
Silicone pressure-sensitive adhesives (PSAs) have been used for many years in areas where typical organic PSAs have failed. One of the most important uses is applications where large temperature extremes occur.
The composition of silicone PSAs parallels that of many common organic PSAs. The two main components that dictate the performance of the silicone PSA are a high molecular weight, linear siloxane polymer and a highly condensed, silicate tackifying resin (MQ resin). Figure 1 shows the structure of a typical silicone polymer. Commercially available silicone PSAs use either polydimethylsiloxane (PDMS) or polydimethyldiphenylsiloxane (PDMDPS) polymers that contain silanol functionality at the polymer chain ends.
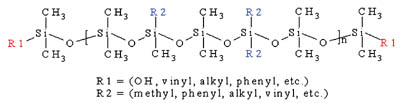
The silicate resin, often referred to as an MQ resin, is a solid particle supplied in a hydrocarbon solvent. The MQ name derives from the fact that its structure consists of a core of three-dimensional Q units (SiO4/2) surrounded by a shell of M units (Me3SiO). The resin also contains a level of silanol functionality on the surface. The ratio of M:Q is typically in the range of 0.6-1.2:1. Figure 2 shows a computer-generated molecular model of a silicate resin.


Adhesive Cure Chemistry
Although most silicone PSAs will exhibit pressure-sensitive behavior immediately after solvent removal, further crosslinking is done to reinforce the adhesive network. Two basic cure systems are commercially available for silicone PSAs: peroxide-catalyzed free-radical cure and platinum-catalyzed silicon hydride to vinyl addition cure. The majority of silicone PSAs available employ the use of a peroxide-catalyzed (benzoyl peroxide or 2,4-dichlorobenzoyl peroxide) free-radical reaction to achieve additional crosslink density. Curing of these types of adhesives is done in multi-zoned ovens due to the use of non-specific peroxides. Solvent removal is first required at lower temperatures (60-90 degrees C) to ensure the peroxide does not inadvertently cure solvent in the PSA matrix, which would result in reduced performance and poor temperature stability. At elevated temperatures (130-200 degrees C) the catalyst decomposes to form free radicals, which primarily attack the organic substituents along the polymer chains, extracting protons and generating free radicals.1The free radicals then combine to form crosslinks as shown in the graphic.




Discussion
In this study, four adhesives were evaluated: 1) a solvent-based, peroxide-catalyzed dimethyl silicone PSA, “commercial dimethyl”, 2) a solvent-based, peroxide-catalyzed diphenyl silicone PSA, “commercial diphenyl”, 3) a previously commercial solventless silicone PSA, “obsolete solventless” and 4) a new prototype solventless silicone PSA, “prototype solventless”. The peroxide catalyzed adhesives were prepared at 50 wt. percent solids in solvent using 2 wt. percent benzoyl peroxide based on the silicone solids. Figures 5-6 show the peel adhesion (PSTC-1) and probe tack performance (ASTM D 2979) for each PSA on two different substrates, respectively.
Comparison of these four adhesives on these figures illustrates an important point. The commercial dimethyl PSA is known in the marketplace to be an all-purpose adhesive, while the commercial diphenyl PSA is reputed to have excellent tack properties for a silicone. When the obsolete solventless was developed, it too had excellent tack and adhesion properties. The focus of making the current prototype was to de-emphasize the need for the best tack and adhesion performance but rather improve the high temperature performance. Although the tack and peel adhesion performance is slightly lower than the commercial diphenyl and that of the obsolete solventless, the performance is well within the acceptable range for a silicone PSA. The biggest step change for the prototype solventless exists in the high temperature area. Figure 7 shows the high temperature shear performance (PSTC-7) for each PSA.

Each material was also analyzed on the TA-XT2i Texture Analyzer4 as a supplement to traditional probe tack and peel adhesion data. Figure 8 shows the resulting output.

Additional evaluations of the prototype solventless have shown that this new PSA is also compatible with the industry standard, fluorosilicone-coated release liner system for silicone PSAs. Figure 9 displays the release profiles of each PSA. The commercial dimethyl, obsolete solventless and prototype solventless all show flat and consistent release across many delamination speeds.

Summary
Recent development work at Dow Corning has produced a new prototype solventless silicone PSA using the standard test methods of peel adhesion, probe tack and high-temperature shear. The texture analyzer has been further used to enhance the understanding of the structure/property relationships between the resin and polymer. The prototype solventless silicone PSA exhibits tack and peel adhesion properties that are typical of silicone PSAs, and most importantly, it also exhibits the high temperature shear performance that is required in many silicone PSA applications. The use of a platinum-cured solventless system also offers many advantages over that of a traditional peroxide-catalyzed system.Acknowledgements
The author wishes to acknowledge Glenn Gordon for discussions on the use of rheology for silicone adhesives, and Lacy Brondstetter and Patricia Moore for their formulation and testing work.References
1 Tangney, T. Silicone Pressure Sensitive Adhesives for High Performance Applications. Presented at Adhesives ’86 Conference, Baltimore, Sept. 1986.2 Sobieski, L. Formulating Silicone Pressure Sensitive Adhesives for Application Performance. In Technical Seminar Proceedings, Pressure Sensitive Tape Council, Itasca, IL, May 7-9, 1986.
3 Tangney, T. Adhesive Development Offers Low Temps, Savings. Paper, Film & Foil CONVERTER, Nov. 1990.
4 Stable Micro Systems, Godalming, Surrey, U.K.
5 Zosel, A. The Effect of Bond Formation on the Tack of Polymers. J. Adhesion Science and Technol., 11(11):1447-1457, 1997.
6 Zosel, A. The Effect of Fibrillation on the Tack of Pressure Sensitive Adhesives. International J. Adhesion & Adhesives, 18(4):265-272, 1998.
7 Zosel, A.; Molecular Structure, Mechanical Behaviour and Adhesion Performance of Pressure Sensitive Adhesives. Technical Seminar Proceedings, Pressure Sensitive Tape Council, Northbrook, IL, May 3-5, 2000.
Sidebar:
Benefits of the Prototype Silicone PSA
• Lower volatile organic content• Lower volatile siloxane content
• No cure byproducts
• Single-zone oven cure
• Fast cure
• Lower temperature cure
• Curable over a range of temperatures and times
• Reduced worker exposure to hazardous solvents
• “Primer-less” adhesion to substrates
• Wider range of backing materials possible
• Compatible with standard silicone PSA release system