Hydrogenated Styrenic Block Copolymers for Adhesives and Sealants
SEBS are well-positioned as high-performance materials within a circular economy for their high contribution in the reduction of carbon footprint.

Portra / E+ via Getty Images
In the diverse segments of the adhesives and sealants market, various adhesives based on different polymers are available, including polyurethanes, polyolefins, acrylics, silicone, latex, polyvinyl acetate, polychloroprene, Hot SBR, SSBR, and styrenic block copolymer (SBC), among others.
Styrenic block copolymers (SBC) are categorized into two main types: non-hydrogenated and hydrogenated. Within these categories, we find SBS (styrene-butadiene-styrene), SIS (styrene-isoprene-styrene), SEBS (styrene-ethylene/butylene-styrene), and SEPS (styrene-ethylene/propylene-styrene).
SEBS are produced through the hydrogenation of SBS, during which butadiene double bond segments are selectively hydrogenated to obtain a copolymer with enhanced chemical stability. In the anionic polymerization process of SBS, where butadiene can be added to the polymer chain in 1,4-addition, resulting in a double bond positioned in the middle of the chain; this bond can exist in either a "cis" or "trans" configuration. Additionally, butadiene may also be incorporated in 1,2-addition, leading to a double bond that extends from the main chain (short ramification), forming vinyl structures. The selective hydrogenation of the butadiene segment of the SBS leads to the formation of a random ethylene/butylene copolymer. See Figure 1.1
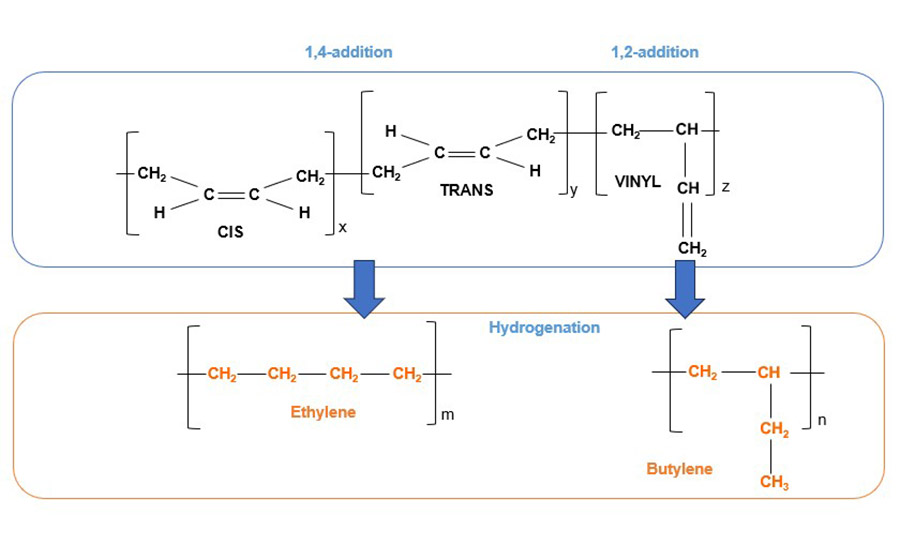
In SEBS, the level of hydrogenation of butadiene unsaturation is greater than 99%, which provides the following advantages over non-hydrogenated styrenic block copolymers (SBS):
- Excellent weatherability
- UV light and ozone resistance
- Excellent low-temperature properties
- Excellent electrical insulation.
- Superior heat resistance (>200 °C)
- High transparency
- Excellent oil absorption
- Excellent compatibility with polyolefins
- Improved aging resistance
- Excellent mechanical properties
- Raw material that is compliant with the circular economy due to its durability
Considering the properties and advantages of SEBS, as well as analyzing various market specifications for adhesives and sealants, Table 1 shows the potential market segments where SEBS are used or could be utilized.
