Optimized Filler Featuring Low Density, Flame Retardancy, and Thermal Conductivity
An article based on a paper presented at a meeting of the Thermoset Resin Formulators Association, in Denver, Colorado, May 8-11, 2023.

Pasha Pechenkin / iStock / Getty Images Plus
Thermally conductive or flame-retardant thermosets have a long history in the thermoset industry. New applications like gap fillers or battery housings for lithium-ion batteries (LiB) drive the trend towards higher filling levels.
In classic thermal conductive applications filler loads of 70-75 wt.-% can be obtained comparably easily, while in gap fillers for batteries filling levels of 85-90 wt.-% and even higher must be realized. The use of innovative viscosity-optimized aluminum hydroxide from APYRAL® HC grade-line generates thermoset resins with thermal conductivity (TC) levels of 1-3 W/mK while having outstanding features like low density, low tool abrasion, and good dispensing properties in combination with high flame retardancy.
In this paper, parameters like thermal conductivity, viscosity, and flame retardancy properties are discussed.
Thermal Conductivity and Flame Retardancy
Background
The automotive industry is going through a revolutionary change from combustion engines to electrical drive units. Safe, rapid charging technologies and longevity as well as reliable fire safety are inevitable for a broad consumer acceptance of electrical vehicles (EV).
The major components for an efficient thermal management system are the electrical motor, the power electronics (e.g., inverter and converters), and finally the lithium-ion battery (LIB). The thermal conductivity (TC) of the components forming the battery case, the gap fillers in the battery stacks, various adhesives, and gaskets as well as the motor coil encapsulation, all these components require very different material solutions based on existing or totally new designed polymer compounds. Probably the most important component of a modern electric vehicle is the LiB itself (see Figure 1).
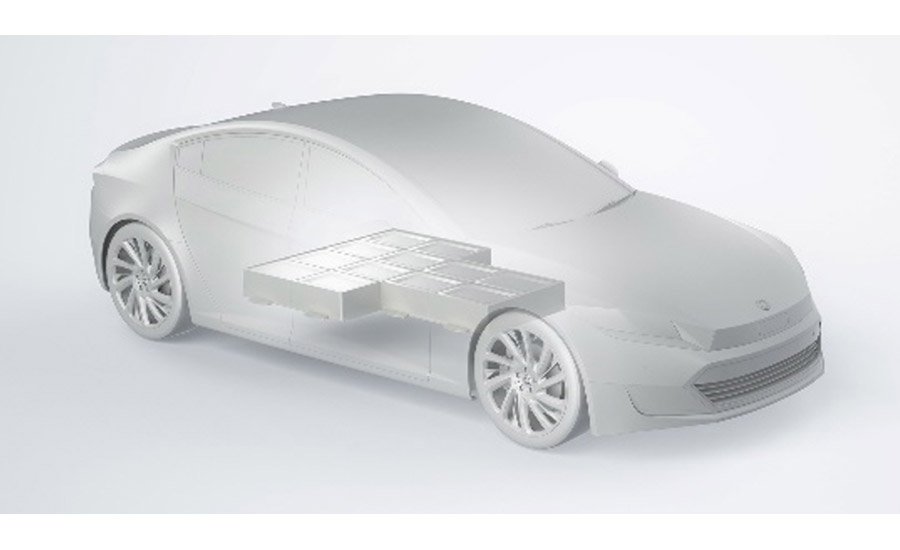
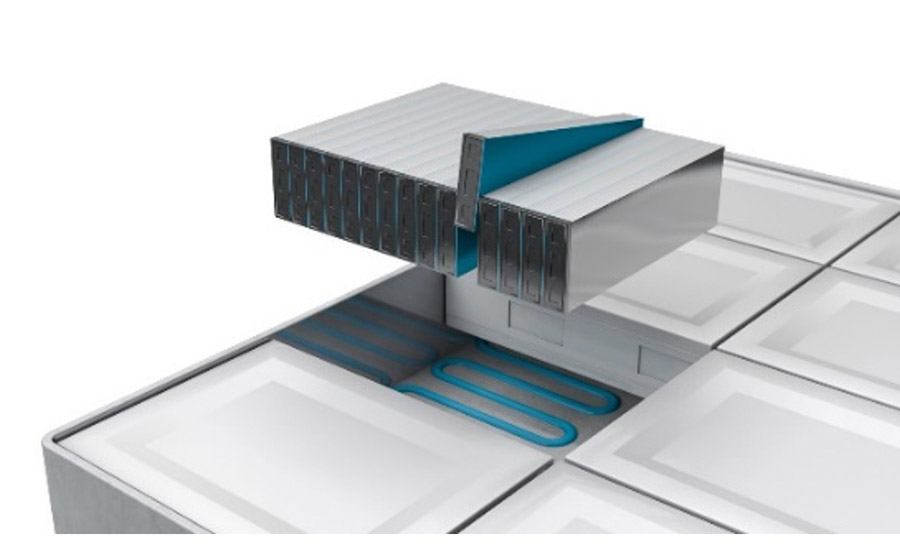
To keep the LiB from overheating during fast charging, the heat has to be conducted out of the battery stacks through the battery enclosure to an external (active) cooling system. Here the thermal conductive adhesive (TCA) attaching the stacks to the enclosure and especially the thermal conductive gap filler between the single stacks of the battery module (see Figure 2) play key roles.
