many of these companies are giving precedence in their thinking to tactical, rather than strategic matters, and that is a natural thing to do, but it isn’t going to do much more than keep them afloat for the near-to-mid-term. Only by looking at the future through the lens of strategy can companies create plans to position themselves to take maximum advantage of opportunities and minimize threats from outside forces.
What timeless lessons have we learned and assimilated from the supply chain issues and high inflation of the past few years that will help the adhesive and sealants industry have as bright a future as possible?
- No manufacturing business can afford to keep all of its eggs in one basket.
- Single sourcing from raw material producers is dangerous.
- Single sourcing from individual countries is even more so.
- JIT (just in time delivery) is dead — or if not yet dead, at least in a state of dying. Unless you are a very large customer that is the final link in your supply chain, JIT is your enemy, not your friend.
- Every raw material used to make adhesives and sealants in the United States should have at least one reliable vendor in the United States that either makes the material in the United States or has significant stocking capability in the United States.
- Having a single source of any raw material is a bad idea, even if it is sometimes necessary due to the absence of a second source.
- Certain high-profile manufacturing operations should be repatriated to the United States, as should the ancillary suppliers to those industries.
- It is also good to have a low-profile but ongoing R&D effort to investigate potential raw material substitutions and have specifications, instructions for use, and product names readily available in the case of shortages.
- Even during the darkest hours when all hands are on deck trying to put out fires, absolutely nothing should prevent at least a minimal level of true R&D from taking place.
- Adhesives and sealants are part of a technology-based, global industry; those with a strategy focused on the continual development of new and improved products will be the winners.
The Current World from the Perspective of Specialty Chemical Suppliers
China was seriously harmed by the COVID pandemic and has recovered uncharacteristically slowly from the economic damage that it incurred as a result. It hasn’t been purchasing nearly the amounts of raw materials for in-country use that would have been the case if things hadn’t been so hampered by closures. China is finally beginning to draw on raw materials again for internal use, and we need to be ready for that. This is not yet a supply issue — China is facing substantial economic challenges, including deflation, an unstable housing market, significant declines in domestic stock markets, and a level of foreign investment in 2023 that was the lowest in the past three decades.1 Nonetheless, there is likely to be a recovery in the future, and this is exactly the sort of situation that a properly prepared strategy anticipates and prepares options for dealing with such eventualities if/when they occur.
In addition to raw material availability at the producer, another major cause of shortages and steep price increases between January 2020 and January 2023 was the cost of transoceanic shipping containers, which rose dramatically from approximately $1,500-$2,500 for non-hazardous loads in late 2019 to as much as $20-$21K (even as high as $30K in specific incidences) by mid-2021, before dropping back to the deceptive “new low” of roughly $1,300 in January of this year. Unfortunately, this is when the Iranian-backed Houthis initiated what is now called the Red Sea Shipping Crisis. Thirty percent of global container trade travels through the Suez Canal, and shipping costs have risen as much as five-fold on routes from Asia to Europe. J.P. Morgan estimates that the disruptions could add 0.7 percentage points to global core goods inflation, and 0.3 percentage points to overall core inflation, during H1 2024.2
From January to April 2024, the cost to ship a 40-foot container from China to the United States went from $1,300 to as high as $4,400 in March, before declining to $3,300 in April. What happens to the cost of container shipping in the months ahead is anybody’s guess, but it is difficult to see it settling back to $1,300 anytime soon, even if the Red Sea shipping attacks stop tomorrow (Figure 1).
