Manufacturer and Raw-Material Supplier Benefit From Semi-Bulk Material-Handling System
Based on this growing trend of manufacturer/supplier relationships, this article will present a case study of an ongoing, collaborative relationship between Bostik Findley, Inc. (BF), an adhesive manufacturer (the “discharger”); Arizona Chemical Co. (AZC), a major resin supplier (the “filler”); and Process Packaging & Control, Inc. (PPC), a supplier of an innovative material-handling solution.
The case study illustrates how the three companies worked together to design and fine-tune an integrated solution that resulted in a number of benefits for all three companies. In addition to BF’s improved material-handling process, AZC benefits included a solution for the many customer requests for specific, recipe-driven package sizes. PPC was able to design and fine-tune its solution and provide a tested, innovative technology that addresses many of the demands of the adhesives and sealants industry through close collaboration.
The Case Study
At the end of 1998, BF management, concerned with ergonomic issues, internally stated a strategic goal for its hot melt adhesives plants to reduce manual handling of incoming raw material to no more than 30 lb by the end of 2000. Current packaging solutions (e.g., paper bags, drums, Gaylord-type box containers, form-filled plastic bags and traditional bottom-discharge semi-bulk bags) used by raw-material suppliers (fillers) fell short of helping BF meet its stated strategic goal. Full bulk-handling solutions via rail cars or hopper trucks were a possible solution, but required a huge capital investment and fixed-plant infrastructure changes and installations.
PPC’s technology, however, offered steps toward a total semi-bulk material-handling solution between the traditional paper-bag packaging and the full-bulk approach. As with any new technology, however, it could not be built or implemented in isolation. The promised benefits of PPC’s technology would also require adaptations to other processes, including BF’s at-line discharge and staged-discharge processes, and AZC’s bag-loading processes.
Assessment of BF’s Objectives and Discharge Practices
BF management earned enthusiastic support from its “associates” (plant-floor operators) for internal productivity improvements by committing to the 30-lb lifting-limitation goal. Further, BF also determined that the following objectives needed to be met:
- Employee Safety and Ergonomics: Improve operator and working-environment safety and ergonomics by reducing “lost time” injuries, reducing Workers’ Compensation “experience” ratings and increasing compliance with OSHA recommendations.
- Capital Utilization: Require no significant plant-infrastructure changes and a solution that could be used on all plants and vats. The technology platforms in one plant needed to be transferable and adaptable into other plants.
- Operating Costs: Require minimal or no price increases over the direct material cost from the filler using paper bags.
- Process Optimization: Provide operator control of material-discharge rates, therefore eliminating possibility of overloading mixer capabilities and improving the consistency by eliminating ‘human variability’ in the material-addition process. Require the ability to perform partial-bag discharges and re-store the bag for future use. Require ability to handle reasonably poor-flowing materials.
- Modernize Documentation: Document the material processes to help meet stringent and growing ISO production-documentation requirements.
- Environmental Impact: Decrease waste to landfill, resulting in an overall positive impact on the environment. Also improve the environment within the plant by decreasing dust and raw-material waste.
- Supply-Chain Management: Provide a complete solution so that plants, an externally located Supply-Chain Management team and the fillers could each concentrate on its given strengths.
PPC began work with BF in early 1999 and observed the following practices:
In BF plants, there are two approaches to the material-flow process:
- At-Line Discharge: Raw materials are weighed out during discharge while discharging directly into the vat from the original packaging container.
- Staged Discharge: Raw materials are pre-weighed from the original packaging container to an intermediate vessel and then staged-up prior to discharge into the vat. The pre-weighed quantities of the staged raw materials match the recipe for that specific production batch.
When needed, the paper bags were manually removed one at a time from their pallets, slit open using a razor knife, and emptied into the vats or intermediate containers at the plants. This usually involved one to three people and entailed significant lifting, twisting, cutting and dumping motions. It was a manually intensive process that was time-consuming, dusty and resulted in some amount of product spillage each time a vat was filled. The empty paper bags were then collected, bailed, compacted and sent to landfill.
Approximately 10% of BF’s incoming solid, raw-material products arrived in Gaylord cardboard boxes. Usually, pallets of 1,450-lb Gaylord boxes arrived in truckload quantities to the plants. A small hole was cut in the front of the box and then emptied to a specific weight using a tipping device into a steel intermediate tote. The forklift then transported the intermediate tote in front of the mixing vat. The operator gently tipped the tote forward. As the material flow slowed, an associate used a broom to persuade the remaining material out. This resulted in some product spillage and tended to be a dusty process. The empty Gaylord containers were then disassembled and packaged for pickup to landfill.