For gap fillers, usually a thermal conductivity of 2–3 W/mK is demanded, which requires the use of thermal conductive fillers at levels often significantly above 80 wt.-%. While gap fillers and classic thermal interface materials (TIM) in the electronic industry are used in scale of some grams per unit, a modern LiB requires kilograms of a gap filler. In this regard, easy and fast dispensing plays a critical role to enable short assembly times.
The Role of Viscosity and Density
Nabaltec AG has developed high-performance fillers based on viscosity-optimized aluminum-tri-hydroxide (Al(OH)3, ATH) – APYRAL HC. Their optimized particle size distributions simultaneously allow high packaging densities (resulting in high TC values) and extremely low viscosity levels. Carefully chosen surface treatments, like in APYRAL HC 503H, can reduce the viscosity level even further and can provide hydrophobicity, which enables the filling of moisture-sensitive polymers like polyurethane (PUR) or silane modified prepolymers (SMP) and even the filling of highly reactive isocyanates in PUR with good storage stability.
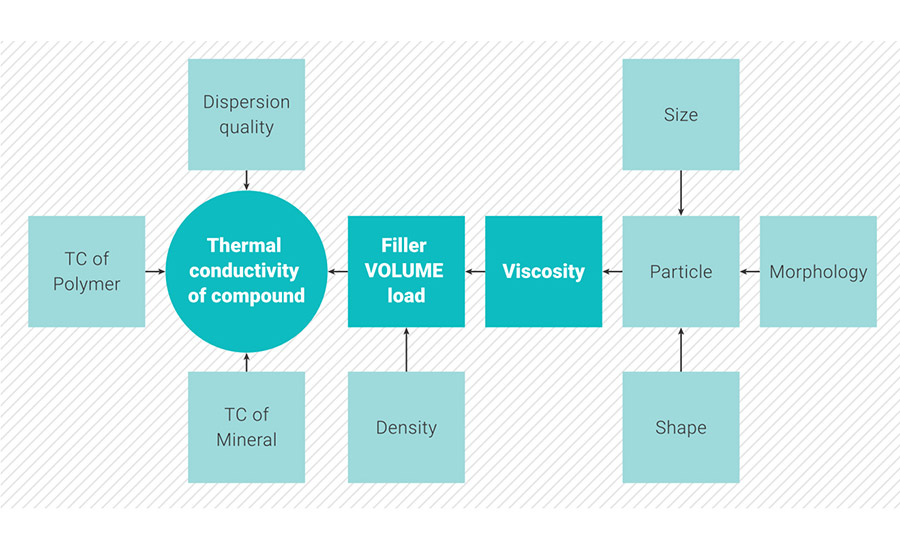
When trying to improve the TC of a polymer compound, a set of parameters of the compound ingredients must be considered. Figure 3 gives a simple overview of these parameters. In first place, one usually considers the thermal conductivity of the resin and of the mineral filler. The TC of most resins is very low. Actually, most resins act as thermal insulators and prevent the conduction of heat. Consequently, the TC of the mineral filler is in focus. For an overview of selected mineral fillers for polymer applications including their TC values please compare Table 1.