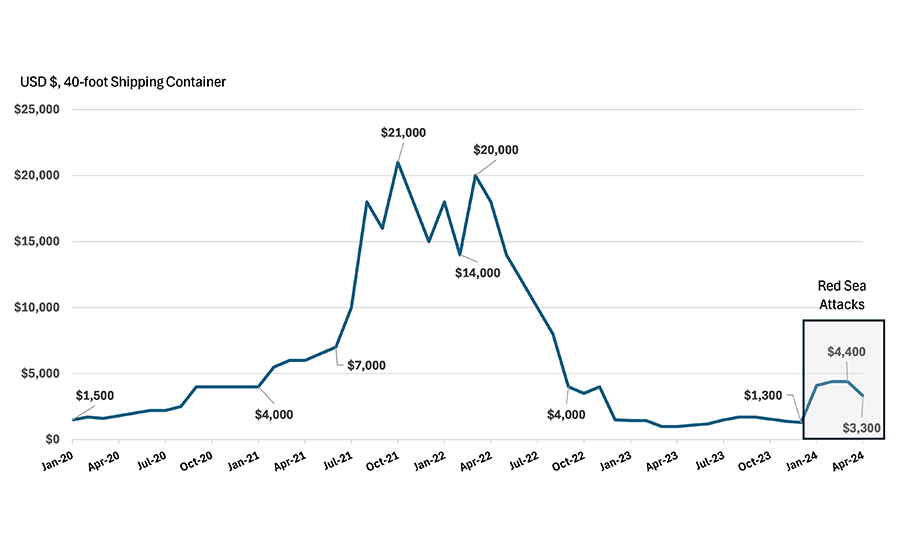
Although U.S. long-distance trucking rates declined between January 2022 and January 2023, the decline hasn’t been to nearly the level that prevailed in January 2019 (Figure 2) and U.S. rail transportation of freight steadily rose between January 2020 and January 2024 (Figure 3).
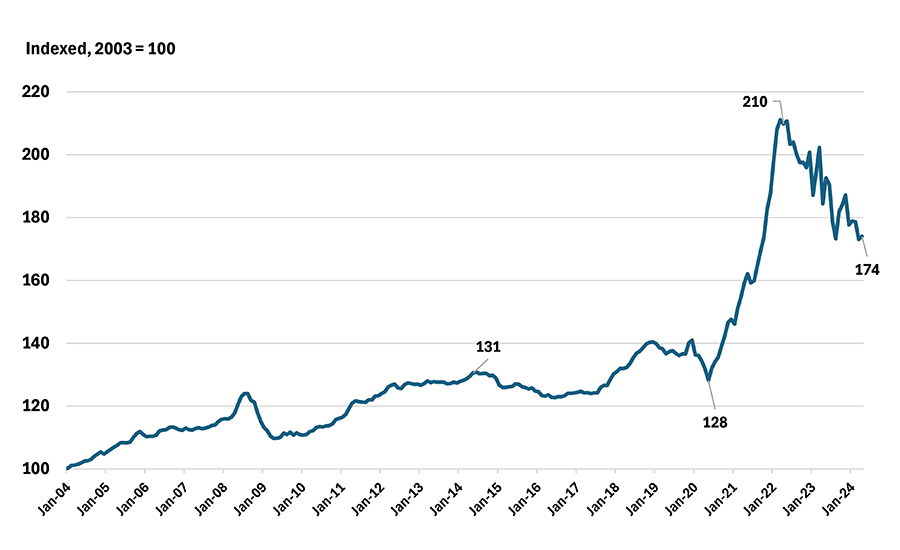

The “Resetting” of the U.S. Economy
There is little doubt that not just the U.S. economy but the entire global economy is being “reset” to one degree or another — and in one aspect or another. It is reasonable to envision a continuum from 2021 through 2025 in high-level terms that nonetheless should have some degree of meaning for everyone in the U.S. adhesives and sealants industry with regard to overall market dynamics during this period of time:
- 2021 — "The Supply Chain Train Wreck” was initiated by the February 2021 Great Freeze in the Permian Basin and exacerbated by the subsequent supercell storms, hurricane-force winds, severe flooding, baseball-sized hail, and large numbers of tornadoes in the region throughout the remainder of the year.3
- 2022 — We experienced some degree of recovery in Q3-Q4 with regard to lead times and availability, but a significant period of inflation set in as demand increased, unemployment hit historic lows, and cost of labor soared for industry as a whole. The typical R/M cost increase for a basket of formulated specialty chemicals raw materials between Q1 2020 and Q4 2022 was roughly 40-50% (Figure 4).
