Rheology Control: Novel Use of Pyrogenic Fumed Silica in Wind Turbine Adhesives
The pronounced thixotropy and shear-thinning effect provided by pyrogenic fumed silica allows easy processing of adhesive components even at high silica loading levels.

With over 50 years of experience, WACKER is a pioneer in producing pyrogenic silica under the brand name HDK®. The company’s integrated production system, statistical process control, and highly efficient reactor dynamics combine to create an exceptionally pure and high-performing pyrogenic silica. WACKER creates its pyrogenic silica through hydrolysis of chlorosilane in an oxygen-hydrogen flame. The process yields highly branched aggregates when, upon cooling, they form weakly bound agglomerates, which make up the basic structure of pyrogenic silica. Pyrogenic silica made in the flame reactor is hydrophilic in nature. By post-treatment in a second reactor, WACKER offers hydrophobic pyrogenic silica grades. Hydrophobic grades can be used to control rheology in polar systems. WACKER’s pyrogenic silica has an exceptionally high surface area-to-mass ratio, which facilitates multiple particle interactions in liquid formulations, thereby building a three-dimensional physical network. WACKER’s HDK® is the basis for the rheology control of pyrogenic silica. Obtaining the desired rheology for an adhesive depends on selecting the specific surface area based on the desired specifications and using the correct hydrophilic or hydrophobic pyrogenic silica grade. To create strong thixotropy it is typical to combine opposite polarities provided by pyrogenic silica and the formulation (resin and solvent).
Wind turbine bonding pastes are typically based on epoxy and vinyl ester resins that are applied in thick beads onto half-shells of the rotor blade. Adding WACKER’s pyrogenic silica to bonding paste formulas enables optimal rheology control to meet the demanding requirements for sag resistance. The pronounced thixotropy and shear-thinning effect provided by pyrogenic silica allows easy processing of adhesive components even at high silica loading levels (~5 – 10 wt% loadings). Moreover, pyrogenic silica increases the viscosity of adhesive components during storage and prevents settling. Pyrogenic silica is a versatile solution through various adhesive systems enabling high-level performance.
HDK® H18 is a pyrogenic silica grade that exhibits high hydrophobic properties and performs well in polar formulations such as vinyl ester or epoxy-based adhesives requiring high rheological impact. In addition, it also provides excellent storage formulation stability. This grade is recommended for first-pass evaluation. HDK® H17 is another excellent alternative to facilitate improved dispersion. HDK® H17 displays well-balanced features and is particularly easy to disperse. As shown below, the use of hydrophobic silica provides excellent rheology. Interactions of the polar HDK® N20 with the polar resin have a weak thixotropic effect on the formulation. Whereas the non-polar HDK® H17 particle exhibits a strong thixotropic effect up to 28 days at room temperature.
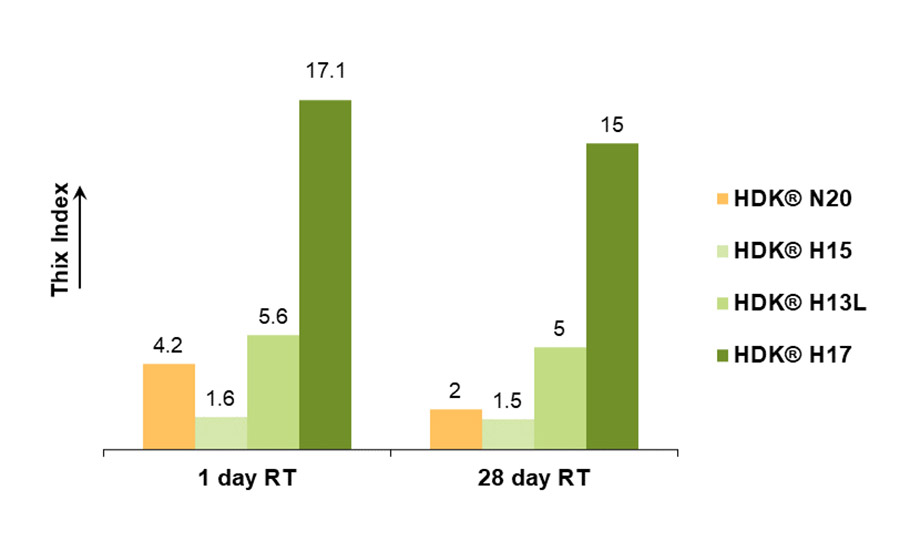
Formulations vary, and it is always recommended to test to evaluate the empirical effects of the pyrogenic silica particle and the mixing conditions. Shown below is a formulation example (1 wt%) of H18 in an epoxy resin. Sufficient shear is a must to achieve optimum dispersion of the pyrogenic silica particles in liquids. Increasing the dissolver blade up to 4000 rpm exhibited the highest effect (25.3) on increasing the low shear viscosity compared to 2000 rpm (11.5) and 3000 rpm (18.6).