In another plant, a sizable conveying system was used to convey material from the Gaylord overhead into the vat. This process was slow and the system had low uptime and high maintenance requirements. The system also required pre-weighing of desired amounts prior to conveying.
In a single plant, approximately 5% of the incoming raw material arrived in 800-lb bottom-discharge sacks. The bags were picked up by the four upper loops of the bag using a forklift and carried from the warehouse area to the vat area. The bags were lifted high above the vat and a homemade chute. An operator would then untie the bottom of the bag, and all the material would flow out of the bag into the chute and then into the vat. There was no control over the speed of material discharge and no ability to dispense less than the entire contents of the bag. There was some product spillage with each addition.
There was general dissatisfaction with an operator having to bend under a full, suspended bag while opening the bottom-discharge spout. In addition, the forklift tines dented the overhead dust-collector devices in the process of loading the vats. Finally, if more than 800 lb was needed for a recipe, which in most cases it was, repeated bag dumpings were required.
In all cases, the results from manual-weighing and dispensing processes were documented manually.
Each plant presented differing headroom and floor-space limitations that needed to be addressed in order to provide the proper solution. All plants had dust-collection devices permanently mounted over the mixing-vat openings. One plant had two vat openings located 14-ft high that were loaded from a mezzanine floor. All plants had permanent structural beams that limited the potential for any large infrastructure.
The high-volume raw materials used were resins and polymers. For the most part, they were solid, granular materials that flowed well in most conditions. The plants, however, were concerned about some materials that had a tendency to re-mass, becoming poor-flowing.
Assessment of AZC’s Objectives and Filling Practices
AZC also had its own specific objectives to meet while working with BF on implementing a revised, semi-bulk material-handling process:
- Improve operator and working environment safety and ergonomics;
- No significant plant-infrastructure changes;
- Minimal or no price increases over existing packaging costs using paper bags;
- Improve plant housekeeping, including less dust and less product waste.

PPC’s Control-Flo™ bag is filled through a normal fill spout using industry-standard, four-fill loops located at the top of the bag.
In looking for an alternative that would meet BF’s requirements, PPC noted the following AZC current practices:
-
Approximately 90% of AZC’s outgoing solid, raw-material products were packaged in paper bags and shipped on pallets in truckload quantities.
- The paper bags were filled via a traditional automated paper-bag filling system that was manually loaded and attended to by an operator.
- There was an existing, single big-bag filling device that was used sporadically.
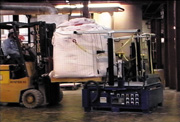
The palletized Control-Flo bag is placed on the Precision-Flo™ unloader. (In a staged process, the Precision-Flo unloader is usually located in a dedicated raw-material staging area.)
The Semi-Bulk Material-Handling Solution
PPC worked closely with BF and AZC to fully assess, design and revise an adequate filling and discharging solution. Early in 2000, PPC delivered a final design that would meet each plant’s needs as well as the needs of the suppliers involved. Since installing the solution in the BF U.S. hot melt plants, nearly 20 million lb of raw materials have been successfully filled at six different raw-material suppliers and successfully discharged at BF.Based on the knowledge that the BF plants would have to meet the requirements of at-line discharge and staged-discharge processes, PPC designed an innovative solution that consists of the following components:
1. Unloaders: Two unloaders, the Precision-Flo™ and Basic-Flo™, automate the precise discharging of powders and granular industrial materials. They are compact and portable and do not require any infrastructure changes. Both are maneuverable independently or by using a forklift and can be easily placed in front of vats or receiving vessels. They work especially well in space-constrained areas, low-overhead environments or areas where dust-collection devices limit access. The unloaders are equipped with massage paddles to ensure that re-massed materials can be discharged.
2. Bags: The bags, called Control-Flo™ bags, can be partially discharged, re-closed and restored. They are capable of holding up to 2,100 lb of most resins and polymers. Since material cannot flow out of the bag, even if its discharge chute is opened, it is extremely safe and easy to use. And it never has to be unsafely lifted high off the pallet to be discharged.