- 2023 — Markets tried to right themselves, but they were pushing uphill; supplies and prices began to normalize gradually throughout the year, but the cost for the same basket of raw materials from Q4 2022 was only down by approximately 30% by Q4 2023.
- 2024 — Lacking a major intervening global/economic event, most raw materials should be readily available, but pricing is unlikely to sustain any additional declines.
- As a result of the move from work offices to home offices, there is an oversupply of offices and office buildings that is unlikely to be brought into balance before 2029-2030.
- Sales of both new and existing homes is improving slightly during H1 2024, but there is simply no question that the country is in a deep hole with regard to housing — per the National Association of Home Builders (NAHB),4 there is a nationwide shortage of roughly 1.5 million housing units. This clearly reflects the mixed emotions of both the public and the construction industry on a number of fronts, including the overall health of the economy; the risk of further inflation; the significant increase in the price of housing; the stability of the financial markets; and the labor supply.
- 2025 — The “Reset Point” will be reached by Q4, with regard to the availability of raw materials and stabilized pricing. Mortgage rates will decline, leading to improved activity in the sale of existing — and construction of new — homes. Supply and demand in residential units is unlikely to be in balance until 2029, however.
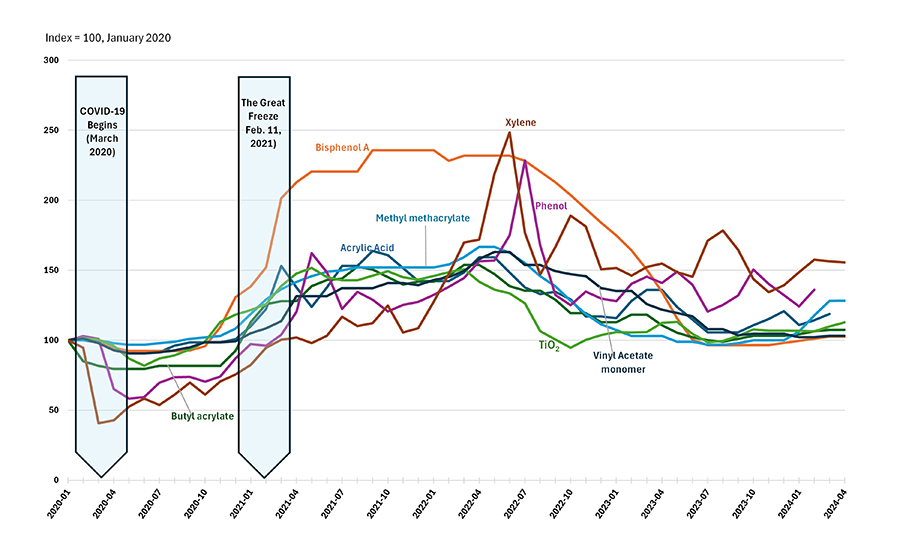
What is Going to Become of the R&D Efforts in the Specialty Chemicals Industries?
There wasn’t an abundance of new products offered to the specialty formulating manufacturers or to their raw material suppliers between 2019 and 2023 due to the need for “all hands on deck” to deal with both raw material substitutions and to assist with finding and approving new sources of raw materials. This is improving, however, and there is no need to be concerned that there aren’t any new raw materials around. The fact that sustainability is the subject of growing — and very serious — interest around the globe, the increasing move of the specialty chemical industries to embrace ESG (Environmental, Social and Governance) as a part of strategic planning, the increasing interest of both businesses and the public in the environment, and the initial regulatory fiat emerging in the PFAS arena will guarantee a steady flow of new raw materials for all businesses that either make or use specialty chemicals. A random look around in H1 2024 brought to my attention many new raw material introductions that met the criteria that I have used in past years for inclusion in my articles. They must be materials:
- That have been introduced into general commerce with the past 18-24 months
- That their producers affirm are not just “tweaks” on existing products
- That definitely hold the potential to create properties in certain specialty chemical systems that do not currently exist, or significantly improve properties in formulated materials that do
The specialty formulated chemicals sector, including adhesives, sealants, paints, coatings, personal care, lubricants, and several others, is exposed to many such materials every year, and — without endorsing or recommending any of them, either on behalf of myself, the ChemQuest Group, or ASI — I am including some of them in Table 1 because these products, while chosen both randomly and arbitrarily, are likely to make sense for paint, coatings, adhesive, and sealant formulators (and perhaps other specialty chemical formulators, as well) to evaluate, especially if the descriptions of the new materials (provided by their manufacturers) in the tables appear to address any properties that would be helpful in creating new commercial formulated products.5
Table 1. Examples of New Raw Material Introductions. (PDF)
What Lies Ahead?
