Optimizing Adhesives and Coatings Production with Advanced Mixing Technologies
Strategic selection of mixing equipment is essential to efficiently produce the next generation of high-value adhesives and capitalize on industry innovations.

courtesy of ROSS
The adhesives, sealants, and coatings markets continue on the trajectory towards more sustainable, high-performance formulations using advanced raw materials and efficient production methods. Biomaterials, nanocomposites, and novel functional additives not only improve product performance but also contribute to reducing environmental impact. Amid this wave of cutting-edge formulation work, one fundamental processing truth remains: optimal mixing, dispersion, and emulsification are critical for achieving the desired color, gloss, conductivity, stability, adhesion, cure rate, weather resistance, and other properties.
The best and most innovative formulas in the world won't live up to their potential if they aren't mixed properly and especially if they can’t be replicated batch after batch. This makes strategic selection of mixing equipment a pivotal decision for manufacturers looking to efficiently produce the next generation of high-value adhesives and capitalize on industry innovations. Investing in the right mixing technology not only ensures product quality but also helps manufacturers stay competitive in a rapidly evolving market.
Innovations Driving Mixing Needs
The industry has witnessed a surge of developments reshaping formulation and production requirements, including:
Bio-based/Renewable Materials: Plant-derived oils and waxes, rosins and rosin esters, cellulose nanocrystals, starches, and agricultural byproducts like chitosan are increasingly used as more sustainable alternatives to petroleum-based ingredients. Effective dispersion and stable emulsions/suspensions are critical when working with these natural raw materials.
Waterborne and Low-VOC Formulations: In response to environmental regulations, high-performance waterborne coatings and low/zero-VOC formulations have become paramount. However, proper wetting and dispersion of pigments, silicas, clays, sulfates, and other additives in these formulations can be challenging.
Reactive and Radiation-Curable Materials: UV-curable, EB-curable, and hybrid radiation-curable systems are growing rapidly due to productivity and performance advantages, but consistent dispersion of photoinitiators and other reactive ingredients is essential. These coatings offer faster curing times, reduced energy consumption, and improved performance.
Smart and Functional Properties: Self-cleaning, self-healing, antimicrobial, anti-corrosion, thermochromic, photochromic, and other functional "smart" coatings utilize advanced materials like nanocontainers, polymers, and other responsive particles such as lead zirconate titanate that require specialized mixing techniques.
A strategic and periodic reevaluation of mixing operations will help manufacturers address the new needs and processing improvements that novel formulations may necessitate. The practical approach is often a combination of tried-and-tested traditional mixers and new technologies that push the envelope.
Mixer Selection Based on Viscosity and Shear
High Speed Dispersion and High Shear Mixing
The classic High Speed Disperser features an open-disc blade that travels at roughly 5,000 ft/min creating a vortex in which dry ingredients can be poured. Due to the vigorous flow, this style of mixer is well-suited for formulations that require a fine, stable dispersion and for rapidly wetting out powders and breaking down loose agglomerates in low- to medium-viscosity batches up to around 50,000 cP. The standard disperser is supplied on a hydraulic lift to raise/lower the blade during the mixing cycle to avoid “stratification” or possible layering inside the batch.
For formulations that require more intense shearing and homogenization than saw-tooth blades can provide, batch and inline High Shear Mixers are available. These rotor/stator mixers are ideal for reducing the size of agglomerates and droplets in fine dispersions and emulsions to create scalable, highly repeatable products with viscosities up to around 10,000 to 20,000 cP.
Traditional batch-style High Shear Mixers consist of a single-stage four-blade rotor that turns at high speed within a stationary stator creating intense hydraulic shear. The rotating blades pass the stator, mechanically shear particles and droplets, and expel material at high velocity into the surrounding mix. As fast as material is expelled, more is drawn into the bottom of the rotor/stator generator, which promotes continuous flow and fast mixing. Interchangeable stators provide unlimited flexibility to adapt to a variety of product formulations. The typical rotor has a tip speed of around 3,000-4,000 ft/min, but more robust designs are available like the ROSS PreMax (US Patent No. 6,000,840) which runs up to 5,000 ft/min. The PreMax rotor is specially contoured for high pumping capacity and shear intensity. It generates vortices above and below the mix head which further accelerate powder additions and turnover rates.