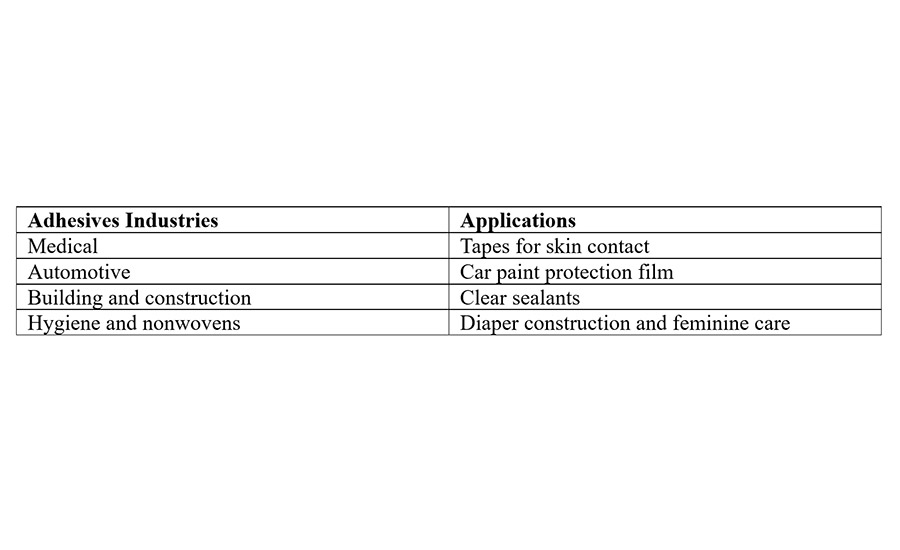
Table 2 outlines the key characteristics of SEBS proposed for use in formulating adhesives for medical tape applications, solvent-based clear sealants, and hot-melt adhesives for hygienic applications, the focus areas of this study
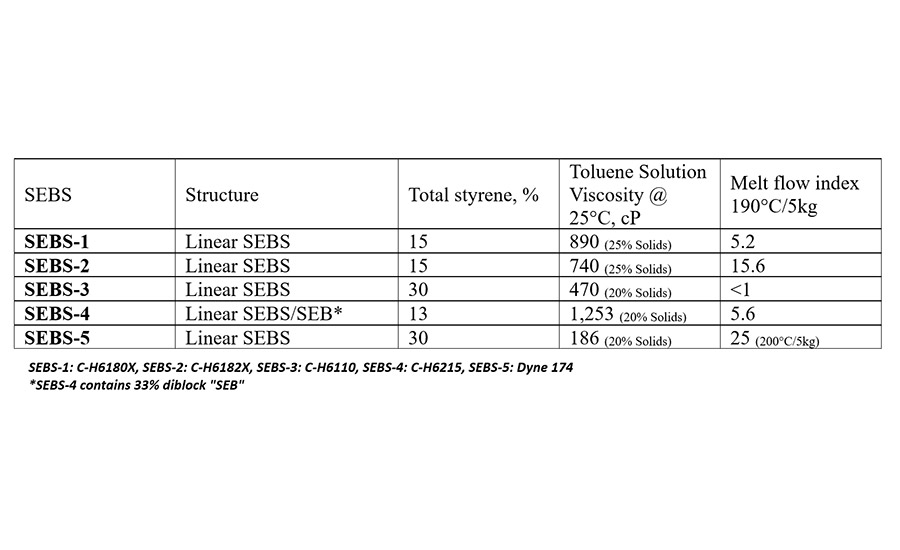
SEBS for Medical Applications
In the medical industry, adhesives fulfill a wide range of functions, from basic applications such as labeling medicine bottles and blood bags to specialized uses like assembling medical equipment and providing healing, surgical, or neuromuscular tapes. When focusing on tapes for medical applications, three dominant technologies currently stand out: acrylic adhesives, silicone pressure sensitive adhesives (PSAs) or soft silicone gel adhesives, and synthetic rubber adhesives.2 The performance of these adhesives for medical tapes must primarily meet the following requirements:
- No skin irritation during wear
- Sterilization compatibility (ethylene oxide, gamma, steam)
- Breathable backings (MVTR - moisture vapor transmission rate (~ 400 g/m2*24h)
- Initial tack
- Peel adhesion (Low to medium)
- No skin trauma on removal
- No mass transfer of adhesive on dressing removal
SEBS are ideal materials to offer an alternative technology to the formulation of adhesives for medical applications due to their unique properties. Their resistance to degradation allows them to withstand various sterilization treatments, and they demonstrate excellent compatibility with medical tape backings (filmic, non-woven, and foam) as well as with polar materials used in their manufacture, such as PET, PE, PU, and cellulose.2,3
The SEBS-1 and SEBS-2 grades feature low molecular weights, which correlate with their low toluene solution viscosity (TSV) and high melt flow index (see Table 2). This property ensures that the adhesive maintains good processability at low temperatures, thereby preventing damage to the substrate during application. Furthermore, the elastomeric segments (85% ethylene-butylene) of these SEBS are highly compatible with tackifying hydrogenated hydrocarbon resins, resulting in adhesives with excellent tackiness. The combination of low molecular weight and reduced styrene content makes these SEBS particularly suitable for achieving low peel strength (Peel 180°), enabling easy removal without causing trauma and minimizing the risk of adhesive transfer to the skin.