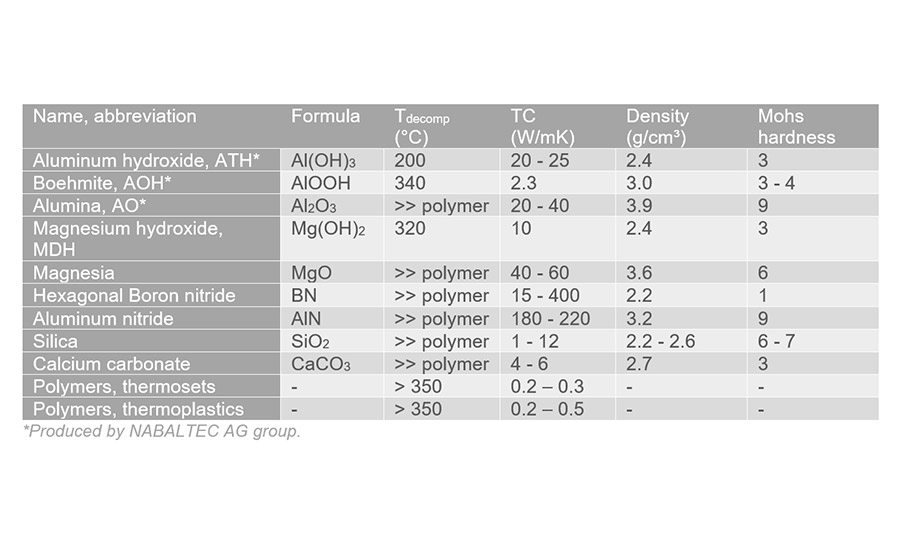
Naturally the formulator seeks fillers with high intrinsic TC values, like boron nitride (BN), aluminum nitride (AlN), alumina (Al2O3, AO), or magnesia (MgO). Electrically conductive fillers like graphite, carbon nanotubes, or metal particles cannot be applied, as most gap fillers and TCA need to be electrical insulators. Historically, alumina (calcined ground or spherical) has been and is widely used in TC applications based on thermosets, while in thermoplastic applications its use is limited by the strong abrasion occurring in the high-shear equipment used for compounding (e.g., twin screw extruders, Banbury mixers, etc.) and injection molding (see Mohs hardness in Table 1). Hence, the low hardness of ATH is another important parameter favoring the use of viscosity-optimized aluminum hydroxide.
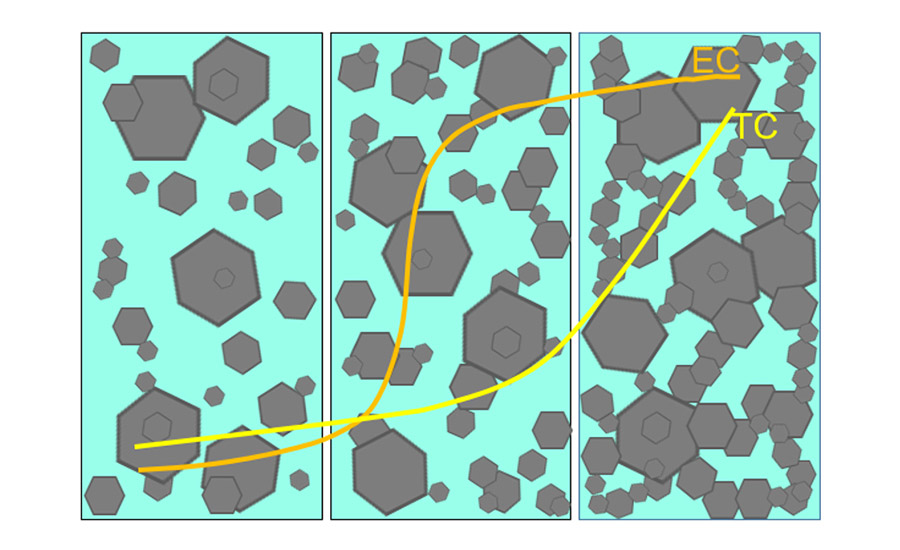
However, the most important parameter is the filler loading level. This is understandable as one tries to replace as much of the insulating polymer with the better-conducting mineral. Ideally, the heat-conducting particles need to contact each other (percolation threshold level, see Figure 4) to raise the conductivity of the composite significantly.
Ultimately, the formulator must gain as high filling levels as possible. Therefore, the dominating factor is the viscosity performance of the filler.