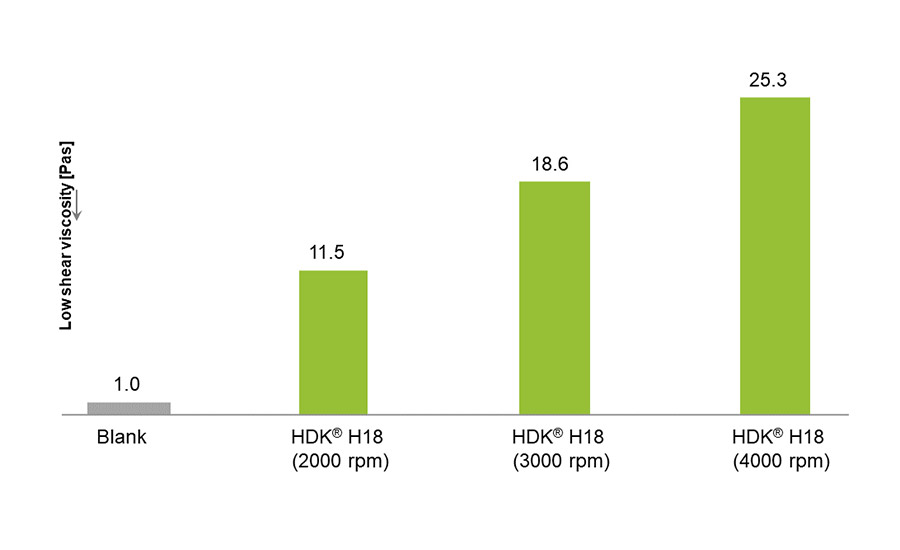
Properties of HDK:
• Synthetic, inert inorganic additive
• Neutral in color
• Migration-resistant
• Thermally stable
• Non-hazardous
Benefits of HDK in Adhesives:
• Highly effective rheology control
• Stable viscosity during storage
• Controlled anti-sag behavior
• Chemical inertness in various reactive systems
• Effective tuning of mechanical properties
Adhesives require reasonable rheology control during manufacture, storage, and processing. The rheological properties of adhesives can be adjusted using suitable pyrogenic silica grades. Adding pyrogenic silica to an adhesive formulation increases the viscosity of the liquid phase, influencing shear thinning and thixotropic flow behavior. The interacting pyrogenic silica aggregate particles form a shear-sensitive three-dimensional network. During storage, the network formation increases the formulation's viscosity and prevents components from settling. The grade and amount of the added silica influences the viscosity at rest. When applying shear forces during the adhesive processing, the branched network breaks up, and the viscosity decreases (shear thinning). Thinning allows for easy processing of the adhesive. After the adhesive has been applied to a substrate, the pyrogenic silica network reforms (thixotropy). This reformation leads to a fast viscosity recovery, effectively avoids sagging, and ensures your adhesive will stay where you want it while curing. In general, pyrogenic silica grades with a larger specific surface area yield more pronounced rheological effects, while grades with a smaller specific surface area are more manageable to disperse. Typically, hydrophobic pyrogenic silica grades offer better results for polar adhesive formulations. The chemical inertness of hydrophobic pyrogenic d silica in polar, reactive resins allows for excellent storage stability. Hydrophilic pyrogenic silica, on the other hand, enables excellent rheology control of non-polar adhesive formulations and is often suitable for use even under high pH value conditions.
WACKER offers a variety of pyrogenic silica grades, each with unique features that can meet performance criteria for various epoxy-based systems.