3. Supply-Management System: PPC introduced a unique “pay-per-use” program to help meet the needs of the fillers. The program calls for the filler to purchase an initial quantity of bags. The quantity is usually a 90-day supply requirement. These bags are filled and shipped to the discharger for use. PPC then picks up the empty bags from the BF plants on a weekly basis. PPC administrates, tracks, ships, recycles, refurbishes and certifies the bags for re-use, on an ongoing basis. The filler is guaranteed a continual supply of bags and a pre-known, fixed cost-per-use of the bag. The filler also benefits from a “forever” bag-replacement program. (i.e., if a bag ever wears out due to normal usage, PPC replaces it into the system at no charge to the filler.)

In an at-line process, an operator easily positions the Precision-Flo unloader in front of the receiving vessel, with the bag and pallet on board. The unloader is moved using a forklift or using optional positioning kit. (In a staged process, a PPC intermediate bag that holds a partial material load acts as the receiving vessel when it is placed in front of the Precision-Flo unloader.)
The above components comprise the key elements of the PPC solution. In the typical process:
1. The raw-material supplier fills bags (2,100-lb capacity). The bag is filled through a normal fill spout using industry-standard, four-fill loops located at the top of the bag.2. Bags are shipped and stored on standard pallets.
3. When preparing for discharge, the palletized bag is placed on an unloader using a forklift. As long as the bag is resting on a pallet, its contents will not flow out even if its flap and the chute are opened. In a staged process, the unloader is usually located in a dedicated raw-material staging area.
4. In an at-line discharge, an operator easily positions the unloader, with the bag and pallet on-board, in front of a vat. In a staged process, a bag that holds a partial material load acts as the intermediate vessel when it is placed in front of the unloader.
5. The bag is unloaded via the bag’s discharge chute, located along one of the bottom edges, into the receiving vessel. The bag can be fully or partially discharged to a specific weight. In an at-line discharge, a simple, dependable, hydraulic-driven system gently lifts and empties the bag into the vat. The operator controls the flow rate and discharge amount. In a staged discharge, the proper weight of raw material is emptied into an intermediate bag at a location away from the vat. When the raw-material recipe calls for it, a small, full-discharge unloader delivers the intermediate bag to the vat and fully discharges it.
6. Following discharge, an operator removes the bag and pallet. Empty bags are folded and sent back for recycling. Partially emptied bags are re-closed, labeled with an automatic printout for ISO compliance, and placed back in storage until needed.

The Control-Flo bag is unloaded into the receiving vessel via the bag’s discharge chute located along one of the bottom edges. As long as the Control-Flo bag is resting on a pallet, its contents will not flow out, even if its flap and the chute are open. The bag can be fully or partially discharged to a specific weight.
Specific Benefit Examples at BF
BF experienced reduced material waste, direct labor savings, faster vat-filling time and reduced dust-filter usage. The plant saved about 6 lb of material per batch. This is due to saving the excess material typically left in the paper bag, the material that is lost in the manual-filling process and the material that is lost in the air to later settle on the equipment and on the floor. In addition, the plant saves about 20 minutes in the resin-filling process. This is due to a faster filling process with the new solution and less cleanup time required for the folding, compacting and stacking compared to the paper bags. Finally, BF changes-out their dust-collection filters only one time per day per vat compared with four times per day per vat prior to implementation of the system. Applying these actual savings to a small, generic adhesives manufacturer would lead to a capital payback of less than one year.In addition to the above economic benefits, BF management has also indicated that it has seen the following benefits:
- Impact of this Ergonomic Solution on Workers: “Worker morale is high. They fully support the program. Operator fatigue has ceased to be an issue. This has resulted in increased productivity, throughput and capacity.”
- Impact of Better Documentation for ISO Requirements: “The scales on the unloaders give us the capability to verify the weights of the raw material and give us a printout that serves as evidence that the correct amount of material was used.”
- Impact on Customer Perception: “During all of the customer visits over the past few months, the cleanliness of the plant and the atmosphere of safety have been sufficiently apparent for the visitors to recognize and remark on it.”

In an at-line process, a simple, dependable hydraulic-driven system gently lifts and empties the bag into the vessel. The operator controls the flow rate and discharge amount. (In a staged process, the proper weight of the raw material is emptied into an intermediate bag.) Later, when called for by the recipe, the intermediate bag is fully discharged into the receiving vessel by a simple Basic-Flo™ unloader.
