Controlling Rheology in Structural Adhesives
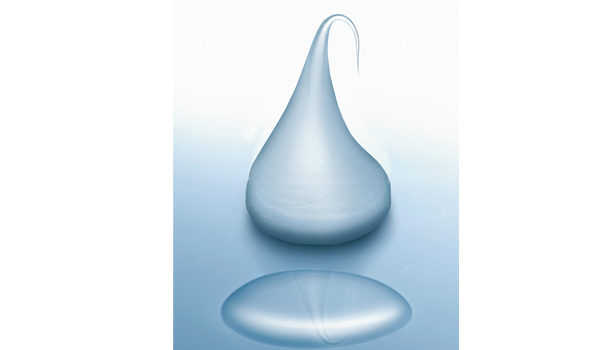







The directed assembly of fumed silica particles can be used to improve the rheology control of structural adhesives.
Line productivity and energy consumption for the modern automotive, transportation, aerospace and wind energy industries increasingly demand parts with lower weight that can also bear higher mechanical stresses. As such, structural joint design has rapidly evolved to meet these conditions. Today’s composite parts require larger joints, thicker bonding gaps, and challenging adhesive bead shapes to deliver optimal adhesion at much higher mechanical stresses in complex deformation modes. These changes, in turn, demand much higher performance from rheology control additives, providing higher yield stresses and faster recovery times from high to low shear, and viscosity stability over long periods of time.
Rheology control has become an enabling requirement for many one- and two-component structural adhesives that rely on low-molecular-weight polymeric liquids to provide the high degree of reactive functionality necessary for adhesion, fast curing, and high mechanical performance. For example, low-molecular-weight resins, epoxy, and urethane pre-polymers often exhibit low viscosity, nearly Newtonian flow, and negligible yield stress with the consequent impossibility to sustain required bead shapes for any relevant time.
Over the past decade, surface-modified fumed silica has become the rheology control agent of choice for these types of systems, given its ability to turn low-viscosity fluids into viscoelastic materials bearing high viscosity at low shear rates, large yield stress, and low viscosity at typical application shear rates (see Figure 1). This complex viscoelastic behavior, at silica loadings varying typically from 2-10% by weight, enables structural adhesives to be applied with low energies over large pumping distances and maintain bead shape for the required processing time—from minutes up to several hours—even for extremely large beads such as those found in auto joints and composite bonding pastes.
Directed Assembly
A new line of novel submicron fumed silica products has been developed with particle size, morphology, and surface chemistry designed to optimize the rheological behavior of epoxy bonding pastes employed in composite windmill blade fabrication* and epoxy structural adhesives for automotive, transportation, and aerospace applications.**
*Cabot Corp.’s CAB-O-SIL® ULTRABOND™ 4750
**Cabot Corp.’s CAB-O-SIL ULTRABOND 5760
The new products operate under the physical principles of particle self-assembly. They have been designed to rapidly self assemble in 3-D network structures when dispersed in liquid polymers with the physical and chemical qualities of epoxy resins. (This behavior is illustrated in Figures 2 and 3.)
By controlling the particle morphology and surface chemistry, the degree of compatibility has been tailored with the epoxy polymer matrix so that the particles assemble into these 3-D networks at the required rate after being mechanically dispersed in the formulation equipment. These 3-D networks are responsible for the complex viscoelastic behavior described above, conferred to the liquid epoxy system. As low as 3-4% by weight of these products with respect to the liquid epoxy resin is sufficient to create a fully percolated 3-D network and thus a viscoelastic fluid with two to six orders of magnitude higher low shear viscosity and large yield stress.
These networks are created by physical attraction forces between the particles and are rapidly broken upon application of high shear rates to the adhesive, as those found when it is being pumped and applied through a nozzle. With the 3-D network dissolved, the viscosity effect virtually disappears, thus allowing the adhesive to flow through the pipes and nozzle with minimum energy consumption.
Upon application of the adhesive bead at the flange or joint, and within a second after leaving the nozzle, the particles re-assemble in another 3-D network. The adhesive then becomes viscoelastic again, stays in place at the joint for minutes or hours, and develops the viscosity profile properties shown in Figure 4. This can be repeated with the same result for many cycles (e.g., day-to-day, shift-to-shift, or in a start-stop operation) with maximum reproducibility.
Performance in Demanding Applications
One of the most challenging applications is the production of composite blades for wind energy turbines. Airfoil blades for wind energy turbines are composite thermosetting materials greater than 60 m long and 20 tons in weight. They are molded as two separate halves by resin infusion and other open mold methods in the art. These two halves are then assembled with internal mechanical stability elements (spars) by bonding the blade halves and spars together with a thick structural adhesive known as a bonding paste. Bonding pastes are typically comprised of two-part epoxy/hardener systems. Due to the extreme mechanical stresses along the blades that are experienced in all forms of deformation as the blades rotate or hang idle, the adhesion and mechanical performance demand for these bonding pastes is considered one of the most challenging for adhesives applications.
To meet these performance challenges, the new self-assembled particles confer the resin with the highest yield stress, the highest viscosity stability, and extremely fast viscosity recovery rates. These rheological properties brought about by the particles’ directed self-assembly offer the epoxy bonding pastes multiple benefits during the different stages of the supply chain lifecycle.
Compared to current solutions in the industry, the treated fumed silica delivers 25-30% higher sag resistance, contributing to improved energy efficiency for wind blades. The new fumed silica also reduces the fumed silica content in the bonding paste formulation by 10-15%, providing the additional and important benefit of lower viscosity and easier application over the blades. By reducing the fumed silica processing time by 50% during the manufacturing stage (compared to competitive products in the market), the new fumed silica substantially reduces the total cycle time and creates an added benefit by enabling production of more adhesives using the same assets on the ground.
For additional information, contact Cabot Corp., Performance Segment, at 157 Concord Rd., Billerica, MA 01821; phone (617) 345-0100; email elizabeth.sims@cabotcorp.com; or visit www.cabot-corp.com.
Looking for a reprint of this article?
From high-res PDFs to custom plaques, order your copy today!