Table 3 presents the model formulation for medical tapes where concentration is expressed in parts per hundred rubber (phr). This formulation utilizes a combination of hydrogenated hydrocarbon resin (HHR) with varying glass transition temperatures. HHR demonstrate excellent compatibility with SEBS and are classified as specialty resins due to their strong resistance to oxidation, light color, and lack of odor. When combined with a colorless paraffinic oil, this formulation yields hot-melt adhesives with favorable physical characteristics suitable for medical applications. Figure 2 illustrates the initial hot-melt adhesive appearance and its color evolution over time, after undergoing accelerated aging in a heat chamber at 177 °C.
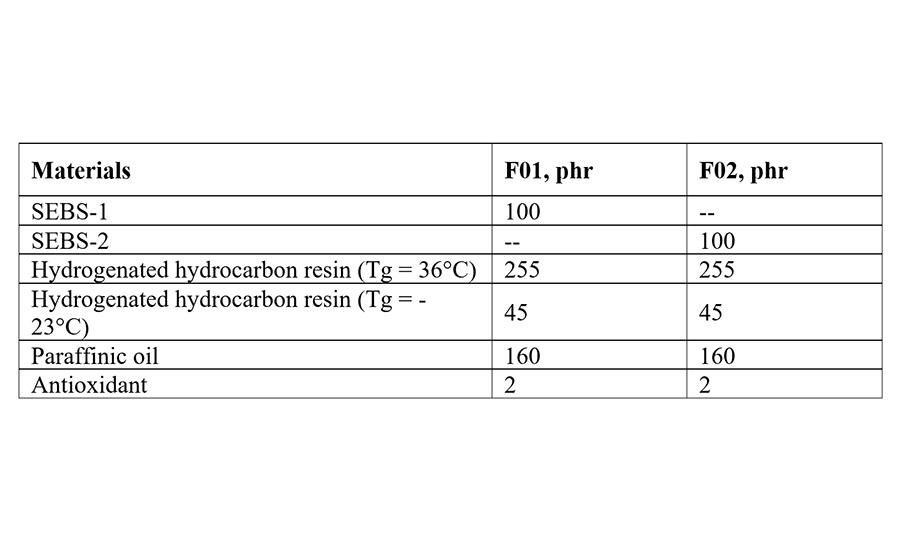
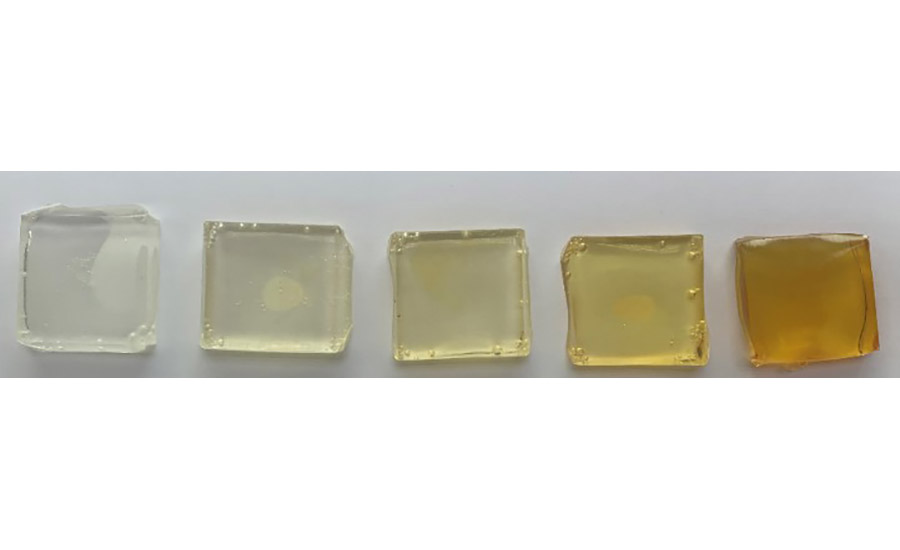