Impact Examples at AZC
- Impact on Filling System: AZC has automated paper-bag filling lines that cost more than half a million dollars each to buy and install. Automated bag fillers involve high maintenance. Several thousands of dollars are spent monthly on the maintenance of the paper-bag filling lines, and when they go down, bottlenecks impact the entire plant. AZC indicates that a big-bag filling system costs less than $100,000 for even the most sophisticated system, and as little as $10,000 for the simplest system. Even in a bad month, the filler estimates that only hundreds of dollars are spent on maintenance of the big-bag filling system. The filler points out that intensive maintenance is part of any paper-bag filling system with a much higher chance of mechanical downtime.
- Impact on Workers: AZC has found it easier for its workers to fill big bags. Currently, plant operators are physically loading empty paper bags into the automated paper-bag filling system. If the automated paper-bag system breaks down, the worker has to stop feeding empty paper bags into the system and start troubleshooting. All this time, the worker and the plant are down. The benefit to the plant of the big-bag filling is that the workers can do more work in the production area while the sacks are filling. They have noted a much cleaner, neater, more organized production area since converting from paper bags to the Control- Flo sacks.
- Impact on Packaging Cost: AZC estimates paper bags typically cost about $0.40 each or about $17.00 for 2,100 lb. However, this does not include the cost of maintenance on the automated paper-bag filling line or the ripped bags that occur frequently on the paper-bag automated filling line. One ripped bag lost can mean $50 in lost revenue if the resin is priced at $1 per pound.
Also, this direct paper-bag cost does not include empty paper bags that are lost due to ripping, damage, aging, etc. Therefore, the actual cost of the paper bag is much higher than just the direct cost of procuring that paper bag and very competitive with the per-use cost of the Control-Flo bag solution.
- Impact on Waste: AZC has experienced no waste using the Control-Flo system.
- Impact on Traceability: AZC has been experiencing many requests for bar coding on its paper bags. Its traditional solution has been to bar code the stretch wraps around the palletized paper-bag stack. The problem its customers experience is that once the stretch wrap is removed, the bar code can easily be lost. Even if the bar code is preserved, the paper bags on the pallet tend to get pulled off and used, and the bags “scatter” with no traceability. AZC prefers one bar code placed on the big bag. That way, the material always travels in the same bag with the same bar code.
- Impact on Warehousing, Shipping and Standardizing: AZC double stacks the Control-Flo bag with a slip-sheet placed between the top of the bottom bag and the bottom of the pallet of the top bag. Since warehouse space is at a premium, this was important to AZC. As for shipping, the 2,100-lb bag is equivalent to most palletized paper bags and stacks in nearly the same footprint, so it is roughly equivalent and allows AZC to “max-weight” the truck. Finally, because the Control-Flo bag can be partially discharged to a specific weight, re-closed and restored at the discharger’s site, AZC benefits by filling to one standard size and stocking one standard package.
Conclusion
The benefits of a patient, ever-learning, long-term collaborative relationship between a manufacturer (BP), a raw-material supplier (AZC) and a solution provider (PPC), have yielded a finely tuned, semi-bulk material-handling solution that brings compelling and profound economic and ergonomic benefits, increasing customer service at all levels.The unique solution is portable and easy to use by plant operators, and requires low maintenance. Both raw-material suppliers and producers gain productivity, flexibility and safety through more efficient bag filling and unloading, more rapid recharging of valuable processing equipment, and reduced employee problems caused by long-term manual heavy lifting, all within current infrastructure and without costly plant modifications.
This article is based on a presentation made at the Adhesive and Sealant Council Fall 2000 Convention. Additional information on the Control-Flo™ semi-bulk, material-handling solution is available from Process Packaging & Control, Inc. (PPC), 6410H N. Business Park Loop, Park City, UT 84098; call 435-658-4900; fax 435-658-4499; e-mail tjpetracca@control-flo.com; or visit the Web site www.control-flo.com.
- Impact on Packaging Cost: AZC estimates paper bags typically cost about $0.40 each or about $17.00 for 2,100 lb. However, this does not include the cost of maintenance on the automated paper-bag filling line or the ripped bags that occur frequently on the paper-bag automated filling line. One ripped bag lost can mean $50 in lost revenue if the resin is priced at $1 per pound.
Looking for a reprint of this article?
From high-res PDFs to custom plaques, order your copy today!