Like the batch models, inline High Shear Mixers reduce the size of agglomerates and droplets but are installed external into the tank, either in a recirculation set-up or truly continuous (single pass) operation. Most large batch mixing processes can be optimized with the addition of an inline rotor/stator mixer. The supplemental agitation and shear provided by an inline mixer boosts production by reducing cycle time. Multiple batch tanks can be serviced by a single inline mixer and benefit from its pumping capabilities. Another practical advantage to an inline mixer is that it is easily installed without disturbing pre-existing equipment.

For applications requiring even greater mixing energy, Ultra-High Shear Mixers that generate tip speeds over 11,000 ft/min are the best candidate to provide superior dispersions and tight particle-size distribution. One example is the ROSS line of Ultra-High Shear Mixers with three rotor/stator designs available – the X-Series, QuadSlot, and MegaShear. These inline devices generate very fine dispersions and emulsions superior to those produced by conventional multi-stage rotor/stators and colloid mills.
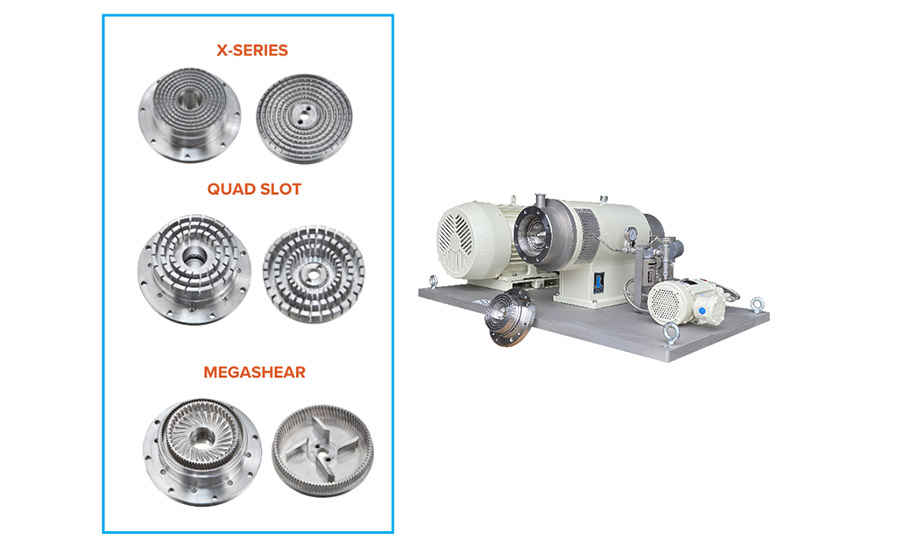
Efficient Powder Induction
Rapidly incorporating large amounts of powders while preventing lump formation or "fish eyes" is a major challenge when working with modern coating formulations containing high solids loadings or specialized fillers. High-Shear Mixers with direct powder injection technology streamline this process. For instance, the ROSS Solid/Liquid Injection Manifold (SLIM) generates an intense vacuum in the high shear zone and inducts powders directly into a fluid stream — dry and wet materials are combined at the exact point where intense mixing takes place, not in an upstream eductor. This allows the SLIM to handle large volumes of solids without clogging or agglomerate formation. The SLIM technology not only improves mixing efficiency but also enhances operator safety by reducing dust exposure.
