HUNTSMAN ADVANCED MATERIALS LLC: Aerospace Materials
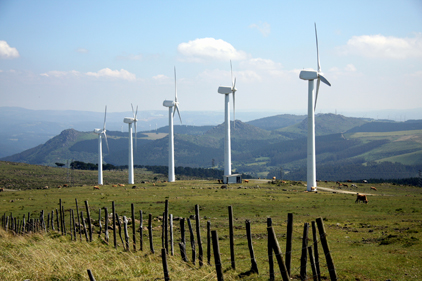
This company recently introduced five new products at SAMPE Seattle, which took place June 3-4. “Based on our long-term commitment to developing next-generation aerospace products, we are pleased to introduce five new materials that will enable our aerospace customers to fabricate and assemble tougher, longer-lasting composite components for structural and interior applications,” said Carl Holt, Marketing manager, Aerospace Components and Adhesives, and Automotive and Industrial Composites.
The new products are:
XU 35710 FST benzoxazine resin, a high-strength, flame-retardant material that is reportedly easier to process than conventional phenolics. It can be used for the production of aircraft interior parts such as overhead bins, floor and ceiling panels, and bulkheads that must meet the requirements of FAR 25.853.
RDS 2012-027 and RDS 2013-059 solid epoxy resins, which are specifically designed for producing adhesives and composite parts that retain very high tensile (8,044 psi) and flexural strengths (13,840 psi) at high 302°F (150°C) temperatures. The epoxy resin building blocks reportedly have a hot/wet glass-transition temperature of 428°F (220°C) and good chemical resistance.
Epibond® 200 A/B epoxy adhesive, reportedly a versatile system for bonding metals, composites and dissimilar substrates. It has a 1:1 resin:hardener mix ratio, an extended gel time of 100 minutes at room temperature, and offers a working life of 60-70 min. The flexible epoxy reportedly maintains a high lap shear strength of 3,160 psi at temperatures as low as -67°F/-55°C.
Epocast® 1645 FR A/B ultralow density epoxy edge filler, reportedly an easy-to-mix-and-apply syntactic that meets the requirements of FAR 25.853a for void filling and edge reinforcement of honeycomb structures used in aircraft interiors. The 0.48 g/cc material has a 65-min gel time and hardens to a sandable surface quickly.
For more information, visit www.huntsman.com.
Looking for a reprint of this article?
From high-res PDFs to custom plaques, order your copy today!