The evaluation of processability and adhesive properties (coating weight: 22 g/m²) for adhesives F01 and F02 are presented in Table 4. Figure 3 shows a comparative analysis of adhesive properties against a pair of commercially measured tapes with different backings, indicating that the proposed adhesives F01 and F02 can achieve a level of tackiness that is similar to or better than that of the commercial tapes, while exhibiting a lower adhesion value (Peel 180°). This characteristic facilitates easier removal without damaging the substrate (skin). 4
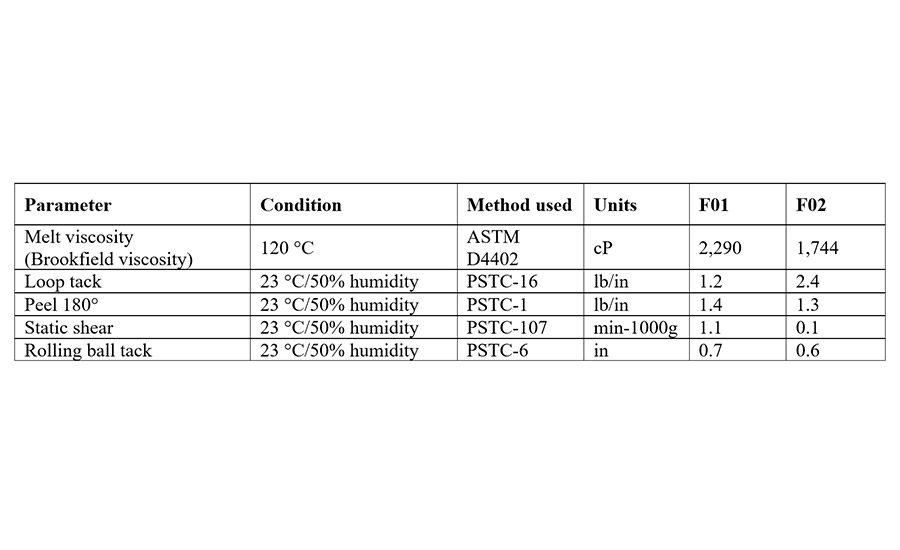
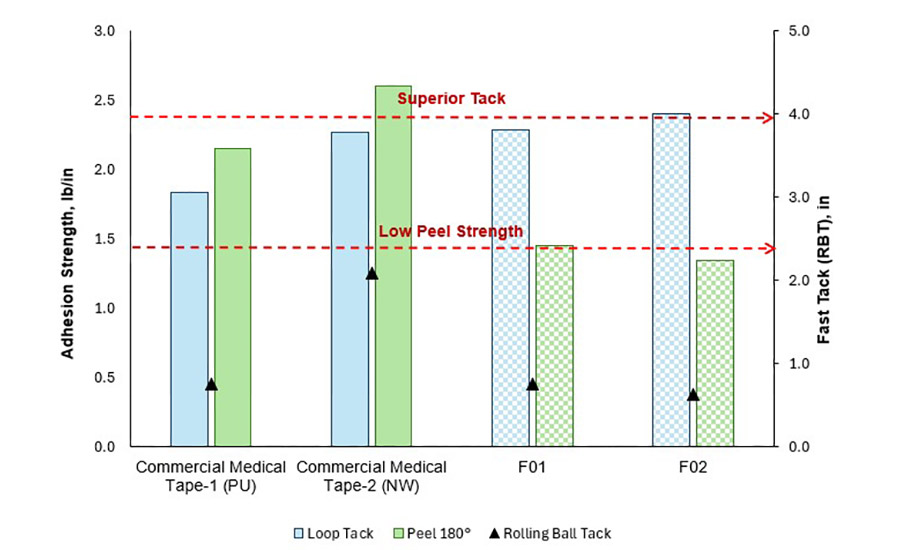
Based on the properties of SEBS and the characteristics of the formulated hot-melt adhesives, the following conclusions have been drawn:
- Excellent processability at low temperatures (120 °C) enables the development of a sustainable HMPSA that requires less energy consumption, thereby reducing the carbon footprint.
