The Key to Success in Volumetric Filling Systems
How volumetric filling systems help to achieve precise repeatability at high operational velocities.

Nostal6ie / iStock / Getty Images Plus
In today's fast-paced economy, expertly designed and engineered volumetric filling systems significantly boost operational efficiency and profitability through enhanced reliability, accuracy, and flexibility. Reliability minimizes downtime and accelerates production rates, accuracy reduces costly product waste and ensures compliance with regulations, while flexibility empowers companies to adjust to evolving market demands and maintain a diverse product portfolio to respond to market opportunities and increase revenue.
Servo volumetric filling systems play a pivotal role in ensuring that products are consistently packaged correctly and efficiently in a broad range of applications from, the precise dosing of pharmaceuticals into syringes, to swirl-filling cosmetic creams into bottles for distinctive visual appeal, to filling squeeze tubes and cartridges with highly viscous sealants, adhesives, and greases for industrial applications.
Why Servo Volumetric Filling?
Servo volumetric filling, a precision process widely utilized in the packaging industry, excels at dispensing a precise volume of product into containers. The method is preferred for its accuracy, efficiency, and versatility, accommodating a broad range of liquids and semi-liquids across various consistencies and densities, handling viscosities up to 3 million centipoise.

The advantages of servo volumetric filling include consistent product quantities, minimal waste, and fast production speeds, which together contribute to operational efficiency and reduced costs. Servo volumetric filling systems are also less technologically complicated to set up and operate and are easy to clean and maintain.
An alternative method, net weight filling, utilizes a weight scale to measure the amount of dispensed product into the container. It can be a good solution for uniform low-viscosity fluids and dry products sold by weight, such as powders, grains, and nuts. However, they are typically much slower than volumetric filling equipment for higher viscosity greater than 20,000 to 30,000 cps and are usually not cost effective.
Another method, known as time pressure filling, involves larger pressurized containers for maintaining consistent pressure and flow. The amount of product dispensed is regulated by adjusting the duration the valve stays open. Time pressure filling provides less precision and control over the dispensed product quantity compared to servo volumetric filling. Moreover, the time pressure systems are generally larger, more complicated and time consuming to set up and maintain.
Reliability
Reliability in filling systems is a critical business necessity. Servo-driven volumetric filling systems for 30,000 cps and above have demonstrated exceptional reliability and ease of maintenance, ensuring years of trouble-free operation while operating continuously at high throughput rates.
Downtime — When filling systems experience downtime, the entire production line can come to a grinding halt. This disruption results in significant costs related to labor and delayed product delivery.
Product Waste — Additionally, unplanned stoppages lead to the generation of scrap product. This not only represents a direct loss in materials, which adds to production costs, but also impacts environmental sustainability efforts. Waste can be extremely costly in industries like pharmaceuticals where the product is highly valuable.
Maintenance — Servo-driven volumetric filling systems require little maintenance, except for keeping them clean and free of product residue. The programmable logic controller (PLC) will alert operators when the servos need lubrication, which is typically after one million cycles, equivalent to filling a million containers.
Durability — Servo-driven volumetric filling systems have also proven to be remarkably durable. At ProSys, many of our first servo systems, commissioned over two decades ago, are still in production, running continuously without faltering in their speed and accuracy.
The reliability of the filling equipment and the OEE (overall equipment efficiency) is a linchpin in the overall productivity and profitability of manufacturing operations, impacting not just the bottom line but the brand's reputation for delivering quality products on time.
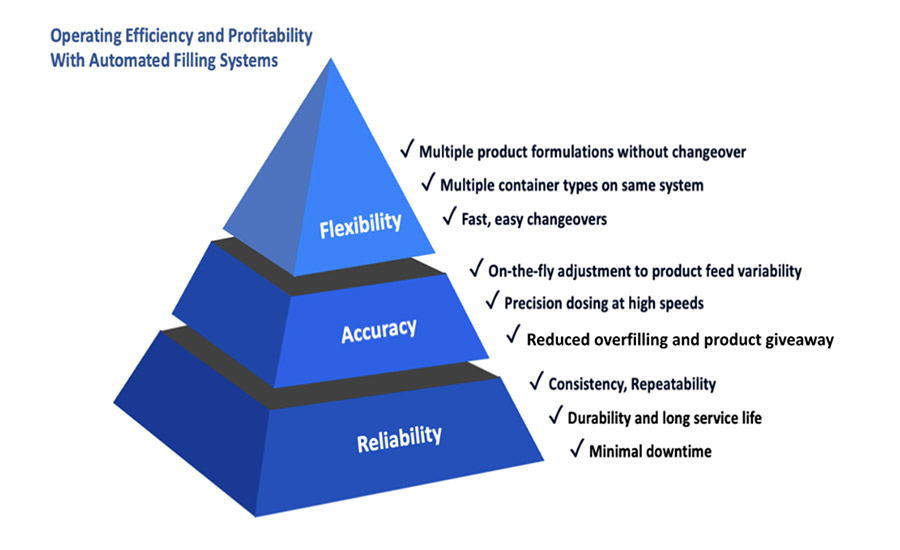
Accuracy
Reliability involves more than just trouble-free operation in the long run; it also includes the precision and repeatability of each cycle.
