Case Study
Controlling VOC Emissions from Silicone-Based Coatings
For processes such as tape manufacturing, a recuperative thermal oxidizer specially designed for high levels of silicone may be most effective.

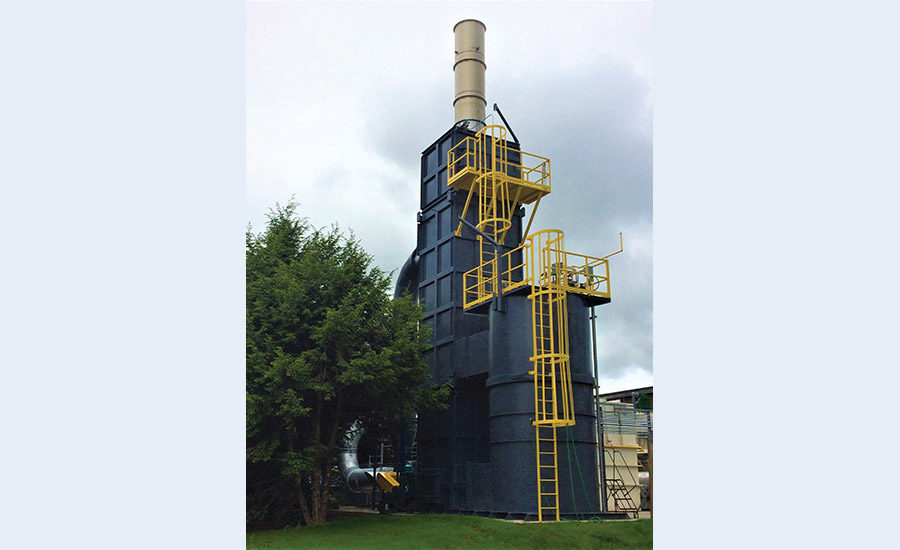
Thermal oxidation is the most widely accepted technology available to control VOC emissions from the manufacture and application of solvent-based coatings.


Silicone-based coatings are among the most versatile materials used in a variety of industrial applications, including pressure-sensitive tapes, protective coatings, and the protection of printed text on packaging. They are chosen over other materials for their technical and mechanical characteristics, as well as their flexibility. Silicone-based coatings have excellent properties such as strong adhesion to most substrates and high chemical, thermal, UV, and water resistance.
The application of these solvent, silicone-based paints, coatings, and adhesives releases significant levels of volatile organic compounds (VOCs) into the environment. When evaporated during the coating process, these VOCs react with nitrogen oxide (NOx) in the presence of sunlight to form ground-level ozone. As such, they are regulated as ozone precursors under the U.S. Environmental Protection Agency’s criteria pollution program. In sufficient quantities, VOCs can cause adverse effects on human health, including eye, nose, and throat irritations; headaches; dizziness; visual disorders; and memory impairment.
The web coating and converting industry is a primary user of silicone-based coatings and is therefore faced with many challenges to control these air emissions from the manufacturing process. Web coating or converting involves applying specialized coatings over a variety of substrates or webs, including paper, foil, plastic, film, metal, and wire. The coating process consists of applying a coating material to a moving web of flexible substrate. Different types of coating lines may be found in each application, but broadly speaking, each system is based on a roll design and consists of a metering system for applying the coating material to the substrate, followed by a drying tunnel to dry the coated web before it is rewound. The coatings provide the substrate with enhanced aesthetic and physical properties derived from the coating material.
Understanding Thermal Oxidation
Thermal oxidation is the most widely accepted technology available to control VOC emissions from the manufacture and application of solvent-based coatings. The oxidation of VOCs and other air pollutants works via a simple oxidation reaction of the harmful air pollutants with oxygen and heat. In this environment, the VOCs are converted to harmless inert byproducts like carbon dioxide (CO2), water vapor (H2O), and usable heat. These byproducts are released to the atmosphere or used within primary or secondary energy recovery techniques to further lower operational costs.
