Ellsworth Adhesives Canada Launches Warehouse Management System
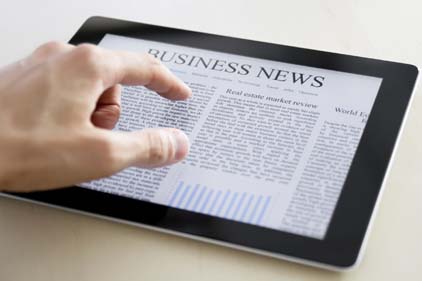
Ellsworth Adhesives recently announced that it has implemented a new warehouse management system (WMS) in its Canadian facility. The system is intended to help improve process times and the ability to provide best-in-class service to the company’s customers.
Ellsworth Adhesives Canada implemented a fully automated WMS. All items in the warehouse are bar coded and tracked through the system, which includes many checkpoints that require verification of inputs, reportedly resulting in higher quality outputs. The WMS allows the company to control inventory by item, lot/batch and shelf life, and systematically match those to individual customer requirements.
“In today’s markets, customers demand that their suppliers provide them with what they need, when they need it,” said Roger Lee, vice president of the Specialty Chemical Distribution. “The objective is to provide an enhancement that fully ensures a benefit to our customers and improves the products and services we provide. The successful implementation of this world-class WMS provides improved alignment within our North America distribution network. Platform consistency and process replication are fundamental keys to our operational goals that increase our efficiencies and add significantly higher customer value.”
For additional information, visit www.ellsworth.com.
Looking for a reprint of this article?
From high-res PDFs to custom plaques, order your copy today!