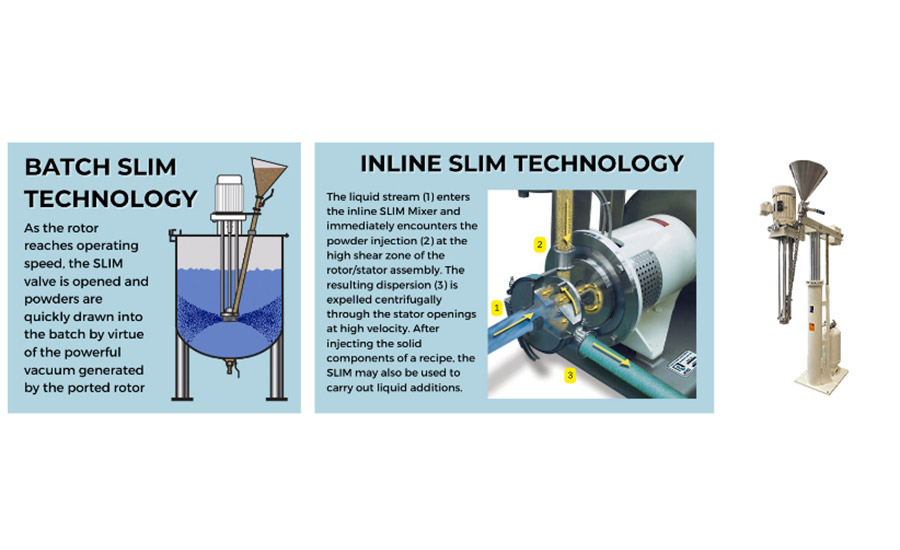
Multi-Shaft Agitator Solutions
For processing requirements that call for homogenization across a wide viscosity range along with uniform bulk movement and heat transfer, Multi-Shaft Mixers employing multiple agitators is an ideal solution. A common configuration is the Dual-Shaft Mixer, which is comprised of a High Speed Disperser and a Two-Wing Anchor. This cost-effective yet heavy-duty design is practical for straightforward applications that do not require intense shearing via a rotor/stator. Another popular option is the Triple-Shaft Mixer consisting of a High Shear Mixer, a High Speed Disperser, and a Three-Wing Anchor. Working in tandem, all three independently-driven agitators can easily handle thick slurries, pastes, gels, and suspensions with viscosities in the hundreds of thousands of centipoise.
These versatile multi-agitator systems allow formulators to wet out powders, disperse agglomerates, emulsify immiscible phases, and control viscosity in a single piece of equipment. Their vacuum-capable design also enables the processing of large batches with improved density and performance properties critical for cutting-edge formulations.
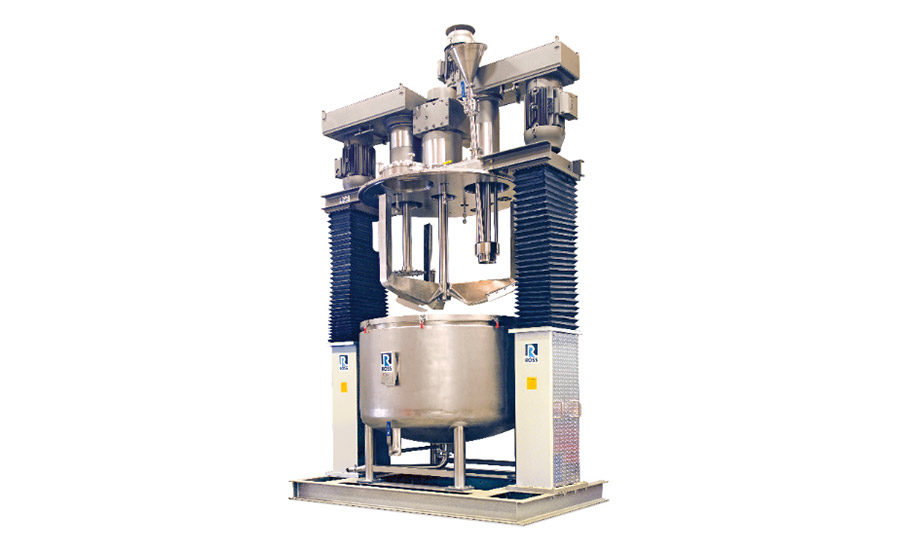
High-Viscosity Mixing
Many modern coatings traverse extremely high viscosity ranges during processing, starting as thin slurries and solutions, then transforming all the way up to the consistency of gels and thick pastes exceeding 1,000,000 cP. This is common when working with rad-curable, high-solids, and other 100% solids formulations. For these challenging applications, robust Planetary Dispersers and Double Planetary Mixers are utilized.