- Prevention of damage to backing occurs due to high impregnation temperatures.
- Low peel force ensures that there is no damage to the substrate (skin) during removal.
- Clean removal of the tape from the substrate (skin) leaves no adhesive residue.
Furthermore, there is potential for additional applications where a combination of high tackiness and low adhesion is advantageous, such as in the automotive industry for car paint protection films.
Note 1: The manufacturer or supplier of medical-grade adhesives must ensure that their adhesives pass the biocompatibility testing (ISO 10993), Cytotoxicity and MEM elution (ISO 10993-5) and primary skin irritation (ISO 10993-10).2
SEBS for Building & Construction: Clear Sealants
Clear sealants demonstrate excellent thermal stability and moisture resistance, enabling them to endure a range of environmental conditions without compromising their appearance or performance properties. Consequently, they enhance the aesthetic quality of finishes and are extensively utilized in the construction industry for bonding materials such as glass, metal (including aluminum and steel), ceramics, concrete, and plastics.
A sealant must effectively bond at least two substrates and fill the gaps between them to create a barrier or protective coating. Additionally, it should be capable of:
- Preventing the entry of dirt, air, and cold or hot water
- Controlling vibrations, shocks, and noise
- Maintaining sufficient flexibility to deform and absorb small displacements between substrates, even at low temperatures
- Exhibiting no tack on the exposed surface shortly after application
The properties of SEBS copolymers make them ideal for formulating either solvent-based or hot-melt sealants. Each technology offers distinct advantages depending on the specific application.
Solvent-based Sealants
- Less shrinkage due to high solids levels
- Quick strength development
- Dry very fast
Hot-melt Sealants
Hot-melt sealants are highly valued because they are 100% solids systems and due to the fast set time, which allows applications
- In high-volume production operation
- When traffic or external stress cannot wait
- During periods of inclement weather
Table 5 presents a model formulation for a solvent-based clear sealant, utilizing a combination of hydrogenated hydrocarbon resin (HHR) to develop adhesive properties and PMC9 to enhance cohesive properties. Aligned to several environmental regulations aimed at reducing or eliminating the use of solvents that generate VOCs, a pair of solvents listed in the VOCs exemption list published by the Environmental Protection Agency (EPA) were proposed. These solvents exhibit good compatibility with SEBS, allowing them to effectively dissolve the polymers.4,5
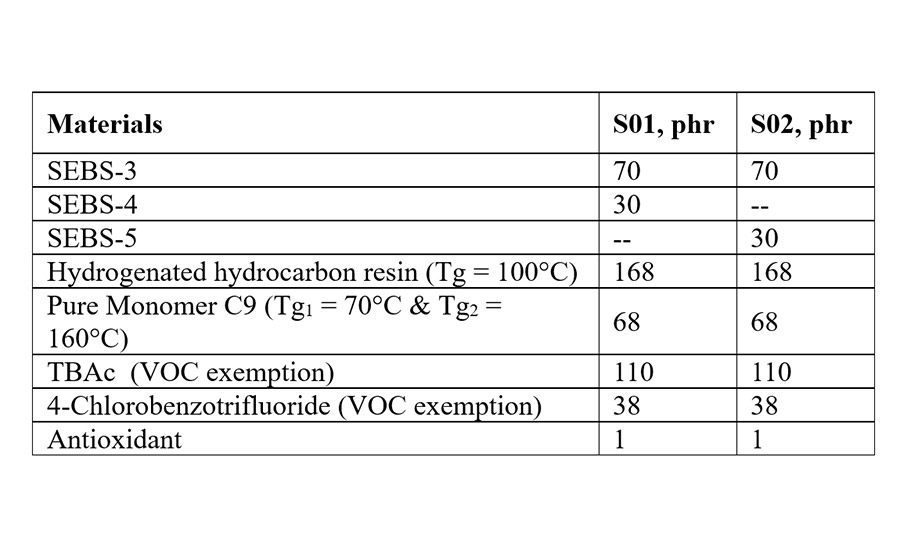
Table 6 presents the results of the fundamental evaluations of sealants S01 and S02, comparing their performance to that of a silicone-based clear sealant. The adhesion properties to substrates such as glass and aluminum are illustrated in Figure 4. The advantages of SEBS-based sealants, S01 and S02, over silicone sealants primarily arise from their structural properties related to styrene content. This content promotes the formation of polystyrene domains, which contribute to the development of "green strength." Additionally, the diblock "SEB" structure and low molecular weight improve both the extrudability of the sealant and its adhesive properties. See Table 2.