To demonstrate this, results of viscosity-optimized aluminum hydroxide in a polyurethane resin (PUR) are shown in Figure 5. The graph on the right shows the influence of the filler loading on the resulting viscosity increase in comparison to other mineral fillers. Likewise, the TC (graph on the left), the viscosity is rising strongly with increasing filler loads. However, the rheological performance of alumina is lagging far behind viscosity-optimized aluminum hydroxide.
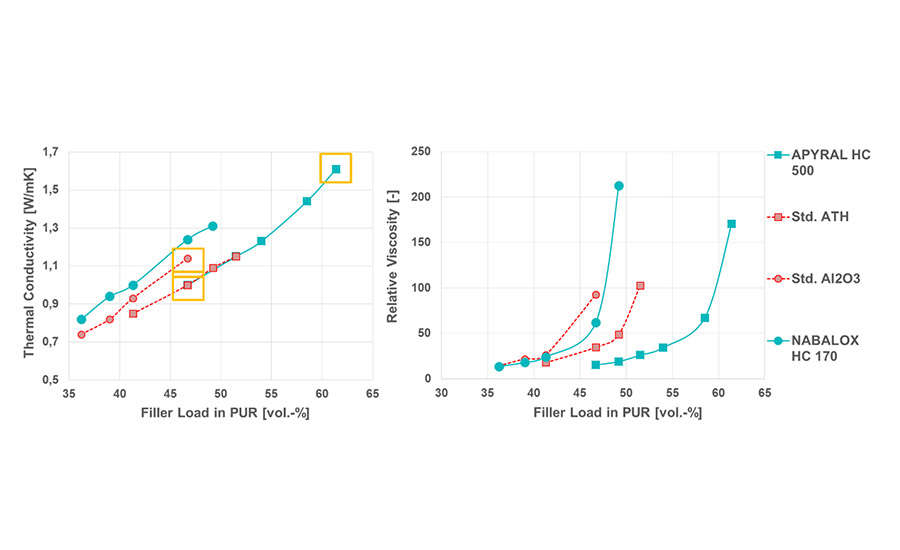
The density (specific gravity) of the filler plays an important role. Low-density fillers will gain a higher volume loading at the same loading level by weight. While alumina has a comparable high density of 3.9 g/cm³, APYRAL HC has a lower density (2.4 g/ml). This fact leads to comparable low polymer fractions when the viscosity-optimized aluminum hydroxide is used and the necessary threshold level is reached at comparably lower filler loadings by weight (see Table 2). The filler loading by weight for the corresponding highest filling level of the viscosity-optimized aluminum hydroxide and optimized alumina is identical at 78.1% (see Table 2), but the resulting TC of the viscosity-optimized aluminum hydroxide is higher (refer to left side of Figure 5). Ultimately, APYRAL HC-filled compounds with higher TC values can be obtained despite the lower intrinsic TC value of ATH compared to alumina (See Table 1).
Furthermore, this is a very important point when calculating the mass-based formulation cost versus the volume-based application cost, where a certain volume must be filled.
The unique properties of APYRAL HC technology of Nabaltec AG were demonstrated in several resins with varying viscosity and intrinsic TC levels. The results are displayed in Figure 6. Depending on the viscosity level and the mechanical properties (e.g., crosslinking degree) of the resin, different loadings and TC levels close to 3 W/mK can be gained. This qualifies the viscosity-optimized aluminum hydroxide as ideal candidates for modern TIM and especially gap fillers for EV batteries.
