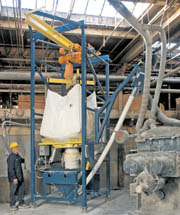
PHOENIXVILLE, PA - In producing epoxy mastic, Polymeric Systems Inc. was able to cut batching time from 3 to 1 1/2 hours by switching from manual emptying of 50-lb (28-kg) bags of dry inorganic powder to automated weigh batching directly from bulk bags. The system contained dust and ended the potential for injuries from lifting and emptying bags.
With the old system, operators dumped 50-lb (28-kg) sacks of dry inorganic powder (up to 32 bags per batch) into a 250-gal (950-L) kneader-extruder or one of two 100-gal (380-L) kneader-extruders. Today, three Flexicon bulk bag dischargers, each equipped with an 8-cubic-foot (226 L) capacity receiving hopper and 10 or 15 foot (3-4.5 m) long, 4.5-in (11.4 cm) diameter flexible screw conveyor, can unload powder from 2,500-lb (1,135-kg) bulk bags as the flexible screw conveyors convey the material at pre-selected batch weights to any of three kneader-extruders under loss-of-weight control.
Polymeric Systems Plant Manager John Kimmich first saw the equipment at a trade show. Flexicon simulated operating conditions for conveying the material in its Bethlehem, PA, test laboratory to verify system performance prior to fabrication.
"The system enables us to switch to different products and meet customer demand faster in OEM, do-it-yourself and retail markets," he said. From the labor savings and productivity gains, he expects the system to pay back in less than two years.
Batch Weights, Formulations Set in 60 Sec.
Because sack weights fluctuated by up to 5 lbs (2.25 kg), operators previously weighed each sack and adjusted for variations. Now, adjusting a batch weight, or selecting one of Polymeric's nine epoxy mastic recipes, requires a one-minute entry on the control panel. The operator is freed for other tasks rather than being tied to the batching process. The only manual task involves adding small amounts of minor fillers from 50-lb (28-kg) bags into the hopper, which is equipped with bag tray support and hinged cover.Weigh Batching System Accurate to +/-0.12%
A control panel entry initiates unloading of the bulk bag and conveying powder in precise weights to the kneader-extruder. As a bag empties, load cells supporting the discharger frame transmit weight-loss signals to the controller that step down the conveyor to a dribble feed rate immediately prior to stopping the conveyor once the accurate batch weight has been unloaded. Batches between 400 and 1,600-lb (180-720 kg) are accurate to 2 lbs (0.9 kg).Flow Promotion Devices Move Stubborn Powder
Flow promotion devices on the bulk bag discharger help promote a continuous flow of material into and through the bag discharge spout. A manual Spout-Lock‘ clamp ring mounted atop a Tele-Tube‘ telescoping tube creates a sealed connection between the clean side of the bag outlet spout and the clean side of the telescoping tube. Elongating the bag as it empties, the tube keeps the spout taut at all times, preventing excess spout material from bulging outward (creating dead pockets) or falling inward (creating flow restrictions).Flow-Flexer‘ bag activators raise and lower opposite bottom edges of the bulk bag at timed intervals, promoting material flow into the bag discharge spout. As the bag lightens, the stroke of the bag activators increases, raising the bag into a steep "V" shape for total evacuation of material.
A pneumatic turbine vibrator in the hopper promotes flow into the flexible screw conveyor's charging adapter.
For leak proof retying of partially empty bags, a Power-Cincher‘ flow control valve employs curved, articulated stainless steel rods to cinch the spout concentrically on a horizontal axis, and vertically in a tight zigzag pattern to prevent leakage of finest powders.
Dust-Tight System Prevents Contamination
The dry inorganic powder remains enclosed from bulk bag discharger, through hopper, flexible screw conveyor to kneader-extruder. Previous bag dumping in open air created dust and allowed paper scraps to enter the batch.Each flexible screw conveyor consists of a durable plastic outer tube enclosing a model 1450 conveyor spiral designed to accommodate the highly aeratable powder. Flexicon applications engineers also incorporated several design elements to overcome the challenges associated with handling the powder.
For more information, contact Flexicon Corp., 2400 Emrick Blvd., Bethlehem, PA 18020-8006; phone (610) 814-2400; fax (610) 814-0600; e-mail sales@flexicon.com ; or visit http://www.flexicon.com .