The ROSS patented PowerMix is a hybrid planetary disperser designed to impart a combination of high- and low-speed agitation for mixtures that start out very fluid and eventually thicken up throughout the course of the batching process. Suitable for water-like viscosity up to around 2 million cP, the PowerMix can impart high shear at any stage owing to the combined mixing action of a planetary stirrer and a high-speed disperser. Both agitators revolve around a central axis while rotating on their own axes. The planetary stirrer sweeps material away from the vessel sidewalls and bottom, carrying it to the saw-tooth disperser blade. This accelerates solids wet-out and dispersion while promotes both material and temperature uniformity throughout the batch at all times.
Standard Double Planetary Mixers are equipped with two identical rectangular blades that rotate on their own axes while orbiting on a common axis, the blades travel along the periphery of the vessel while continuously removing materials from the vessel wall and transporting them to the interior. For applications that range from medium to ultra-high viscosity, the patented High Viscosity “HV” blades are available. Featuring a precisely angled helical contour, the blades pass each other in a slicing motion while pushing product forward and downward, thus preventing any materials from climbing up into the gearbox area. Because the blades run at relatively low speeds, this type of mixer can blend shear-sensitive materials and can tolerate abrasive applications.

Integrated Control and Quality Assurance
Powerful mixing capabilities paired with integrated process control solutions ensure consistent batch-to-batch quality. Repeatability is critical when producing high-value coatings, especially as formulators push the envelope with novel ingredients and tight specifications.
Automating a mixing or blending operation with a ROSS control system offers numerous benefits that go beyond reducing operator error and variation. It ultimately increases overall process efficiency in several ways:
Increased product yield and reduced rejects. Especially for applications that are highly process-sensitive, automated systems ensure consistent and accurate mixing, minimizing the risk of human error.
Reduced production costs. A well-designed mixer with a control system requires less labor to operate, produces less waste, and is more energy-efficient, leading to significant cost savings over time.
Shortened cycle times. Automated systems minimize delays attributed to frequent rework, incorrect mixing instructions, and weighing errors, resulting in faster production cycles.
Quicker changeovers. Automated product discharge, draining, and cleaning-in-place (CIP) help minimize machine idle time, allowing for faster transitions between different product batches.
Extended service life. An appropriate control system provides electronic soft start for the agitator(s), overload protection, and other features that help prevent premature wear and mechanical failure. Proper routine maintenance and calibration can also be programmed into the PLC recipe controls, ensuring that operators are less likely to overlook such procedures.
Improved data collection and traceability. Automated systems can record and store crucial process data, such as mixing times, temperatures, and ingredient quantities, which can be used for quality control, auditing, and continuous improvement purposes.
Enhanced safety. Automated mixing systems can be designed with safety features, such as interlocks and emergency stop functions, to protect operators from potential hazards associated with manual mixing processes.
Scalability and flexibility. Automated mixing systems can be easily scaled up or down to accommodate changes in production demands. They also offer the flexibility to handle a wide range of product formulations and mixing requirements.
Optimized mixing is fundamental to unlocking the full performance potential of modern, high-value adhesives, sealants, and coatings. ROSS Mixers has a well-equipped Test and Development Center dedicated to assisting customers through proof-of-concept demonstrations. Located in Hauppauge, New York, the center features a wide range of ROSS mixing and blending equipment. R&D scientists and process engineers are able to work with highly experienced mixing experts to simulate their process, test a variety of candidate machines, and fine tune mixing strategies before a purchase is finalized. As the industry continues to develop innovative chemistries and technologies, access to advanced mixing equipment capabilities and specialized processing knowledge will be critical for manufacturers looking to stay ahead of the curve.
Learn more about ROSS Mixers at www.mixers.com.
Images within the article are courtesy of ROSS.
Looking for a reprint of this article?
From high-res PDFs to custom plaques, order your copy today!