The adhesives and sealants industry is still reeling from three very stressful years in which more than just raw material shortages, late deliveries, and skyrocketing raw material prices were problems. The loss of key personnel, along with their collective experience, who either burned out and left the industry or who simply couldn’t stand the stress and retired much earlier than they had planned, will be felt by the adhesives and sealants industry for years to come, especially in the technology and marketing areas. Adding insult to injury, certain employers reduced staff in these critical areas to save money, which still happens despite the decades of experience that counsel against such actions. The outcome is the permanent loss of knowledge, experience, and collective wisdom. Such attributes were developed slowly and deliberately over significant periods of time and cannot be recreated or duplicated in the short term. Once knowledge and experience are gone, they are gone, and this should be the most sobering and thought-provoking takeaway from this article.
As a result, raw material suppliers and specialty chemical producers, such as adhesive, sealants, paints, and coatings formulators are looking to universities, independent third-party technology institutions like ChemQuest, third-party testing laboratories, and independent subject matter experts to supply them with the experience that was once “in house” but has now disappeared and cannot be backfilled with other personnel who lack sufficient experience and expertise. At ChemQuest, we are actively helping manufacturers in the specialty chemicals value chain deal with the effects of this loss of experience, whether in adhesives and sealants; paints and coatings; lubricants; personal care; HI&I; and a variety of other areas. Although both a period of global crisis and long-term poor management by many producers caused the situations that precipitated this loss of valuable expertise, a timely opportunity has arisen to explore the experience and creativity of highly experienced, independent experts who bring a wealth of technical and marketing knowledge and operational know-how to bear upon the challenges and opportunities of the formulated specialty products producers who seek their help to solve a universe of diverse issues in an efficient, cost-effective manner.
This is very likely to be the wave of the future, in which cross-functional, in-house resources, working with independent experts, will be the most efficient and cost-effective approach to meeting increasingly demanding time-to-market requirements with appropriate new products.
To learn more, reach out to the author at gpilcher@chemquest.com or visit https://chemquest.com.
References
1. “Overview: The World Bank in China,” updated April 2024, https://www.worldbank.org/en/country/china/overview#:~:text=Domestic%20demand%20in%20China%20has,to%20undergo%20a%20structural%20slowdown.
2. “What are the impacts of the Red Sea shipping crisis?” J.P. Morgan, February 2024, https://www.jpmorgan.com/insights/global-research/supply-chain/red-sea-ship-ping#:~:text=Overall%2C%20J.P.%20Morgan%20Research%20estimates,transport%20times%20and%20freight%20costs.
3. Pilcher, G.R., “The Great Supply Chain Fiasco of 2021-2022: The Immediate Danger is Past, but What Lies Ahead?” CoatingsTech, 2023, 20 (3), pp. 30-40.
4. Thompson, E., “Single-Family Starts will Rise in 2024 but Supply-Side Challenges Persist,” National Association of Home Builders, February 2024, https://www.nahb.org/news-and-economics/press-releases/2024/02/single-family-starts-will-rise-in-2024.
5. Pilcher, G.R., “The Great Supply Chain Fiasco of 2021-2022: The Immediate Danger is Past, but What Lies Ahead?” loc. cit.
Looking for a reprint of this article?
From high-res PDFs to custom plaques, order your copy today!