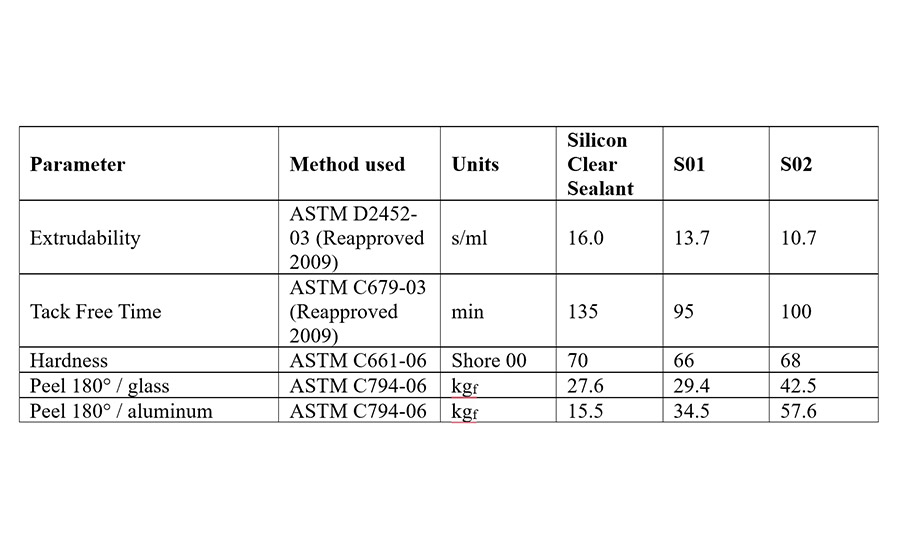
Note 2: Other methods can be evaluated using like reference ASTM C920-08 Standard Specifications for Elastomeric Joint Sealants.

SEBS for Hygienic Applications
The hygiene industry is continuously evolving to provide consumers with improved products that offer greater comfort, better fit, enhanced absorption capacity, and non-invasive properties that do not cause allergies while protecting the skin of both babies and adults.
The adhesive requirements for hygiene products can vary depending on the application area (such as construction, elastic attachment, or positioning); however, the general requirements include:
- Elasticity
- Clear color and no odor
- Wide temperature resistance
- Excellent application properties at high line speeds (with a low melt viscosity of less than 15,000 cP at an application temperature of approximately 120 °C)
- Strong adhesion to specific substrates (particularly those with low surface energy)
- Good thermal stability
Table 7 presents the HMA model formulation for hygienic applications formulated with SEBS.

Currently, the polymers used in formulating hot melt adhesives (HMA) include SBS, SIS, and polyolefins. Each material possesses distinct characteristics: for instance, SBS offers mechanical properties such as elasticity, adhesion, and processability; SIS enhances adhesion properties but has lower mechanical performance due to its reduced styrene content; and polyolefins provide excellent low-temperature processability, stability, and compatibility with low-surface-energy polar substrates (such as non-wovens), although they tend to become quite rigid upon cooling.
Figure 5 illustrates the processability results of adhesive H01 in comparison with two commercial adhesives based on SBS of high styrene content (40 to 43%) used in diaper construction, it is observed that adhesive H01 exhibits slightly lower viscosity at 120 °C compared to the commercial adhesives A01 and A02. This reduction in viscosity is attributed to the lower molecular weight of SEBS-5, which facilitates easier application onto the substrate, thereby maintaining or enhancing productivity. Figure 6 presents the results of their adhesive properties6 (coating weight: 35–37 g/m²), where adhesive H01 demonstrates competitive performance against the commercial adhesives.
