Q&A About Polyurethanes: Prepolymers with Low Isocyanate Content
What might cause problems with reproducibility in prepolymers with low isocyanate content?
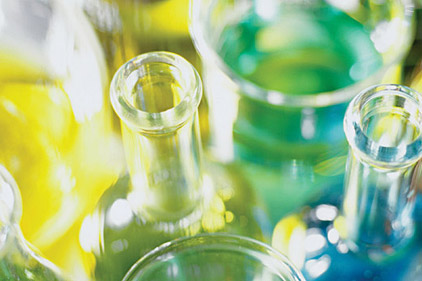
We manufacture prepolymers with an isocyanate content of 15-20% NCO using a variety of diphenylmethane-based isocyanates and polyether polyols. Business has recently picked up, and we have been asked to produce prepolymers with a low isocyanate content (~ 3%). Unfortunately, we are having problems with reproducibility. What might be causing this problem?
Since your company is making isocyanate prepolymers, you already have a fundamental understanding of the typical issues of controlling the mix ratio of isocyanate to polyol and the normal reaction temperatures used. But manufacturing low-isocyanate prepolymers (LNCO) presents special challenges. In general, it is necessary to more tightly control the entire production process. LNCOs are often used in applications that require flexibility and are frequently based on high-molecular-weight (> 4,000) difunctional polyether polyols. Raw material quality needs to be closely examined for the production of this class of isocyanate prepolymers. It is recommended that critical properties of the raw materials should be examined just before use, even if they are received within specification.
Water content of the polyether polyols is one such property. It should be consistently low to prevent undesirable side reactions, such as polyurea formation. Water has a very low molecular weight; a small amount of water can consume a large amount of isocyanate groups. This reaction with water reduces the molar ratio of isocyanate to polyol hydroxyl groups from the target value. The resulting prepolymer ultimately exhibits an increased viscosity along with an isocyanate content that is lower than desired. A 4,000-molecular-weight polyol that contains 0.1% water will produce a prepolymer with an isocyanate content of 2.6% (compared to 2.9% if the polyol has a typically specified water content of 0.03%). The polyureas generated by the reaction can also produce a cloudy prepolymer, so it is important to track the water content to determine if extra water is causing your quality problems.
Undesirable high water levels in the polyol may also occur through contamination by atmospheric moisture if the polyol container is repeatedly opened and closed. This could easily occur if small batches of prepolymers are being made and the polyol is supplied and stored in a tote rather than a drum, which could be used completely for one production run.
Tin catalysts can be used in the production of low-isocyanate prepolymers. In your situation, the reaction time to reach the target isocyanate content will be longer than that of a prepolymer with a higher isocyanate content, but a tin catalyst can be used to drive the reaction to completion more quickly. These catalysts can be deactivated by the presence of water—another reason to minimize the water content in the polyol.
Difunctional isocyanates are the reactant of choice for LNCO. They are preferred since they will produce prepolymers with the lowest viscosity. Isocyanates with functionalities even slightly greater than 2 will produce very high viscosity prepolymers or may even lead to a gelled reactor. For prepolymers based on diphenylmethane diisocyanate, it is worth considering the use of monomeric MDI with an enriched content of 2,4’-MDI. This starting raw material will produce a lower viscosity prepolymer, but the reactivity will be slower than a prepolymer based solely on 4,4’-MDI.
Any views or opinions expressed in this column are those of the author and do not represent those of ASI, its staff, Editorial Advisory Board or BNP Media.
Looking for a reprint of this article?
From high-res PDFs to custom plaques, order your copy today!