The accuracy translates into swift payback periods for investments in servo-driven volumetric filling systems. By reducing product giveaway, which happens when systems overfill, companies can significantly cut costs. Even minor overfilling quickly adds up to substantial losses, often running into the hundreds of thousands of dollars per year, easily justifying the investment in precise filling systems.
Furthermore, the avoidance of underfilling is just as critical for maintaining profitability and brand reputation. Filling too little can risk angering customers, potentially leading to lost sales and damaging relationships with end-users. In some cases, especially in strictly regulated industries and countries, underfilling can incur legal fines or force costly product recalls, adding to financial burdens and public relations challenges.
In volumetric filling systems, the operating principle of positive displacement pumps with servo drive ensures high accuracy, consistency, and speed. The programmable logic controller instructs the servo piston speed and stroke distance to precisely control the dosing amount.
Advanced volumetric filling systems can detect fluctuations and make on-the-fly adjustments. They accomplish this by pre-pressurizing and compressing the product as needed to ensure precision and uniformity.
Servo volumetric filling systems can thereby achieve exceptional high accuracy, particularly crucial in industries like pharmaceuticals and animal health where precise dosing is essential. State-of-the-art servo-driven volumetric filling systems consistently provide accuracies within 0.1%, ensuring reliable and precise dosing for critical applications.
Flexibility
The discussion of the significant impact of reliability and accuracy in servo-driven volumetric filling systems on profitability has highlighted substantial cost savings through minimized downtime, waste reduction, and streamlined operational and maintenance processes. The third key attribute, flexibility, also enhances profitability through cost reduction. But in addition, flexibility drives revenue growth by empowering companies to promptly respond to evolving market conditions and capitalize on new product opportunities, innovative marketing strategies and creative packaging initiatives.
The current marketing landscape is characterized by high product mixes featuring shorter product life cycles and an intensified emphasis on enhancing supply chain agility. In such a dynamic business environment, the imperative lies in possessing production capabilities that can swiftly and cost-effectively adapt to changes.
In a typical scenario, a production line needs to efficiently shift from packaging 5000 units of 10-oz construction adhesives in cartridges to a subsequent run of 2000 30-oz cartridges. Similarly, a cosmetics company might need adeptly transition from filling face creams into 1-oz, 4-oz, and 6-oz squeeze tubes to accommodating various size airless pump bottles.
The best flexible filling systems are designed and engineered to adapt to a variety of container types and fill volumes swiftly and effortlessly. They shine in handling a broad range of products with varying viscosities, not just meeting current production demands but also prepared to tackle future needs. This forward-looking strategy goes beyond immediate plans, ensuring the investment is future proofed.
PLCs must support hundreds of SKUs or more, with an HMI that simplifies recipe creation and recall. Operating an HMI for servo-driven systems involves a straightforward push-button process, streamlining changeovers compared to traditional pneumatic cylinders and cams that necessitate manual adjustment.
The servo filling systems from ProSys require much less changeover time compared to other filling systems for ultimate system flexibility. To change over to various sized containers, simply swap out a few size-change parts, make a couple of toolless adjustments with ProSys’ easy-to-read digital read outs or DRO’s, and pick the new recipe in the HMI and begin production. Quick SKU changeovers equal thousands of dollars per year in labor and production costs and deliver unmatched flexibility to your bottom line.
Keys to Efficiency and Profitability
Reliability, accuracy, and flexibility are crucial for efficiency and profitability in volumetric filling systems. Achieving precise repeatability at high operational speeds is key to success. Reliability establishes the groundwork for trouble-free operation and long-term durability, minimizing downtime. Accuracy prevents costly product waste, while flexibility takes packaging operations to the next level, facilitating revenue growth and responsiveness to market opportunities.
Learn more about ProSys Fill, visit https://prosysfill.com.
Looking for a reprint of this article?
From high-res PDFs to custom plaques, order your copy today!