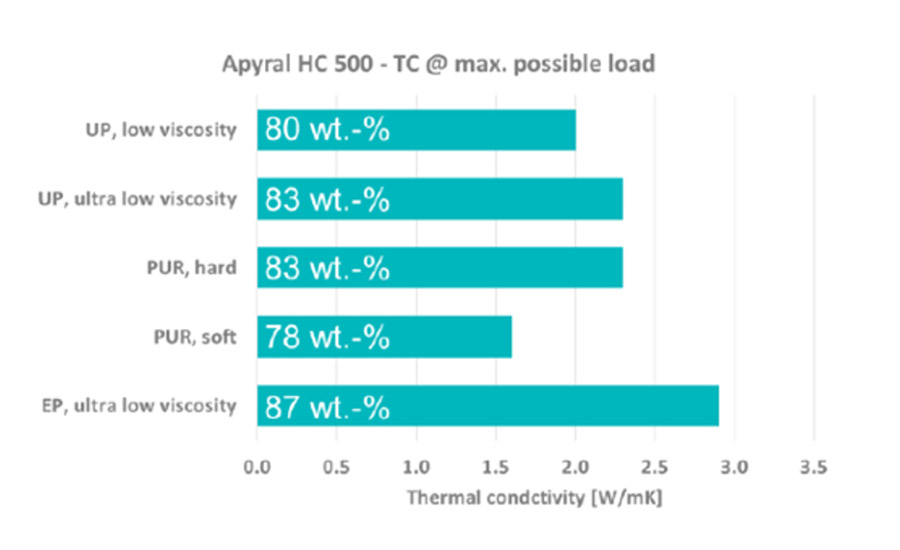
Flame Retardancy on ATH-Filled TC Compounds
Background
Like other electric components, LIBs belong to the safety-sensitive components of an EV. Such components need to fulfill fire safety requirements. While final standardization is still in progress, materials in use are commonly requested to fulfill flame retardancy classification according to the UL 94 V0 (similar to E&E applications).
Even when using alumina at high filling levels in compounds that fulfill the required 3 W/mK, a UL94 V0 classification is not easy to achieve. Therefore, additional flame retardants must be used, which leads to higher cost and even higher viscosity. This is not the case with APYRAL HC, which is a well-known mineral flame retardant. In many resins, a UL94 V0 classification is already achieved with filler loadings of 60–65 wt.-%. When it is used at loadings enabling 2.5–3 W/mK reported above, often very stringent flame retardancy classifications e.g., lined out in EN 45545 (European railway standard) or CPR (European Construction Regulation) can be achieved.
Cone Calorimeter Results
Exemplarily, Figure 7 shows the results of the cone calorimetry measurement of polyurethane resin (PUR), unfilled as well as with high filler loading of the viscosity-optimized aluminum hydroxide and standard-calcined and ground alumina. The tests have been performed on 2 mm thick plaques (10 cm x 10 cm) at a radiation of 50 W/m². Like the approach regarding viscosity and TC, volume-based filler loadings at 46.7 vol% with viscosity-optimized aluminum hydroxide and alumina have been carried out. Additionally, a loading of 61.4%vol has been performed — a filling level that could not be realized with alumina (see the data in Table 2, the weight-based maximum filler load applied for viscosity-optimized aluminum hydroxide and alumina is identical at 78.1%wt).