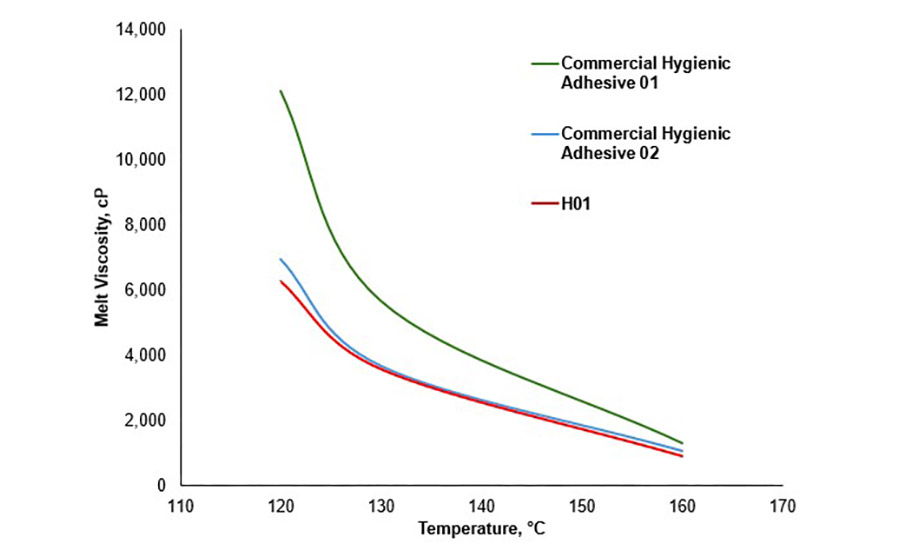

Conclusions
In summary, SEBS materials are known for remarkable resistance to environmental conditions, ozone attack, and high temperature without undergoing degradation that would compromise their chemical structure integrity and end-use application performance. Their intrinsic properties enable these materials to maintain appearance and performance over an extended period of time, making them ideal raw materials for the production of adhesives and sealants, where such requirements are paramount. Moreover, the versatility for synthesizing and tailor-made SEBS with varying molecular weight and structure allows for the formulation of adhesives or sealants that achieve the desired performance on the final application. For instance, SEBS-1 and SEBS-2 in medical tape applications, can provide good tackiness while ensuring low adhesion to facilitate removal without damaging the skin. In sealants, SEBS-4 and SEBS-5 enhance extrudability and adhesion on substrates like glass and aluminum while preserving a crystal-clear appearance. For hot-melt adhesives aimed at the hygiene industry, SEBS-5 ensures good processability at low temperatures and good compatibility with low-surface-energy materials. Due to their high durability, compatibility with VOC-free solvents, and efficiency in adhesive or sealant manufacturing processes, SEBS are well-positioned as high-performance materials within a circular economy for their high contribution in the reduction of carbon footprint.
Learn more about Dynasol Group at https://dynasolgroup.com/en.
References
- Hsieh, Henry L., & Quirk, Roderic P. (1996). Anionic Polymerization Principles and Practical Applications, Chapter 18. Marcel Dekker.
- Tebrake, M. G. (2014). Selecting the right medical adhesive tape: challenges facing the medical device designer. https://multimedia.3m.com/mws/media/1128482O/3m-medical-materials-and-technologies-medical-oem-white-paper.pdf
- Coating and Converting Technologies (Ed.). (2015). Breathable Medical Films. https://ccttapes.com/wp-content/uploads/2014/04/Breathable-films-brochure.pdf
- Ibarra R., J. E. (2021). Adhesives & Sealant Convention. New SEBS for Hot Melt Adhesives with low melt viscosity for Industrial and Medical applications.
- Complete List of VOC Exemption Rules. (s/f). United States Environmental Protection Agency. https://www.epa.gov/ground-level-ozone-pollution/complete-list-voc-exemption-rules
- PSTC Committee Members. (2007). Test Methods for Pressure Sensitive Adhesives. PSTC.
- Annual Book of ASTM Standards Volume 04.07 Building Seals and Sealants; Fire Standars; Dimension Stone. (2009).
Looking for a reprint of this article?
From high-res PDFs to custom plaques, order your copy today!