Although silicone additives may provide special properties and optimize processes, they also pose troubling issues for VOC control equipment. The basis for these problems stems from the oxidation process itself. Silicone is vaporized in the drying process, along with the VOCs, and is forced into the dryer exhaust. While the air pollution control equipment is installed to destroy the VOCs, any systems must be designed to also process the silicone vapors.
When heated above certain temperatures, silicone forms silicon dioxide (SiO2), an inorganic particulate that clings to hot metallic surfaces and forms a destructive and efficiency-robbing barrier layer. SiO2 can also poison the catalyst in a catalytic oxidizer (CatOx), affect regenerative thermal oxidizer (RTO) valving, and clog ceramic heat exchanger media. In a recuperative thermal oxidizer, SiO2 also creates boundary layers in the shell and tube heat exchangers.
Recuperative Thermal Oxidizers
For processes such as pressure-sensitive tape manufacturing that produce considerable amounts of particulate carryover or high SiO2 loadings, a recuperative thermal oxidizer specifically designed for high levels of silicone may be most effective. These thermal oxidizers are specially designed for fast and efficient cleanouts from SiO2 buildup.
A recuperative thermal oxidizer utilizes a combustion and dwell chamber coupled with a cylindrical design for the efficient destruction of VOCs. The design starts by drawing the VOC and silicone-laden process air stream into the high-temperature primary heat exchanger, where it is directed to the floating tube heat exchanger shell side. This eliminates any buildup on the outside of the tubes. The design pinpoints the tube velocities to minimize buildup, and specially designed plenums force drop-out and easy access for vacuum removal.
When the stream enters the floating tube heat exchanger, it is continuously preheated at close to the ignition temperature before being sent to the pre-heat burner. The exchange of energy in the primary heat exchanger makes up the basis for fuel savings and economical operation.
The process flow next enters the high-velocity combustion chamber. It travels down the elongated combustion chamber at high velocities, causing flame impingement and turbulence to occur and providing excellent mixing of the air stream. Next, the heated process stream enters the dwell chamber, where complete combustion of the VOCs occurs. Here, the silicone is converted to an inorganic particulate in the form of SiO2.
The particulate-laden air stream is then directed into the tubes of the floating tube primary heat exchanger. In the floating tube primary heat exchanger, the hot gases provide the energy transfer to the incoming gases, and the SiO2 begins to cling to hot metallic surfaces. By allowing the buildup to occur inside the tubes, a special tube cleaning device can be used to quickly clean the heat exchanger and restore the thermal efficiency to the original design. The cleaned exhaust is discharged to the atmosphere or to auxiliary heating systems such as secondary air-to-air recovery, air-to-water recovery, and air-to-oil recovery.
Case Study: Pressure-Sensitive Tape Manufacturer
At a pressure-sensitive tape manufacturer’s plant, the VOC emissions from two coating lines are controlled by a CPI silicone series recuperative thermal oxidizer. The thermal oxidizer destroys the VOC emissions from two ovens with 98% destruction rate efficiency (DRE).
In addition, a 7,000 SCFM baghouse dust collection system was installed to filter particulate matter (SiO2) during the “pre-start” purge of the oxidizer. When the oxidizer cools, residual SiO2 on the walls of the unit falls off and can exhaust to the atmosphere. The system is designed to filter particulate only upon a cold start condition when the blowers are first turned on, and the particulate matter is exhausted to the atmosphere.
Effective Air Pollution Control
Understanding the technologies that are available for air pollution control is a complicated endeavor. However, it is often necessary for complying with environmental regulations while maintaining the reliable operation necessary to meet production requirements.
For more information, contact the author at (847) 550-4106 or sklostermeyer@cpilink.com, or visit www.cpilink.com.
Looking for a reprint of this article?
From high-res PDFs to custom plaques, order your copy today!