Huntsman Develops Materials to Boost Battery Performance and Protection
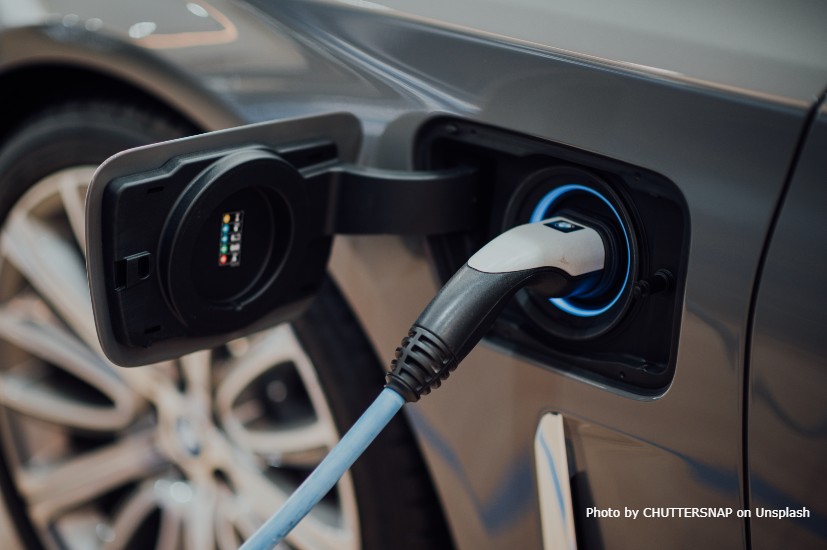
In a move to help deliver high-performance composite battery structures, alongside design and production flexibility, Huntsman has assembled a portfolio of customizable, quick-cure, high-strength polyurethane and epoxy resins that can be used to create underbody and top cover battery protection components up to 30% quicker than some existing technologies. The products can also lower overall part weight and increase strength and structural performance.
A range of products is currently available covering various battery performance and protection needs.
Targeting underbody battery protection, Huntsman offers RIMLINE® WCM system – a low-viscosity liquid resin that enables molding of high fiber volume fraction composites under low pressure. With a long working life, short cure time, and easy mold release, this system, formulated for use on high pressure-mix machines, reduces cycle times.
For battery enclosures, ARALDITE® FST resins allow the design of a flame retardant composite. These OEM- qualified systems have proven performance and reliability, meeting battery safety requirements.
Targeting battery underfloor protection, Huntsman has developed three products: RIMLINE FC (foam core) system, offering a cost-effective solution for manufacturing sandwich composites; RIMLINE LFI (long fiber injection) resin system, for molding strong parts with an example density of 1100 kg/m3 including 30% glass fiber reinforcement; and ARALDITE® 3031 / 3032 WCM systems, which in operation, combine the fastest processing cure time with high-quality mechanical properties and stiffness.
Targeting top cover applications, the VITROX® WCM system enables the development of composite lid structures that can help achieve thermal resistance while reducing weight compared to metallic covers. ARALDITE® SMC solutions enable part design freedom for semi-structural applications and requirements.
In the electric vehicle battery cell, Huntsman has developed a range of materials that help with lightweighting and improved conductivity, as well as thermal, vibration, and structural protection.
SHOKLESS™ encapsulation foam and elastomer systems help to create potting foams and encapsulants that are mechanically strong and have the thermal insulation and vibration dampening properties needed to protect batteries at a cell, module, and pack level.
ARATHANE® thermally conductive adhesives and encapsulants provide mechanical fixation and thermal connection, enabling effective heat management from the cells and enabling new battery pack designs and higher performance.
To increase the capacity or reduce the weight of the cells, Huntsman has introduced MIRALON® NMP Dispersions and MIRALON® Current Collectors. The MIRALON NMP Dispersions for LFP and high-nickel cathodes offer high conductivity with lower concentration than carbon black and are rate performance-compatible with fast charging protocols. MIRALON Current Collectors for ultra-lightweight applications can replace heavier metallic current.
Irina Bolshakova, global strategic marketing lead for Automotive Polyurethanes at Huntsman, said: “As demand for electric vehicles grows, we’re continually innovating, making it easier than ever for battery manufacturers, automotive OEMs and their suppliers to make new gains in powertrain performance. We’re excited to share details of our new systems.”
To learn more, visit www.huntsman.com/markets/automotive-and-transportation/automotive/battery-materials.
Looking for a reprint of this article?
From high-res PDFs to custom plaques, order your copy today!