Integrating Adhesives with Assembly
Adhesives and tapes in durable assembly allow engineers to innovate.
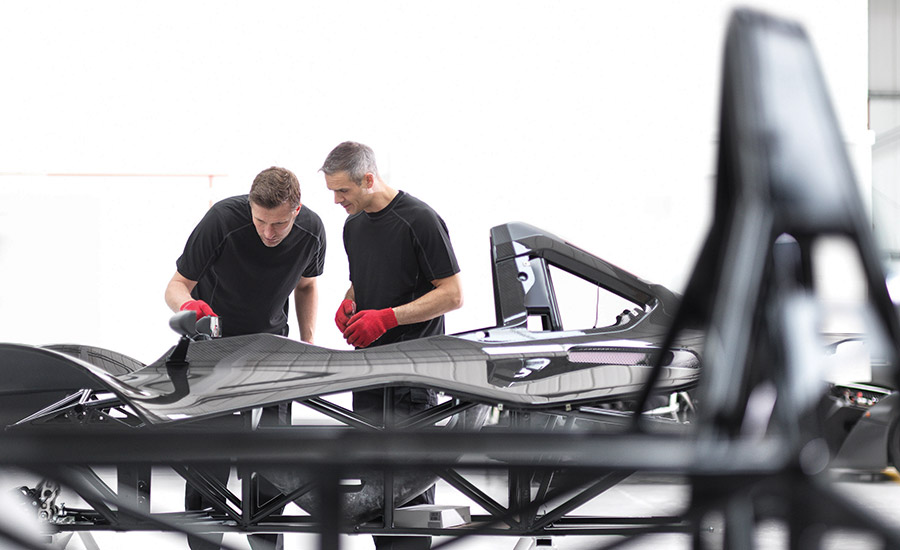
Multi-material designs are becoming increasingly common for industrial assemblies, with the growing incorporation of materials like integrated glass, structural composites, or scratch-resistant surfaces. Design engineers have gravitated toward these kinds of assemblies because of the potential benefits, including cost efficiency, weight reduction, performance improvement, and increased durability.
The challenge is that these kinds of designs often cannot be manufactured the same way and may require different methods of assembly. A “multi-material” design indicates that there will be a greater number of bond points where two materials must be joined, and traditional mechanical or thermal fastening techniques often cannot provide ideal performance. As such, many modern assemblies are evolving and must be manufactured using the technology of adhesive bonding.
The process for choosing the correct adhesive for an assembly is not the same as sizing a bolt to carry a load or deciding between a nail or a screw. There are many complexities to bonding with adhesives, such as the surface energy and joint stresses, which engineers can overlook.
Maximizing Contact Area
The most important considerations when designing with adhesives are to understand the properties of the substrate’s surface and to maximize contact between the adhesive and the substrate. To understand why this is important, we must first consider the mechanisms of the adhesion taking place. There are four commonly recognized mechanisms of an adhesive bond (in order from strongest to weakest): chemical via molecular contact; diffusion via solvating effects of adhesives; mechanical via interlocking with the micro-grooves of the surface; and electrostatic via positive/negative attractions between substrate and adhesive.
The strongest of these mechanisms is chemical. Chemical interactions occur on a molecular level at the interface of liquid/solid on the order of Avagadro’s Number (6.02 x 1023). By ensuring proper contact between liquid and solid, it encourages an increased amount of these chemical interactions. Changes in adhesive chemistry or surface modifications to the substrate can bolster the effects of the other mechanisms.
In order to maximize the contact area between adhesive and substrate, a liquid must be capable of flowing across, or wetting out, the substrate. If the surface of a substrate is examined at an atomic or molecular level, you will see that every substrate behaves differently—each has its own surface energy.
Surface energy is a measure of the sum of all intermolecular forces at the surface of a solid, as compared to its bulk. Strictly speaking, it is a measure of the energy required to create a unit area of surface of a material. (Units of surface energy are often presented in mJ/m2.) The surface energy of materials is a continuum, ranging from low to high. As a material’s surface energy increases, the more energetically favorable it becomes for a liquid to coat the surface. To put it another way, the higher the surface energy of the substrate, the more likely it is for the adhesive to wet-out.