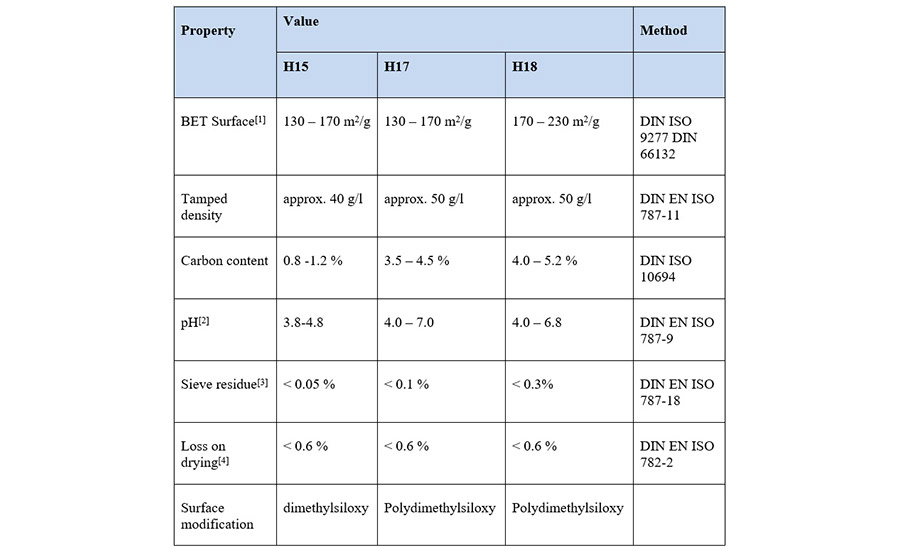
HDK® H18, with its high degree of surface modification, provides superior storage stability and sag resistance to polar adhesives. It achieves high viscosity in vinyl esters at low dosages. At the same time, the high hydrophobicity and the large particle surface area provide good thixotropy. These characteristics make H18 a superior choice over less hydrophobic products (H18) when high sag resistance is a deciding requirement.
Hydrophobic pyrogenic silica grades ensure low viscosity during the application, high viscosity, sag resistance at rest, and anti-settling during storage.
Chemical anchor fasteners, based on vinyl esters and two-component epoxy formulas, are polar adhesives used to secure mechanical anchors in concrete and masonry construction. When augmented with pyrogenic silica, these adhesives prevent sagging in the uncured adhesive, ensuring it does not flow out of the drilled hole. The highly hydrophobic and chemically inert grades, such as H18, H21, and H17, provide excellent thixotropy and enable easy processing and maximal sag resistance. Pyrogenic silica ensures extended product shelf life in polar systems.
If stability in high-pH conditions is a design requirement, then the use of the hydrophilic silica such as N20 should be used. N20 yields good rheological profile in the amine components of epoxy adhesives, but it often requires high silica loadings. Depending on the formula's polarity, hydrophobic siloxane-treated silicas may give a better rheological impact but are not sufficiently stable in high-pH conditions. With HDK®, you can be confident in its stability and reliability, even in challenging conditions.
Packaging
To ensure maximum effectiveness of your products and formulations, various forms of packaging to suit logistics and handling requirements are offered. Packaging size, adequate moisture protection, and specific requirements are crucial factors in determining the optimal packaging for your productivity.
Pallets with Paper Bags
HDK® is available in multilayer, valved paper bags, which can accommodate 10 to 20 kg of product, depending on bulk density. The bags are delivered on pallets that are shrink wrapped with a polyethylene film for moisture protection. If the shrink film is damaged accidentally or single bags are removed, it is advisable to protect the remaining or individual bags by wrapping them in plastic or other appropriate measures.
Big Bags
The big bag solution is available for most pyrogenic silica grades. Big bags are made of woven polypropylene and are suitable for 150 to 200 kg (about 440.92 lb.) of product, depending on bulk density. Big bags are delivered on pallets, shrink wrapped with a polyethylene film to safeguard against moisture. Advice on how to handle the material, particularly how to fluidize and unload big bags is also offered.
For additional information about WACKER and its HDK products, visit www.wacker.com/hdk. For additional product questions and general technical inquiries within North America, contact Dr. John Young, Silicone Functional Additive Technical Manager, at john.young@wacker.com. For inquiries within Europe, contact Dr. Sabin-Lucian Suraru, Silicone Functional Additive Technical Manager, at sabin-lucian.suraru@wacker.com.
Looking for a reprint of this article?
From high-res PDFs to custom plaques, order your copy today!