Henkel Opens Lab in Shanghai
Henkel recently announced it has opened a NVH lab located in the Henkel Adhesive Innovation Center in Shanghai, China.
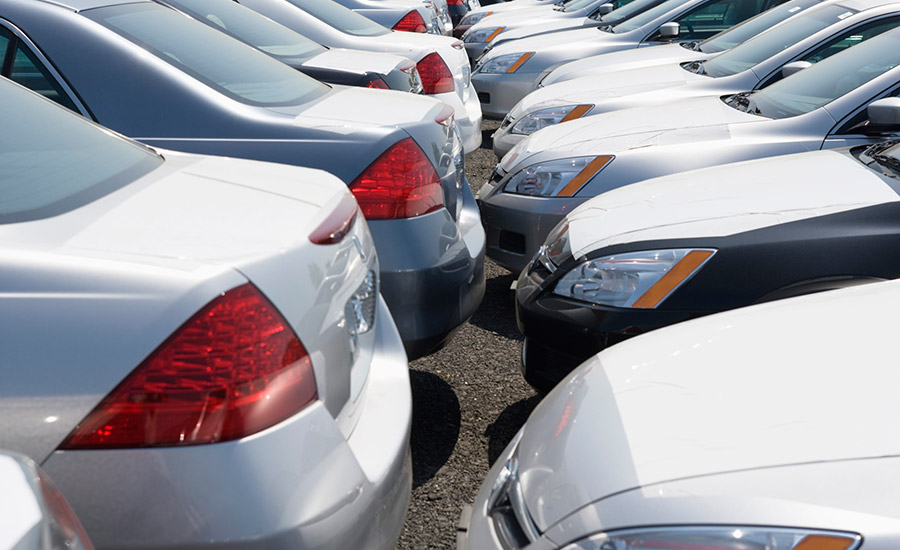
Henkel recently announced it has opened a NVH lab located in the Henkel Adhesive Innovation Center in Shanghai, China. The 400-sq-m facility intends to help the company to stay on top of automotive trends and offer OEM solutions to meet the requirements in the area of NVH.
The new NVH lab is dedicated to noise regulation testing and NVH quality improvement, with its state-of-the-art experimental and computational analysis facilities. The test lab features a full car body oven, a 3D printer, liquid-applied sound deadener (LASD) spray equipment, a mode test platform, a laser vibrometer, and anechoic rooms that are used to test vehicle NVH performance. For LASD and HDF new damping concept application, the latest test lab system, pulse analysis software and optical measuring systems are used to evaluate the vibro-acoustic performance of subsystem and vehicle level. The whole engineering chain from simulation, spray to validation can be done in the lab to meet OEMs’ quick response requirements and shortened DVP period.
“A concept that started as a whiteboard sketch can be quickly turned into a representative, physical part engineers can touch and feel [with 3D printing],” said Eric Aldstadt, acoustic and structural business director, Asia Pacific. “And, they can physically review Henkel’s part solution with their cross-functional team. A picture may be worth a thousand words, but the ability to hand our customer a physical part is truly top-notch engineering support. Henkel’s ability to manufacture 3D prototypes in one day solidifies our commitment to putting customers at the center of what we do.”
For more information, visit www.henkel.com.
Looking for a reprint of this article?
From high-res PDFs to custom plaques, order your copy today!