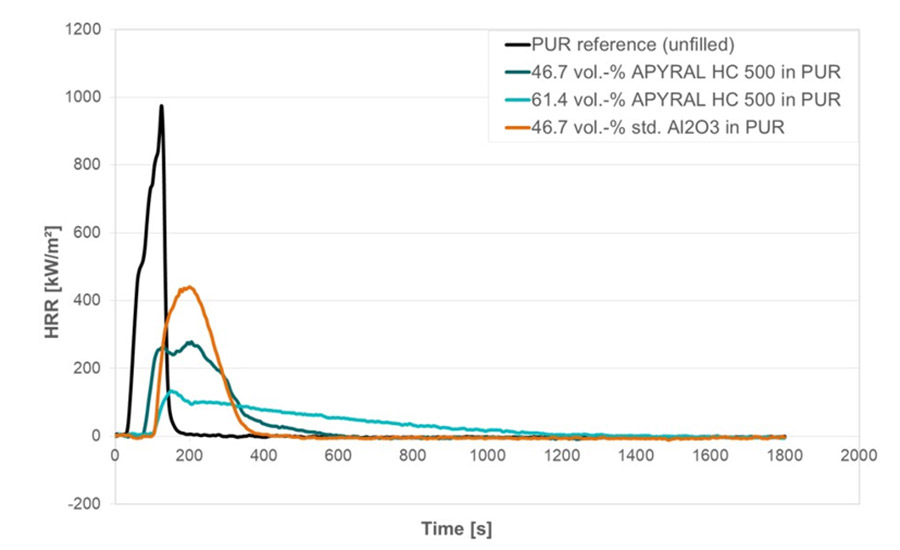
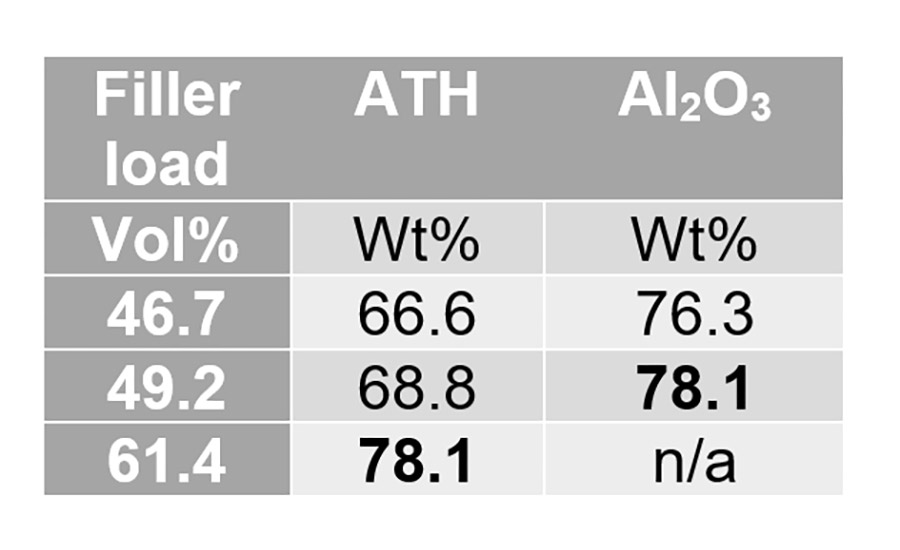
The addition of the viscosity-optimized aluminum hydroxide leads to a significant reduction of the peak heat release rate, which means in effect a considerably improved flame retardancy.
Modern flame retardancy standards focus more and more not only on the flame retardancy itself, but the amount or rate of smoke emission. As ATH is a very strong smoke suppressant, the advantage of a highly APYRAL HC-filled compound is even more visible (See Figure 8).
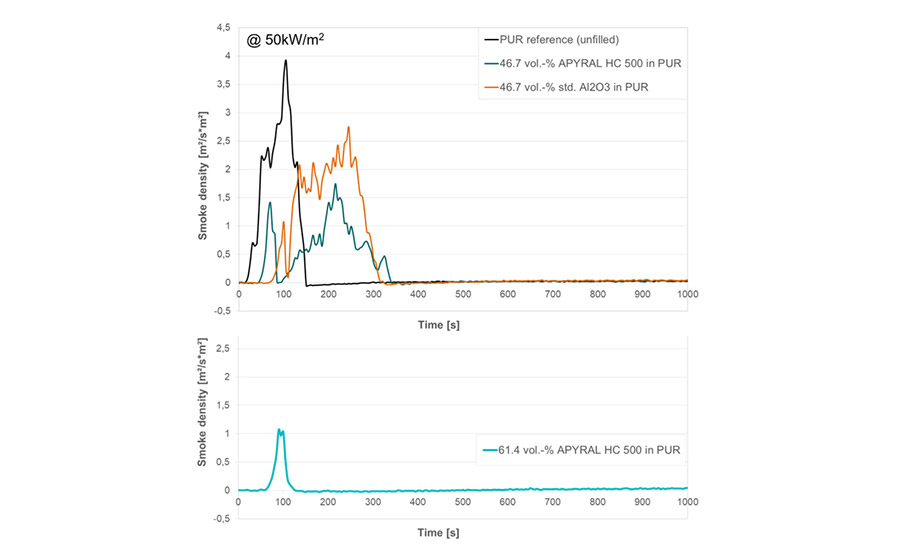
Highly filled glass fiber-reinforced plastics (e.g., SMC / BMC) are already in use when severe flame retardancy classifications are required. This qualifies the viscosity-optimized aluminum hydroxide per se for glass fiber-reinforced battery housings in an EV.
Hence, viscosity-optimized aluminum hydroxide is not only a filler enabling required thermal conductivity but also features excellent ASA flame retardant and smoke suppressor, enabling additional value and performance for broad use in EV applications.
Conclusions
Viscosity-optimized APYRAL HC grades can be a very versatile product as it can be used as a very effective thermal conductive filler that acts as a flame retardant at the same time. Very efficient formulations can be realized in various thermoset resins to meet the demand of cost gap fillers and thermal conductive adhesives, TCA, as well as effective battery housings in EV-batteries.
Learn more about Nabaltec AG at https://nabaltec.de.
Looking for a reprint of this article?
From high-res PDFs to custom plaques, order your copy today!