The effects of surface energy can be observed by placing a droplet of liquid, typically water, onto the surface of a solid and measuring its profile. Water placed on a higher surface energy substrate will flow and create a film over the surface, while water on a lower surface energy substrate will bead up into a sphere. To compare these droplets, we consider a property called the contact angle, measured as the angle created at the solid/liquid/gas interface. The smaller the contact angle, the better that adhesive has wet-out the surface.
The contact angle is not affected by a substrate’s surface energy alone. Other contributors include the surface tension of the liquid and the interaction energy between solid and liquid at their interface. The contact angle—thus the wet-out of the adhesive—can be improved by manipulating any one of these variables. The most common methods of improving wet-out include either increasing the surface energy of the substrate or decreasing the interaction energy at the interface. Increasing the substrate’s surface energy can be done by plasma, flame or corona treatment. Decreasing the interaction energy can be done by chemically modifying the surface with a primer or by removing residue.
Another consideration when joining with adhesives is surface roughness. Abrasion of the substrate has many potential benefits. As previously mentioned, many of today’s materials are often supplied with an existing surface contaminant; removal of that contaminant is crucial for a strong bond. Abrasion also increases the total available surface area for an adhesive. If you were to microscopically examine one square inch of a substrate, it would be evident that scratches, dents and dimples create many tens or hundreds of square inches available for the adhesive to make contact. Abrasion increases the effective surface area by adding grooves and scratches into which the adhesive can permeate. The key is ensuring that the applied adhesive will wet-out across the surface, penetrating into each of these grooves and scratches.
Understanding Joint Stresses
A significant drawback of mechanical or thermal attachment is the concentration of stress that occurs at the point of the attachment. When stress is applied across the hole of a mechanical fastener, the stress is concentrated at the edges, potentially resulting in failure. On the other hand, an adhesive joint does not alter the substrate and allows the stress to be uniformly distributed across the entire region upon which force is exerted. This can increase the overall strength and durability of a joint.
However, there are different stress concentrations that can result in an adhesive failure. The stresses placed on adhesive joints can be classified into two types: one-dimensional and two-dimensional. One-dimensional stresses, such as peel or cleavage, concentrate
the stress along a leading edge of the bond. (Peel values for adhesives and
tapes are presented in units such as
lb/in. or N/mm) Two-dimensional stresses, such as tension, compression, or shear, concentrate the stress across the area of the bond. (Shear or tension values for adhesives and tapes are presented in units of lb/in.2 or N/mm2.)
Adhesives perform best when a joint is designed to place the stress in a two-dimensional load shear, compression, or tension. A strong adhesive joint uses this advantage and removes peel or cleavage. A joint that may be quite strong using a traditional mechanical or thermal attachment method must often be redesigned when using an adhesive in its place.
Once the design of the joint has been established, proper load and performance considerations are the next step in determining the adhesive that is best-suited for the application. As previously mentioned, an adhesive will perform differently from peel to shear, and certainly from adhesive to adhesive. Understanding the ranges of peel and shear strengths possible with different adhesive chemistries is crucial to a long-lasting design.
To definitively design and specify an adhesive for assembly, many other factors play a role in the decision. These factors may include adhesive application method, desired bond strength, temperature exposure, subsequent treatment and end use. However, the initial considerations will always be the same: maximize contact with the surface through careful consideration of adhesive and substrate surface preparation; and design the joint to employ the strengths of an adhesive, specifically, shear, tensile, or compression.
Whether designing a new part or redesigning an old one, the use of adhesives to incorporate multi-material assembly does not have to be a chore. Through careful consideration and effective use of resources available, adhesives and tapes in durable assembly allow engineers worldwide to open the door to unknown innovations. ASI
For more information, visit www.3m.com.
Looking for a reprint of this article?
From high-res PDFs to custom plaques, order your copy today!